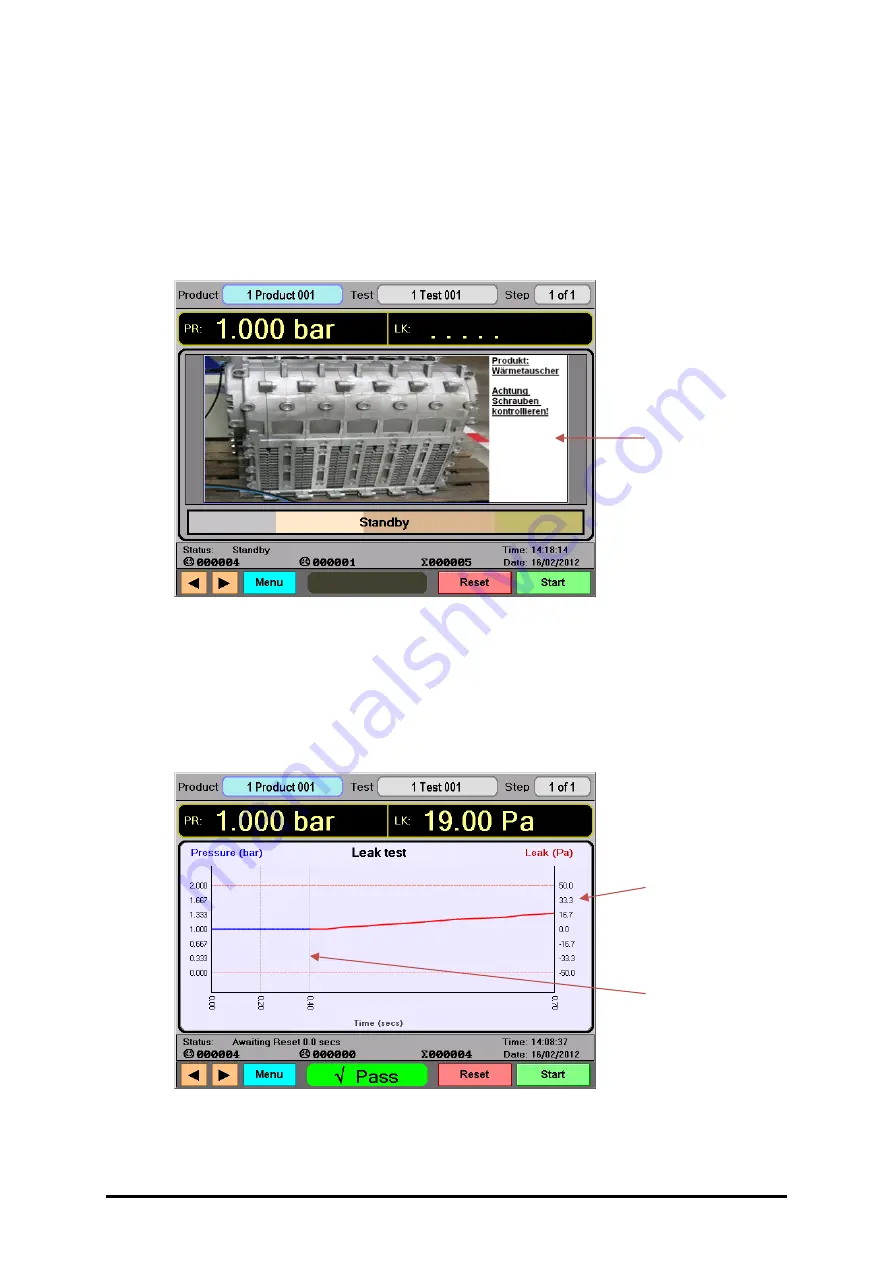
FCO770 Users Guide Issue 1
Page 23
There are various alternative views that may be selected using the
NEXT
and
LAST
buttons in
the lower status window, these are as follows:
DEFAULT DISPLAY
•
The default display shows when the instrument is first powered on. It shows a
customizable graphics area that can be programmed by the user through a USB
memory stick to show up to 300 individual colour images (1 for each test available).
This could be used to present operators with graphical/textual guides on any manual
interaction needed within various stages of a product under test.
GRAPH DISPLAY
•
Shows a graph plotting the various stages of a test in real time whilst the test is
running. Pressure readings are plotted in blue with their scaling shown against the left
vertical axis. Leak readings are plotted in red with their scaling shown against the
right vertical axis. The horizontal axis is pre-scaled to show the length of the full test
in seconds with vertical sub-division lines and times to mark each stage of the test.
•
The graph plot will automatically clear when a test cycle ends and its axis will
automatically scale itself when a test starts.
Customizable user
graphic showing
for test 1.
Dashed test stage division
lines indicate when a new
test stage starts
Axis are automatically
scaled when a new test
Starts.
Summary of Contents for FCO770
Page 2: ......