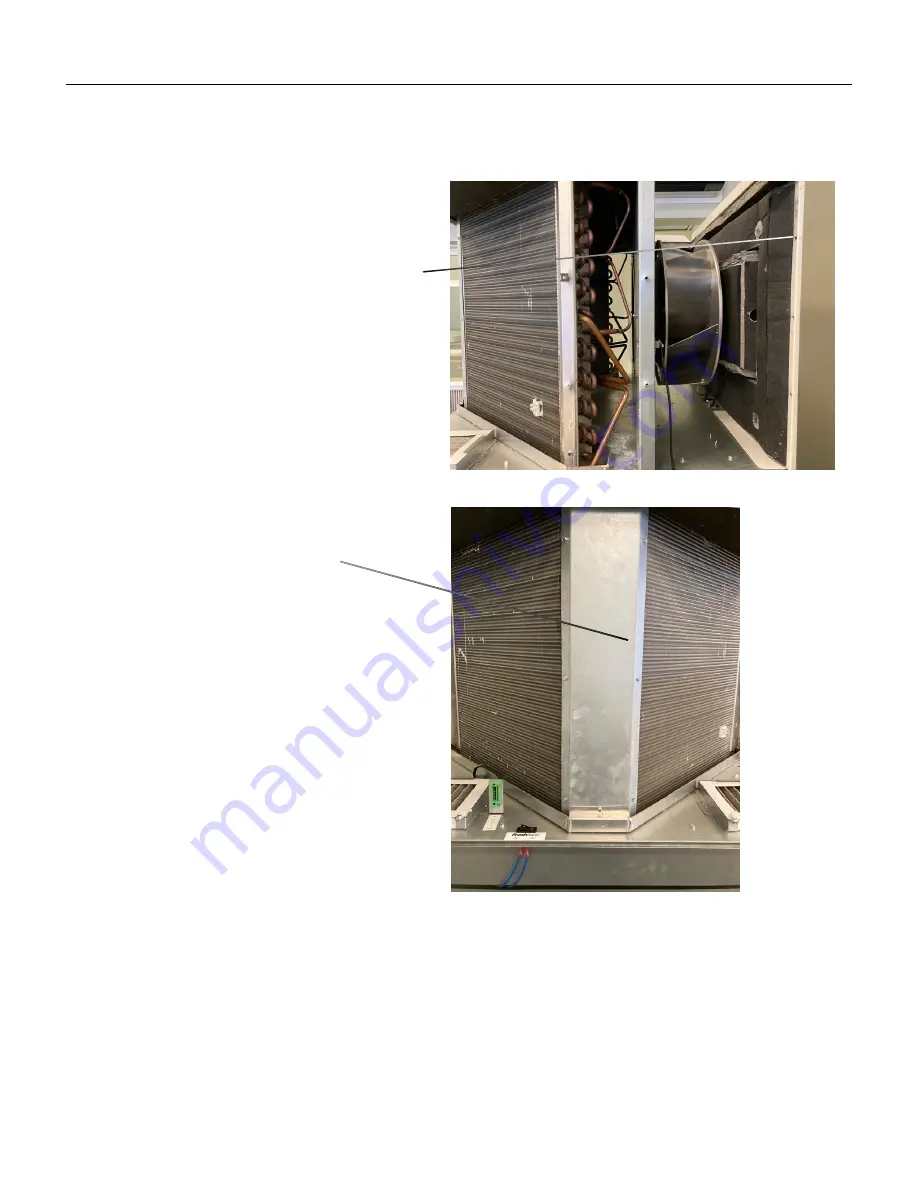
116
PB
R-410A SEALED SYSTEM REPAIR
Replace The Evaporator Coil 36k
1. Remove unit from closet.
2. Ensure no charge in the system,
evacuating according to
EPA standards.
3. Remove front, side, and top panels
Caution: Rear blower panel will need to be supported or
removed if top panel is removed. Damage to equipment
could otherwise occur.
NOTE: The 36k units utilize 2 evaporator coils and 2 reheat
coils if applicable. Either or both coils may be replaced as
required.
6. Detach 2 thermistors from coil.
7. If Unit has a reheat coil;
Reheat coil can be removed from evaporator coil
by removing 4 screws.
Caution: (reheat coil will need to be supported to
prevent damage to tubing.
Alternatively, the tube to reheat coil can either
be sweateded off and rebrazed or cut and
swedged.
8. Remove screws on front header plate.
9. Sweat out evaporator coil tubing connections.
10. remove remaining screw attaching coil to the drain
pan.
11. Lift coil up and out and replace evaporator coil in
reverse sequence. Reinstall reheat coil if applicable.
12. Pressurize with a combination of R-410A and nitrogen
and leak test all connections . If a leak cannot be found,
pressurize with a combination of Nitrogen and a trace
charge of R-410A and sweep with with an electronic or
Halide leak detector. Recover refrigerant and repair any
leaks found.
13. If leak detector is unavailable remove all refrigerant
from system and pressurize with nitrogen to 550 psi.
Check that system holds pressure.
Repeat Step 11 to insure no more leaks are present
14. Evacuate the system with a good vacuum pump
capable of a final vacuum of 200 microns or less. The
system should be evacuated through both liquid line and
suction line gauge ports. While the unit is being evacuated,
seal all openings on the defective compressor. Compressor manufacturers will void warranties on units received not properly
sealed. Do not distort the manufacturers tube connections.
15. Recharge the system with the correct amount of refrigerant. The proper refrigerant charge will be found on the unit rating
plate. The use of an accurate measuring device, such as a charging cylinder, electronic scales or similar device is necessary.
Figure 506 (Support blower panel)
Figure 507 (Remove Header Panel)
Summary of Contents for VRP12K
Page 46: ...46 OPERATION Component Identification Indoor Coil 36k ...
Page 48: ...48 OPERATION Component Identification Outdoor Coil Monitored by 1 thermistor ...
Page 49: ...49 OPERATION Component Identification Outdoor Fan BLDC Variable Speed 600 1000 RPM ...
Page 53: ...53 OPERATION Component Identification 4 Way Reversing Valve 208 230v Reversing valve assembly ...
Page 177: ...177 UPDATING VRP FIRMWARE Or ...
Page 184: ...184 UPDATING VRP FIRMWARE Open zip file Copy to SD Card Insert into SD Card Slot ...
Page 193: ...193 UPDATING VRP FIRMWARE Retrieving VRP Data Remove SD Card from FMC and Locate DF Folder ...
Page 196: ...196 WIRINGDIAGRAMS 12 24K BTU 208 230V 7 5 10 0 KW Figure 801 Wiring Diagram ...
Page 197: ...197 WIRING DIAGRAMS 12 24K BTU 208 230V 2 5 3 4 5 0 KW Figure 802 Wiring Diagram ...
Page 198: ...198 WIRING DIAGRAMS 12 24K BTU 265V 2 5 3 4 5 0 kW Figure 803 Wiring Diagram ...
Page 199: ...199 WIRING DIAGRAMS 12 24K BTU 265V 7 5 10 kW Figure 804 Wiring Diagram ...
Page 200: ...200 WIRING DIAGRAMS 36K BTU 208 230V Figure 805 Wiring Diagram ...