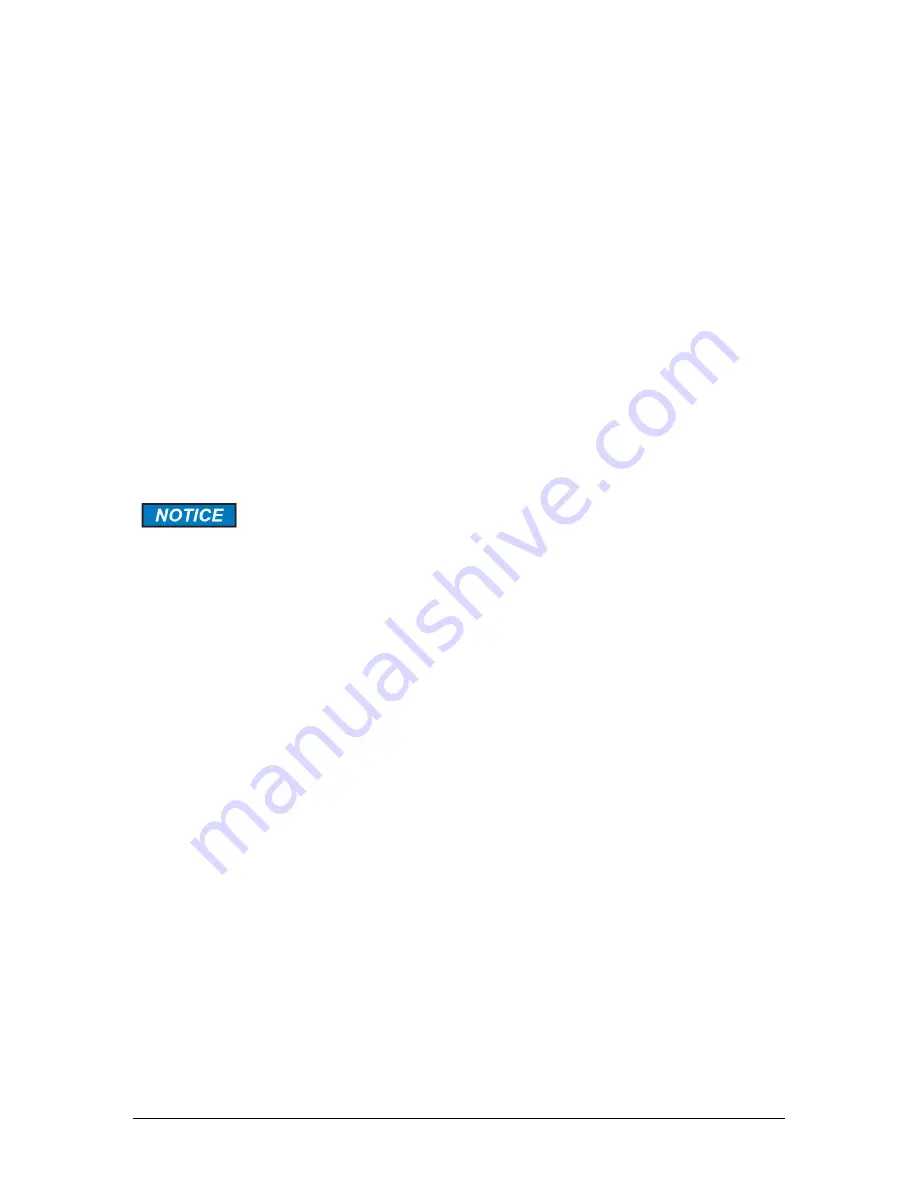
Revision 4
72
August 02, 2019
6.4 Optimizing the Spectrometer Energy Level
Optimization of the Spectrometer Energy Level is periodically required to maintain a sufficient
signal to noise ratio on the spectrometer output signal as the spectral output signal from the
spectrometer will deteriorate over time. The normal causes of this deterioration are:
•
Degrading Anti-Solarant Solution
•
Aging UV Source Lamp (output reduces over time)
•
Dirty cell windows
•
Dirty optics
•
Optical fibre problem
For convenience, the energy level of the spectrometer output signal is gauged by observing
the peak level as displayed on the Spectrum panel of analyzer or the Analysis/Spectrum
page on the Web GUI. When optimizing the spectrometer signal, the normal target value for
the peak value is 32000 counts (+/- 500).
The spectrometer energy level can be optimized manually (for special cases), or
automatically as a function of the analyzer. The automatic function will always target 32000
counts.
Before proceeding with either procedure below, ensure that the analyzer is
‘Off Line’ and purged with zero gas.
6.4.1 Automated Optimization
a) Place the analyzer in back purge mode. This can be done by accessing the
Back Purge
field on the
Analysis 1
panel and pressing
Enter
to place an
X
in the box.
b) Access the
Spectrum
panel, navigate to the
Optimize Integ Time
field and press
Ente
r.
c) Return to the
Analysis 1
Panel.
d) Request a Manual Zero by navigating to the “Manual Zero” field and pressing Enter.
e) Remove the Zero mode by accessing the
Sample
field and then pressing Enter to put an
x in the box, thus allowing the analyzer to return to normal sampling.
Summary of Contents for 943-TGX
Page 48: ...Revision 4 48 August 02 2019 Figure 4 13 Network Sub Panel...
Page 94: ...Revision 4 94 August 02 2019 Figure 9 3 Control Cabinet Detail...
Page 96: ...Revision 4 96 August 02 2019 Figure 9 5 AC Wiring Diagram...
Page 97: ...Revision 4 97 August 02 2019 Figure 9 6 DC Signal and Wiring Diagram...
Page 98: ...Revision 4 98 August 02 2019 This Page Intentionally Blank...