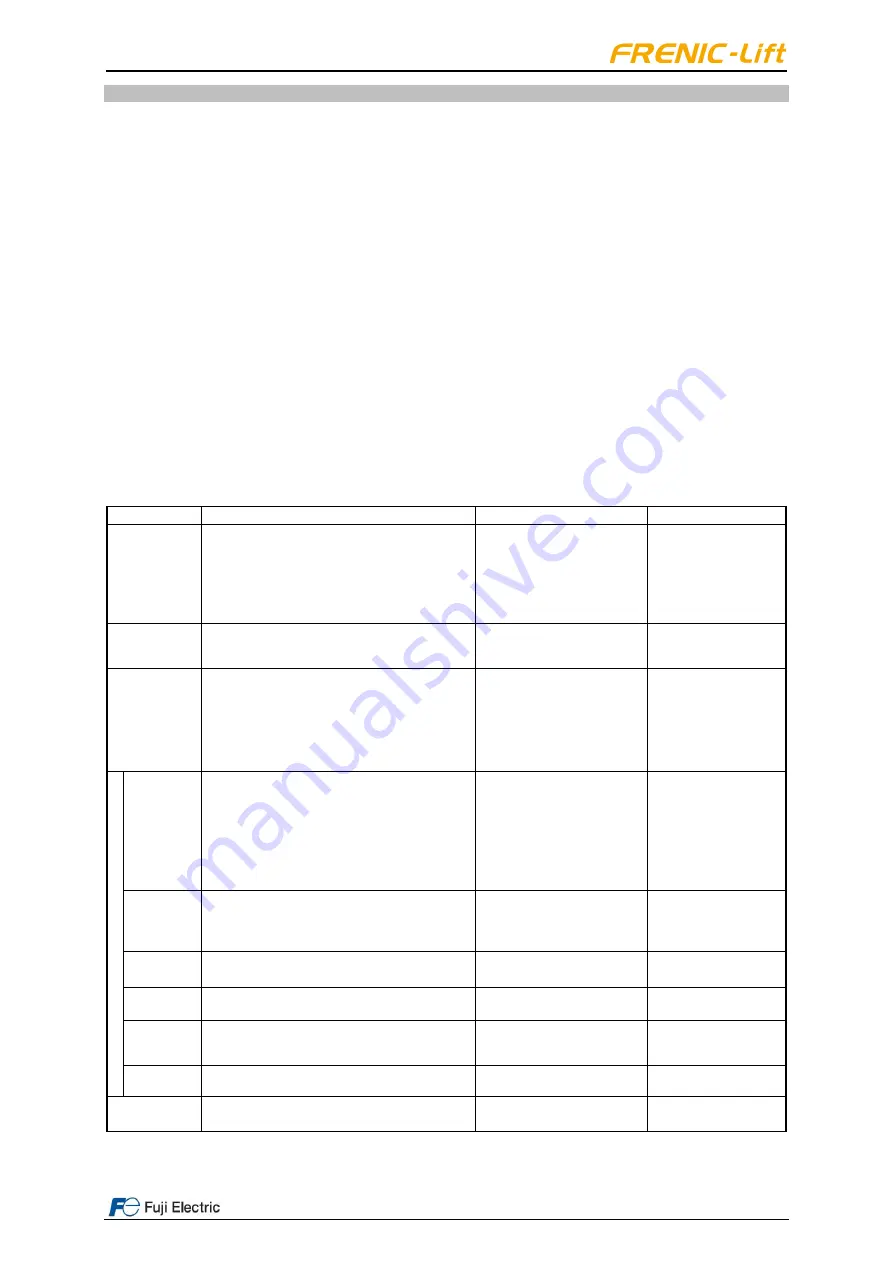
LM2A Wall Mounted Solution
Page
17
of
20
Fuji Electric Europe GmbH
4. Maintenance and Inspection
Perform daily and periodic inspections to avoid trouble and keep reliable operation of the inverter and components
for a long time.
4.1 Daily Inspection
Visually inspect the inverter and other components for operation errors from the outside without removing the covers
when the inverter is ON or operating.
-
Check that the expected performance (satisfying the standard specifications) is obtained.
-
Check that the surrounding environment satisfies the environmental requirements given in Chapter 2, Section
2.1.
-
Check that the keypad displays normally.
-
Check for abnormal noise, odor, or excessive vibration.
-
Check for traces of overheat, discoloration and other defects.
4.2 Periodic Inspection
Before starting periodic inspections, be sure to stop the motor, shut down the power, and wait at least 10 minutes.
Make sure that the charging lamp on the inverter is turned OFF. Further, make sure, using a multimeter or a similar
instrument, that the DC link bus voltage between the main circuit terminals P(+) and N(-) has dropped to the safe
level (+25 VDC or below).
For the complete list of inverter periodic inspection, refer to the FRENIC-Lift LM2A series Instruction Manual.
Table 4.1 List of Periodic Inspections
Check part
Check item
How to inspect
Evaluation criteria
Environment
1) Check the ambient temperature, humidity,
vibration and atmosphere (dust, gas, oil mist, or
water drops).
2) Check that tools or other foreign materials or
dangerous objects are not left around the
equipment.
1) Check
visually
or
measure using apparatus.
2) Visual inspection
1) The
standard
specifications must be
satisfied.
2) No
foreign
or
dangerous
objects
are left.
Input voltage
Check that the input voltages of the main and
control circuit are correct.
Measure the input voltages
using a multimeter or the like.
The
standard
specifications must be
satisfied.
Structure such
as frame and
cover
Check for:
1) Abnormal noise or excessive vibration
2) Loose bolts (at clamp sections).
3) Deformation and breakage
4) Discoloration caused by overheat
5) Contamination and accumulation of dust or
dirt
1) Visual or auditory
inspection
2) Retighten.
3), 4), 5)
Visual inspection
1), 2), 3), 4), 5)
No abnormalities
Ma
in
c
ir
c
u
it
Common
1) Check that bolts and screws are tight and
not missing.
2) Check the devices and insulators for
deformation,
cracks,
breakage
and
discoloration
caused
by
overheat
or
deterioration.
3) Check for contamination or accumulation of
dust or dirt.
1) Retighten.
2), 3)
Visual inspection
1), 2), 3)
No abnormalities
Conductors
and wires
1) Check conductors for discoloration and
distortion caused by overheat.
2) Check the sheath of the wires for cracks and
discoloration.
1), 2)
Visual inspection
1), 2) No abnormalities
Terminal
blocks
Check that the terminal blocks are not
damaged.
Visual inspection
No abnormalities
Reactor
Check for abnormal roaring noise and odor.
Auditory,
visual,
and
olfactory inspection
No abnormalities
Magnetic
contactors
1) Check for chatters during operation or
vibrations.
2) Check that contact surface is not rough.
1) Auditory inspection
2) Visual inspection
1), 2) No abnormalities
Main switch 1) Check that it is not damaged.
2) Check that it can change the position.
1),
2) Visual or auditory
inspection
1), 2) No abnormalities
Cooling
system
Check the heat sink, intake and exhaust ports
for clogging and foreign materials.
Visual inspection
No abnormalities
Remove dust accumulating on the inverter and other components with a vacuum cleaner. If a component is stained,
wipe it off with a chemically neutral cloth.