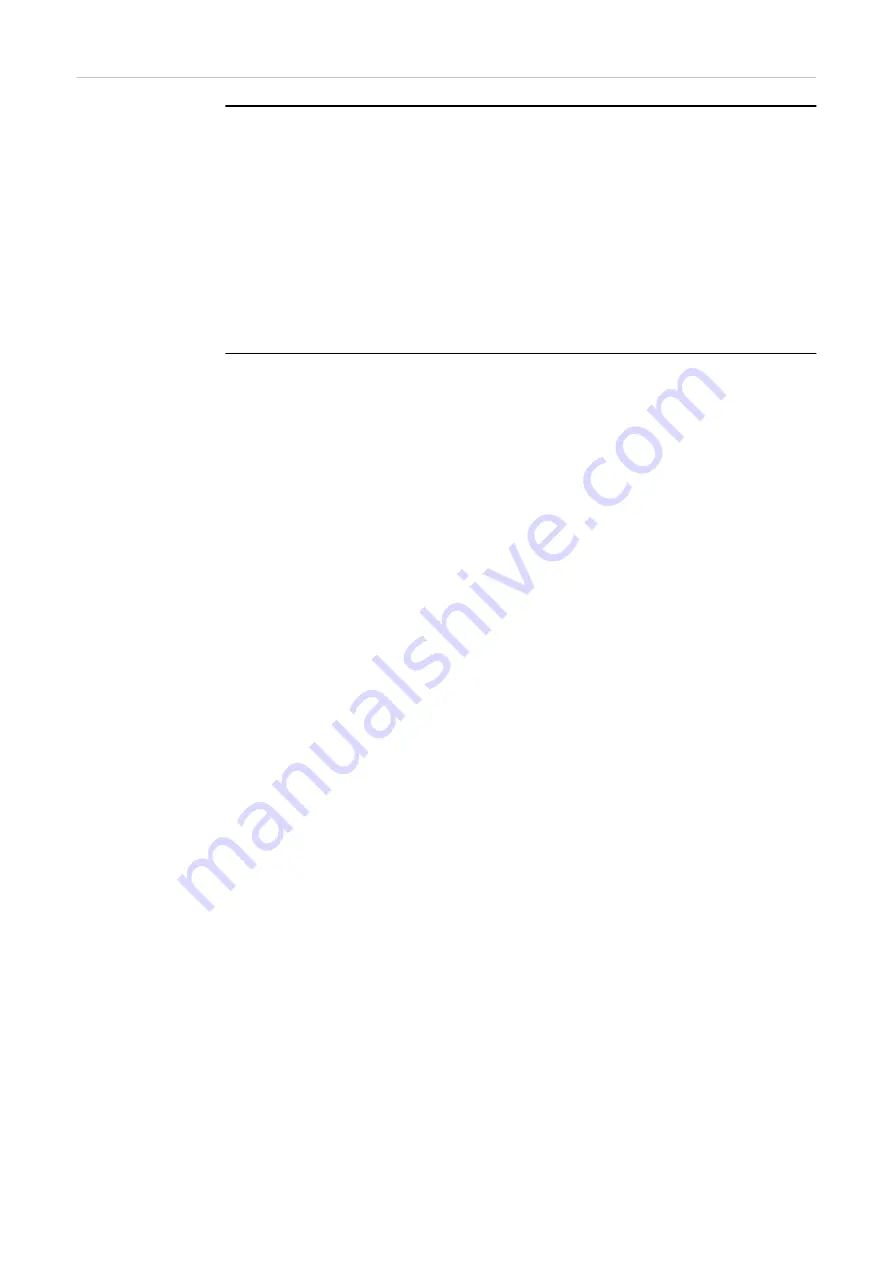
No USB/Speed-
Net connection
No USB/SpeedNet connection between power source and calibration software
USB connection error
Check that the USB Ethernet adapters are properly plugged into the
power source and calibration system.
Check the Ethernet connection cable for any possible damage and
for functionality.
Check that the Ethernet connection cable is connected correctly to
the USB Ethernet adapters.
Check that the DHCP server is running (icon in the task bar!). If the
DHCP server is not running, restart the software and check the net-
work settings.
Disconnect the USB briefly from the power source and reconnect it
again.
Cause:
Remedy:
94
Summary of Contents for Calibration system 2.0
Page 2: ......
Page 13: ...General information 13...
Page 14: ...14...
Page 22: ...22...
Page 23: ...Controls connections and mechan ical components 23...
Page 24: ...24...
Page 28: ...28...
Page 29: ...Installation 29...
Page 30: ...30...
Page 38: ...38...
Page 39: ...Calibrating welding systems 39...
Page 40: ...40...
Page 47: ...2 2 Connect the Signotec signature pad to the calibration system 47 EN...
Page 90: ...90...
Page 91: ...Troubleshooting 91...
Page 92: ...92...
Page 95: ...Technical data 95...
Page 96: ...96...
Page 99: ...99 EN...