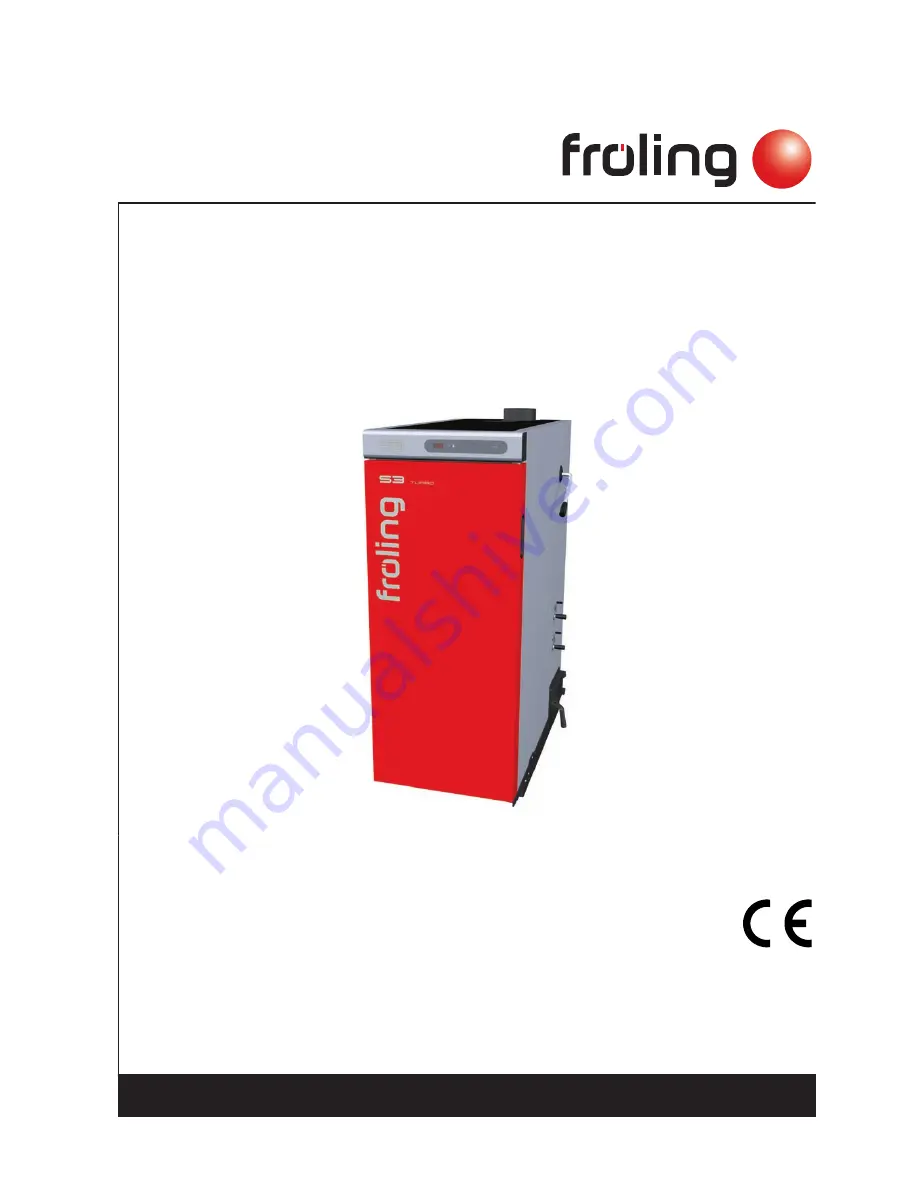
Installation Instructions
Firewood boiler S3 Turbo
Translation of the original German installation instructions for technicians
Read and follow the instructions and safety information!
Technical changes, typographical errors and omissions reserved!
M1081217_en | Edition 23/03/2017
Froeling GesmbH | A-4710 Grieskirchen, Industriestraße 12 | www.froeling.at
All manuals and user guides at all-guides.com
all-guides.com