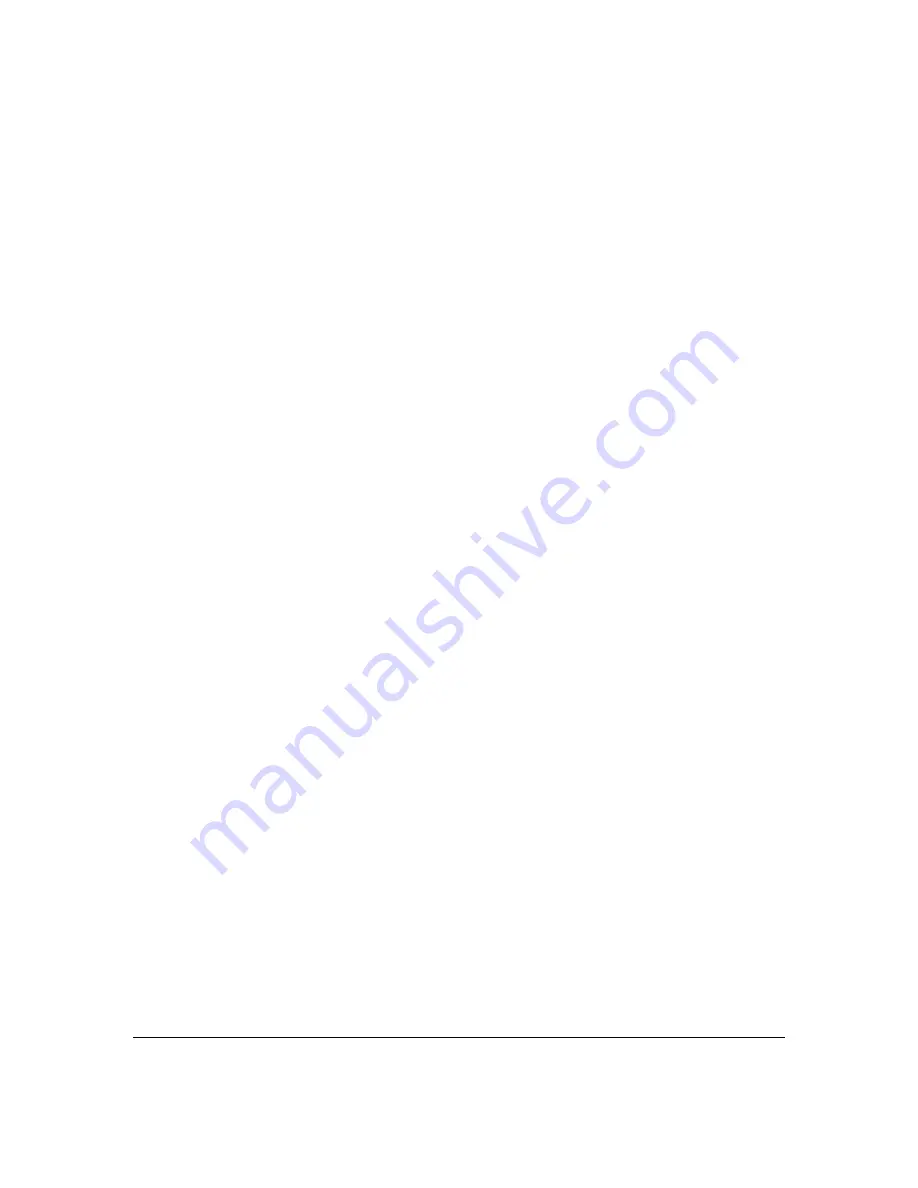
Revision 5
18
August 2021
1.6
Contents of this Manual
This manual contains the following information:
Section 1
: 943-TGXeNA Tail Gas Analyzer Introduction
presents introductory information
about the analyzer system.
Section 2:
Installation
describes unpacking the analyzer, installing it in the facility and
interfacing with other devices.
Section 3:
Operation of the System
explains how the operator interacts with the analyzer.
Section 4:
Local System Control
describes how the user enters data and views system
parameters using the keypad and the local display
Section 5
:
Web-based Graphical User Interface
describes how to operate the analyzer
and edit the analyzer configuration using the web-based graphical user interface.
Section 6
:
Maintenance
describes the various regular maintenance procedures that
should be followed to keep the analyzer functioning normally.
Section 7:
Service
gives some important service procedures that may be necessary to
keep the analyzer in operational condition.
Section 8:
Product Quality Assurance
includes various documentation of the Quality
Assurance that was done at the factory prior to shipping
.
Section 9:
Drawings
gives a variety of generic drawings related to the analyzer system.
Section 10:
Spare Parts
lists a number of items which may be required to maintain
operation of the analyzer.
Section 11:
Specifications
presents the specifications for the analyzer.
Section 12:
Input / Output Board Configuration
provides information for the testing and
calibration of the various inputs and outputs available on the analyzer’s IO board.
Summary of Contents for 943-TGXeNA
Page 130: ...Revision 5 130 August 2021 Figure 82 Oven Cabinet Door Removed ...
Page 131: ...Revision 5 131 August 2021 Figure 83 Control Cabinet Door Removed ...
Page 132: ...Revision 5 132 August 2021 Figure 84 Power Steam Air Signals Connection Details ...
Page 133: ...Revision 5 133 August 2021 Figure 85 AC Wiring Schematic ...
Page 134: ...Revision 5 134 August 2021 Figure 86 DC Signals and Wiring Diagram ...
Page 135: ...Revision 5 135 August 2021 Figure 87 Flow Diagram ...