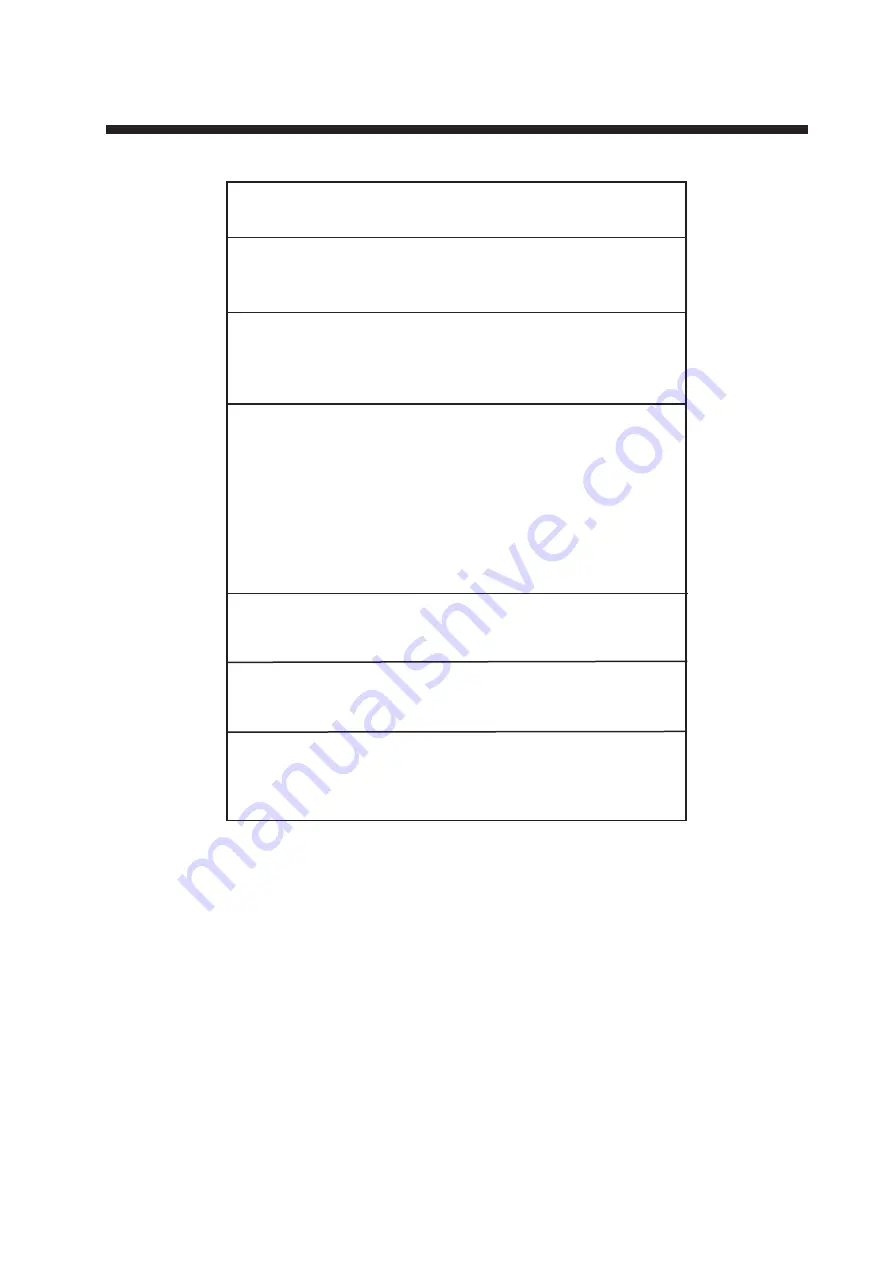
1-1
1.
MOUNTING
Be sure the power supply matches equipment voltage rating.
Improper power supply will damage the equipment.
Locate the transducer where the affects of noise and
air bubbles are minimal.
Noise and air bubbles will affect performance.
When selecting a mounting location keep the following points
in mind:
▪ Keep equipment out of direct sunlight.
▪ Keep equipment away from air conditioner.
▪ The useable temperature range of the display unit is 0°C - 50°C.
▪ Provide sufficient ventilation.
▪ Select location where vibration is minimal.
▪ Locate the equipment away from magnets or equipment generating
magnetic fields.
Keep the transducer cable away from oil.
Oil can corrode the cable.
Do not expose the transducer to hot water.
Hot water can damage the transducer.
Do not turn on the equipment with the transducer
exposed to air.
Exposing the transducer to air may damage it.
NOTICE
Summary of Contents for CSH-5LMARK-2
Page 8: ...EQUIPMENT LISTS vi This page is intentionally left blank ...
Page 26: ...1 MOUNTING 1 18 This page is intentionally left blank ...
Page 54: ...3 ADJUSTMENTS 3 8 This page is intentionally left blank ...
Page 60: ...AP 6 ...
Page 61: ......
Page 62: ......
Page 63: ......
Page 64: ......
Page 65: ......
Page 66: ...This page intentionally left blank ...
Page 67: ......
Page 68: ...8 May 2013 H MAKI D 2 ...
Page 69: ......
Page 70: ......
Page 71: ......
Page 72: ......
Page 73: ......
Page 74: ......
Page 75: ...D 9 ...
Page 76: ......
Page 77: ......
Page 78: ......
Page 79: ......
Page 80: ......
Page 81: ......
Page 82: ......
Page 83: ......
Page 84: ...D 18 ...
Page 85: ......
Page 86: ......