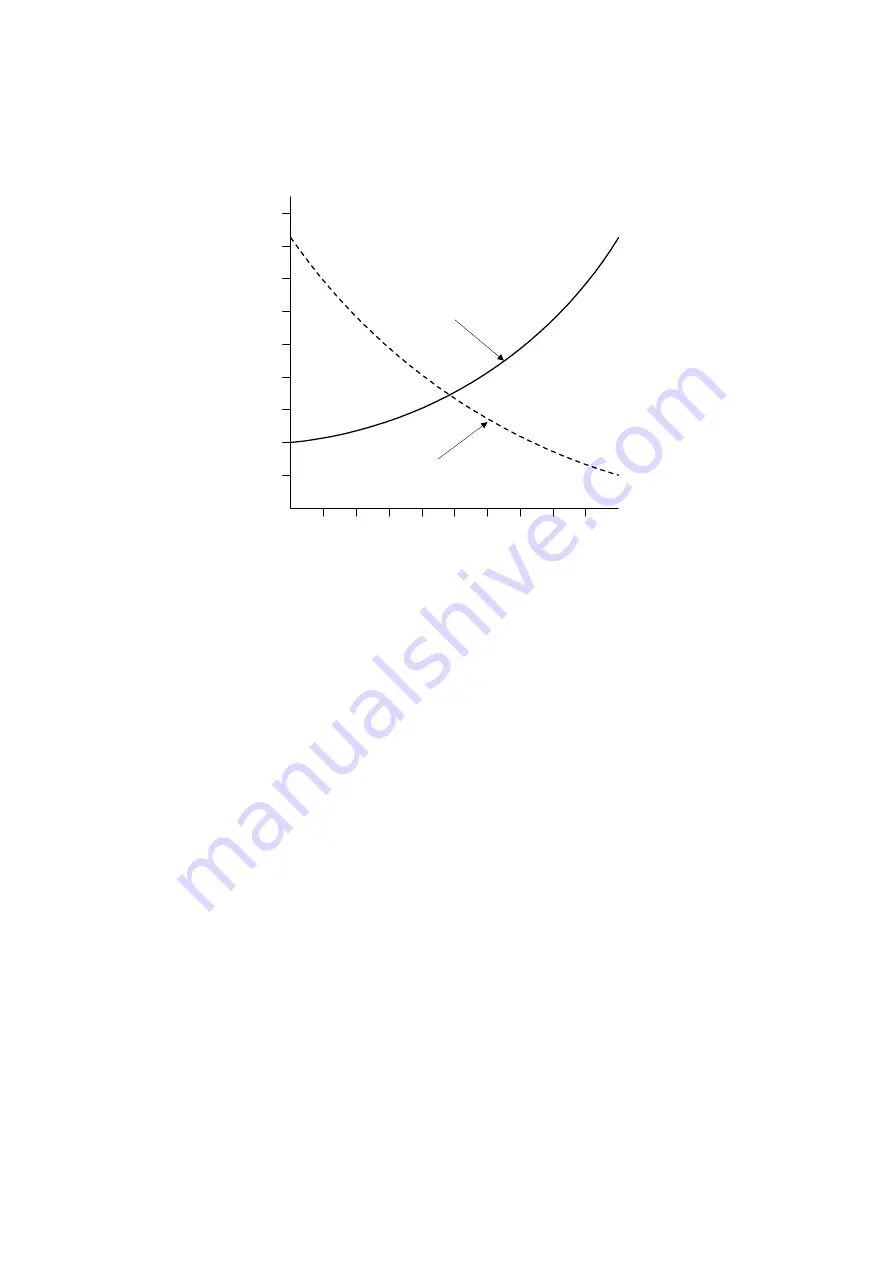
PROCESS CONTROL
31 March, 1999
2-2
2.1.2 ID SENSOR
The ID sensor consists of two separate sensors. For detecting the density of black
toner patterns, there is a straight reflection sensor for K toner (this is the type of
sensor normally used in black-and-white copiers), and for colored toner there is a
diffused light sensor. Both sensors share the same LED, but have separate light
receivers for K and color toners. However, the LED current (light intensity) used for
detecting black toner is different from the one used to detect colored toner.
As shown in the diagram, the output from the straight reflection sensor decreases
as the amount of attached toner (M/A: mass/area) increases. This is because black
toner is blocking the reflection of light back into the sensor from the transfer belt
(the transfer belt itself is black, but it is reflective). However, the diffused light
sensor output increases for higher M/A, because colored toner is reflective.
The diffused light sensor is more accurate for detecting colored toner, no matter
how much or how little toner is present. However, if the amount of toner on the
transfer belt is small, the low level of reflected light means that without an initial
calibration, the error in detection could be very great.
The diffused light sensor cannot be used for black toner, because there is little
difference between the diffuse light reflected from black toner and from the transfer
belt surface.
ID sensor output [V]
Diffused light
detection curve
Straight reflection
detection curve
Amount of attached toner (M/A, mg/cm
2
)
G024D520.WMF