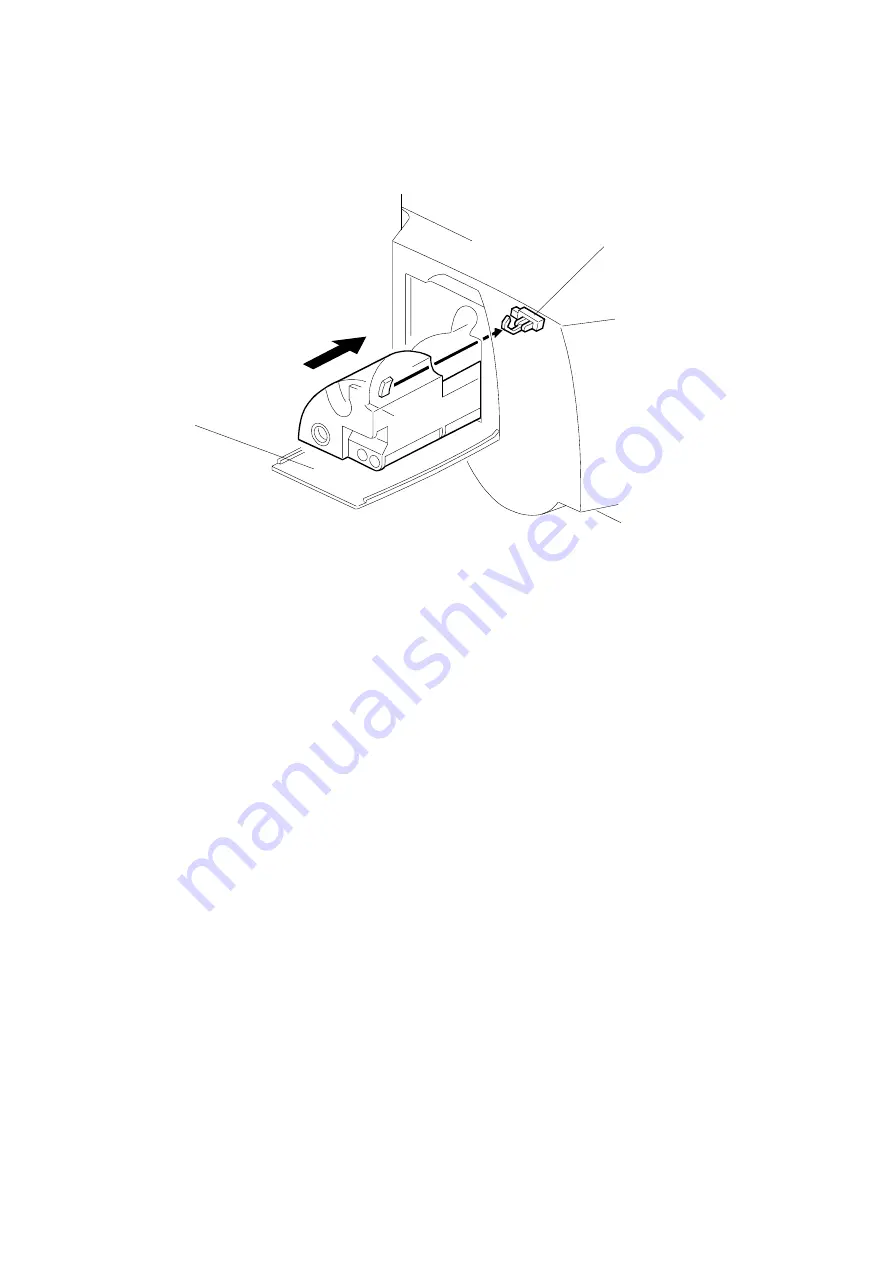
DEVELOPMENT UNIT
31 March, 1999
2-36
2.4.8 DTM (DEVELOPMENT TONER MAGAZINE) DETECTION
The DTM sensor [A] detects the presence of a DTM.
The DTM sensor outputs an error detection signal when a toner bottle is not
present or is incorrectly installed. Printing cannot start until this signal ceases (i.e.,
the error must be corrected).
Installing a toner bottle and closing the DTM cover [B] automatically initiates the
recovery procedure, releasing the error.
G024D164.WMF
[A]
[B]