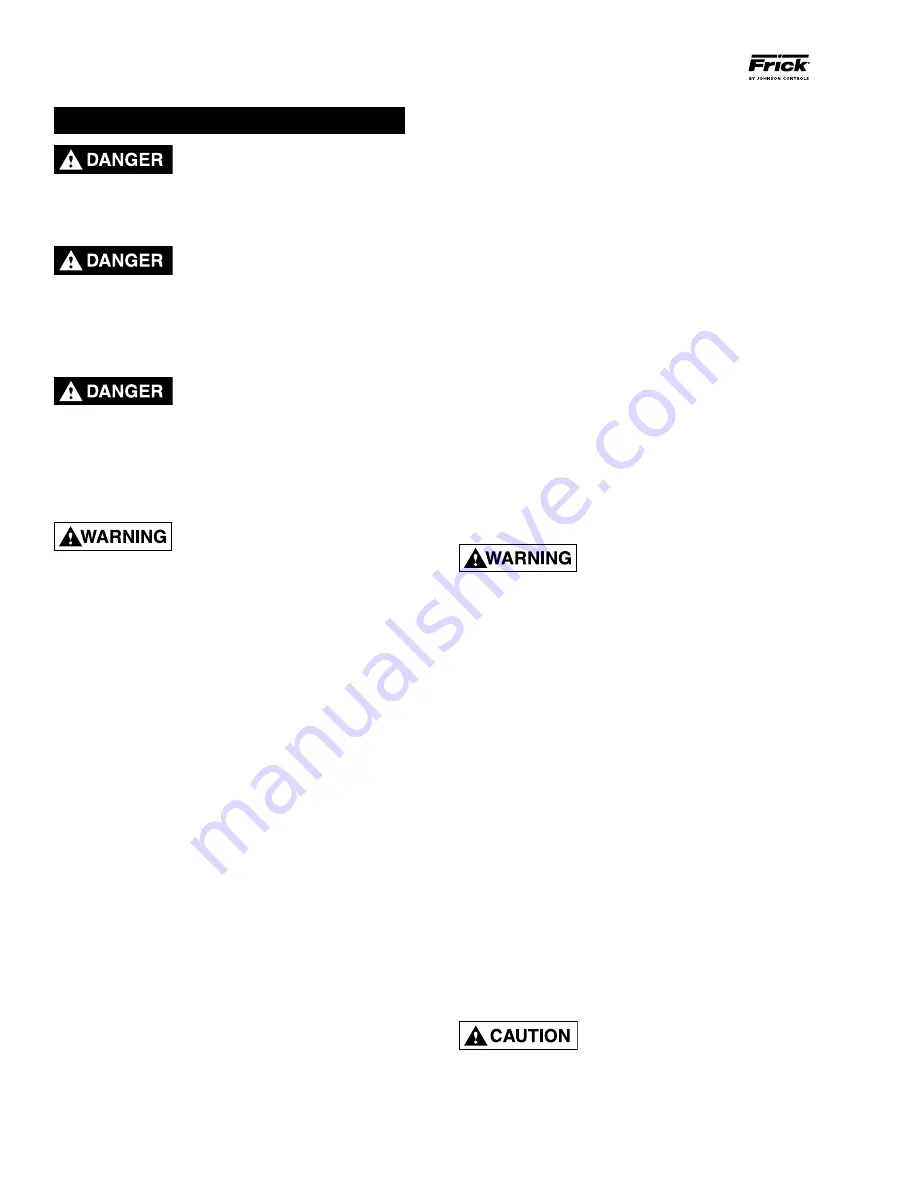
VYPER
™
VARIABLE SPEED DRIVE
OPERATION
100-210 IOM (
JUL
09)
Page 56
MAINTENANCE
Shock Hazard! Before beginning
service, use proper lock-out/tag-out
procedures to disconnect all power
supplies related to this equipment. Verify all power is
removed from the supply leads. Death or severe personal
injury will occur if proper care is not taken.
This equipment is for power
conversion purposes. It is energized
with up to 600 volts AC and houses
a DC bus that is charged up to 1.4 times the incoming
voltage. It also encompasses multiple contactors that
may open and close without notice. It is not intended to
be operated with the doors open and appropriate ARC
FLASH protection must be used when servicing.
Shock Hazard! Wait five (5) minutes
after switching power to the Vyper
™
OFF to allow capacitors in the
cabinet to discharge before opening the cabinet door.
Failure to do so will result in death or serious injury.
After opening the door, carefully verify that the incoming
power has been removed and that the DC bus is
completely discharged with a Cat. IV meter capable of
reading up to 1000 volts AC & DC.
All service on this equipment should
be performed by Johnson Controls
certified service personnel only.
Death, severe personal injury, and/or equipment damage
may occur if service is not performed by competent
personnel.
NORMAL MAINTENANCE OPERATIONS
Before performing any routine maintenance or service on
this equipment, read this section thoroughly first. This section
provides instructions for normal maintenance, replacement
of the power module, and replacement of the harmonic filter
module.
An authorized Johnson Controls-Frick service representative
should perform all service and maintenance activities other
than the standard maintenance activities listed below.
STANDARD MAINTENANCE
The Vyper
™
requires very little facility-operator-supplied
maintenance. The only routine maintenance item involves
the coolant system.
The Vyper
™
is shipped to the customer with a premixed so-
lution of 50/50 mixture of Propylene Glycol and a corrosion
inhibitor. This shipping fluid needs to be replaced before
starting the unit. Proper disposal of the Propylene Glycol
is required.
The standard Frick running coolant is pink in color and con-
tains a nitrite corrosion inhibitor to reduce corrosion effects
on the aluminum surfaces of the cooling circuit. The pink color
may become clear over time, but cooling performance is not
affected. Do not dilute the premixed coolant.
Inspect the coolant and coolant level regularly and replace the
coolant annually using the steps described previously in this
manual. Any time the coolant is removed from system, always
discard the old coolant and replace with new coolant.
Coolant that is any other color than pink (or clear) indicates
bacterial growth or corrosion. Symptoms are as follows:
•
Brown or green in color indicates that
bacteria growth
is occurring.
•
Milky white coolant or the presence of a white milky
coating inside of the tubing indicates corrosion exists
on the inside of the cooling system and is oxidizing
the aluminum components.
If any of these conditions occur, use proper health and dis-
posal precautions when draining the coolant. Referring to
the coolant changing procedure described previously in this
manual, use the following steps to replace the coolant in the
contaminated system:
1. Drain the coolant and blow the system out with com-
pressed air.
2. Flush the coolant system out thoroughly with water.
3. Fill the coolant loop with
Ethylene Glycol
(Not Propyl-
ene Glycol, normal Frick running coolant).
4. Circulate the Ethylene Glycol for one hour.
5. Drain the Ethylene Glycol and refill the coolant loop with
Frick running coolant.
6. Check the coolant system in two weeks for bacteria
growth and/or corrosion.
REPLACEMENT OF THE
VYPER
™
POWER MODULE
The Vyper
™
Power Module is to be
replaced by Johnson Controls
certified service personnel only.
Death, severe personal injury, and/or equipment damage
may occur if service is not performed by competent
personnel.
The following is a step-by-step procedure describing the
replacement of the Vyper
™
power module. Follow this pro-
cedure minimize the possibility of damage to other system
components or to the Vyper
™
drive.
Save all the packing material. This material must be reused
when returning a defective power module for warranty
claims.
Power module replacement procedure:
1. Be certain the Vyper
™
has been de-energized for over
five minutes, and then double-check for presence of
voltage using a VOM. The DC bus must be fully dis-
charged.
2. Drain the coolant from the heat exchanger into a suitable
container and discard. Use proper handling and disposal
procedures, as the coolant may contain bacteria.
3. Remove the connector to the IGBT Gate driver board.
4. Remove and discard the six (6) Phillips head screws
from the power wire connector tangs and the remaining
(6) Phillips head screws from the bus connections.
5. Remove and discard the eight (8) Allen screws from the
IGBT module.
Use care when removing the Vyper
™
power module. Do not place any
stress on the bus structure and
make sure coolant does not drip from the IGBT module
to other components. Damage will occur to the
components if this precaution is not followed.