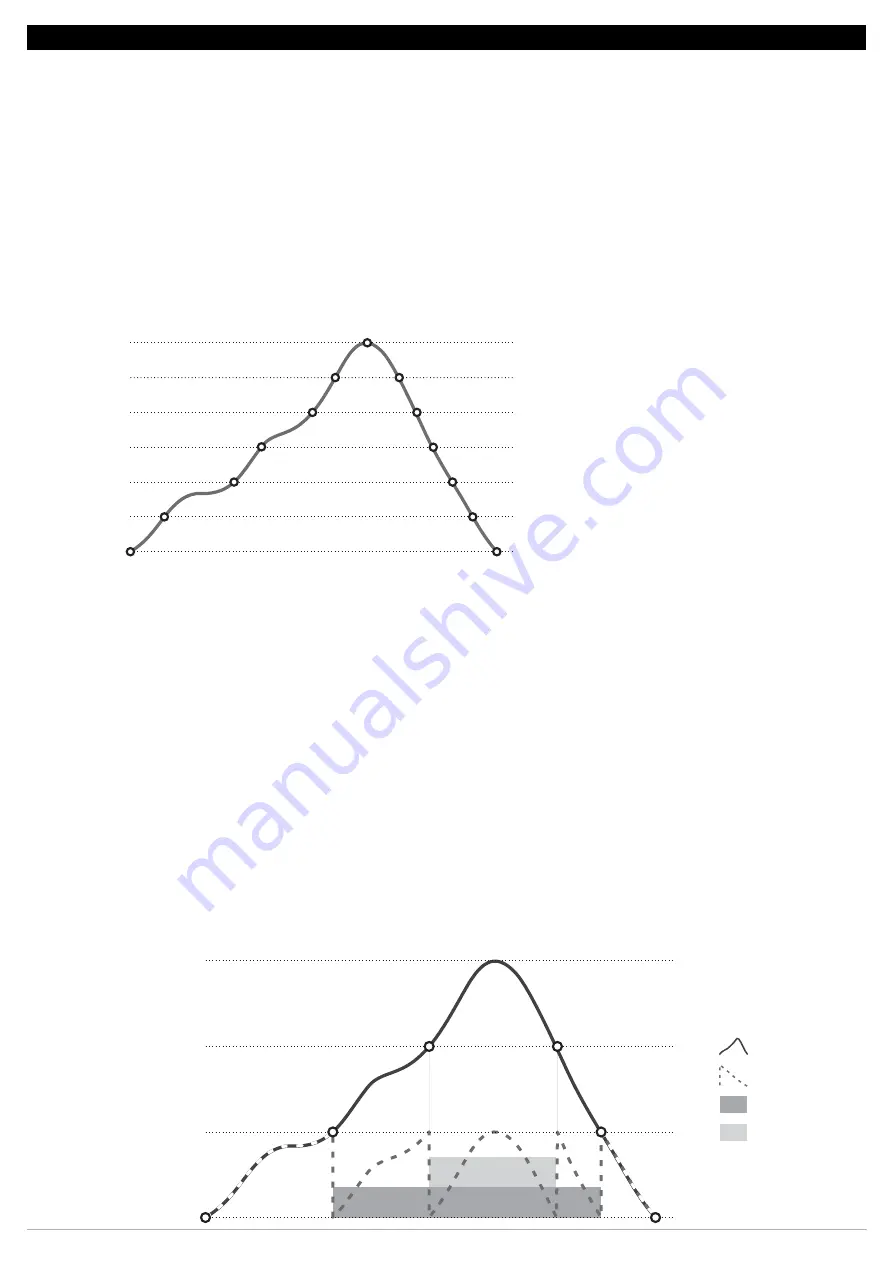
18
14.SUCTION CONTROLS
Example:
Linear control associated with digital outputs of compressors with unloaders
Compressors with unloaders.
When compressors with unloaders are used in linear mode, all the main compressor outputs are activated first and then the unloaders are
used.
1.2.x.2
Control mode: Linear
1.2.x.3
Setpoint: 25 psi
1.2.x.5
Digital hysteresis: 6 psi
1.2.x.15
Number of compressors: 6
1.2.x.22
Modulation of compressor 1: ON I OFF (0 I 100)
Compressor 1 is associated with one digital output only. Compressor 2 has one unloader valve, so it is associated with two digital outputs (main and
auxiliary 1). Compressor 3 has two unloader valves, so it is associated with three digital outputs (main, auxiliary 1 and auxiliary 2). The total number of
digital outputs is six and the step is defined as: 6/6 = 1 psi.
14.4.1.2 Linear mode using a proportional compressor (inverter) in conjunction with compressors associated with digital
outputs:
Compressor 1 of each suction can be proportionally controlled when configured as inverter and associated with a 0-10 V proportional
analog output. For this, you must select the modulation of compressor 1 as inverter and assign an analog output to it. The use of a control
output with Start-stop function in conjunction with the inverter compressor is optional. The Start-stop output must be selected as the main
output of compressor 1.
When the inverter compressor works in conjunction with compressors linked to digital outputs - with unloaders or not - the control is done
using one setpoint value and two hysteresis. The hysteresis of the analog output corresponds to the pressure interval for the control of the
inverter compressor output, and the hysteresis of the digital outputs corresponds to the interval of all compressors using digital outputs.
The inverter compressor is the first to be activated and the last to be deactivated and the other compressors will be started after reaching
their maximum capacity. For each compressor or unloader that is activated, the output of the inverter compressor is reduced to
compensate for the added portion. Similarly, when a compressor or unloader valve is switched off, the analog output value is increased to
compensate for the portion that has been reduced.
Example:
1.2.x.2
Control mode: Linear
1.2.x.3
Setpoint: 25 psi
1.2.x.5
Digital hysteresis: 4 psi
1.2.x.6
Analog hysteresis: 2 psi
Compressor 1 (proportional) uses an analog output (0-10 V), and compressors 2 and 3 use one digital output each. The step of the digital outputs is
defined as: 4/2 = 2 psi
25
26
27
28
29
30
31
(psi)
Pc1
Pc1 + Pc2
Pc1 + Pc2 + Pc3
Pc1 + Pc2 + Pc3 + U1c2
Pc1 + Pc2 + Pc3 + U1c2 + U1c3
Pc1 + Pc2 + Pc3 + U1c2 + U1c3 + U2c3
OFF
Digital outputs
Pc1 = Main output of compressor 1
Pc2 = Main output of compressor 2
Pc3 = Main output of compressor 3
U1c2 = Auxiliary output 1 of compressor 2
U1c3 = Auxiliary output 1 of compressor 3
U2c3 = Auxiliary output 2 of compressor 3
1.2.x.23
Modulation of compressor 2:0 I50 I 100
1.2.x.24
Modulation of compressor 3: 0 I 33 I 66 I 100
1.2.x.29
Modulation of compressor 2: Incremental
1.2.x.30
Modulation of compressor 3: Incremental
1.2.x.15
Number of compressors: 3
1.2.x.22
Modulation of compressor 1: Inverter
1.2.x.23
Modulation of compressor 2 = 0 I50 I 100
1.2.x.24
Modulation of compressor 3 = 0 I 33 I 66 I 100
Ac1
Pc2
Pc3
(psi)
Ac1 = 0% -> 100%
Ac1 = 0% -> 100%
Pc2
Ac1 = 0%
Ac1 = 100%
Pc2 + Pc3
Ac1 = 100% -> 0%
Pc2 + Pc3
Ac1 = 100% -> 0%
Pc2
Ac1 = 0%
25
27
29
31
psi