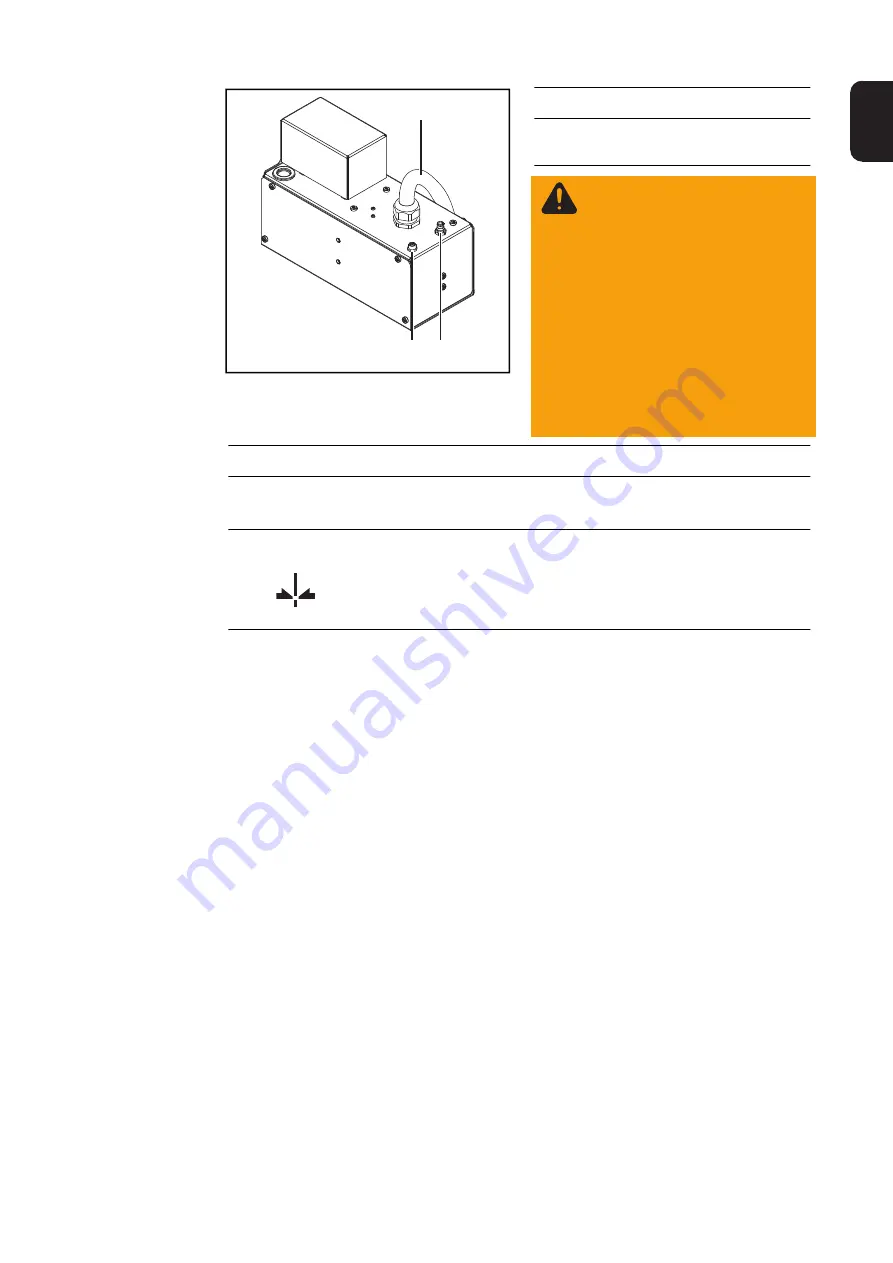
33
EN-US
Underside of the cleaning unit
No.
Function
(3)
Interconnecting hosepack
For connecting to the base unit
WARNING!
Danger of serious in-
jury and damage from electric
shock. Once the ready to clean in-
dication lights up, do not disconnect the
interconnecting hosepack from the base
unit.
Before disconnecting the interconnecting
hosepack:
-
Disconnect the base unit power sup-
ply
-
Disconnect the base unit compressed
air supply
No.
Function
(4)
Parting agent atomizer connection socket
For connecting to the ‘Robacta Reamer’ parting agent container
(5)
Wire cutter connection socket
For electrically controlling the wire cutter
(4)
(5)
(3)
Summary of Contents for Cleaning Unit TC 2000
Page 2: ...2...
Page 4: ...4...
Page 15: ...General...
Page 16: ......
Page 24: ...24...
Page 25: ...Operating controls connections and mechanical components...
Page 26: ......
Page 34: ...34...
Page 35: ...Installation and Startup...
Page 36: ......
Page 43: ...43 EN US 4 Tightening torque 1 3 Nm 5 Tightening torque 0 5 Nm 6 4 1 5 1 2 3 4 6...
Page 52: ...52...
Page 53: ...Troubleshooting Maintenance and Disposal...
Page 54: ......
Page 61: ...Technical Data...
Page 62: ......
Page 65: ...65 EN US...
Page 66: ...66...
Page 67: ...67 EN US...