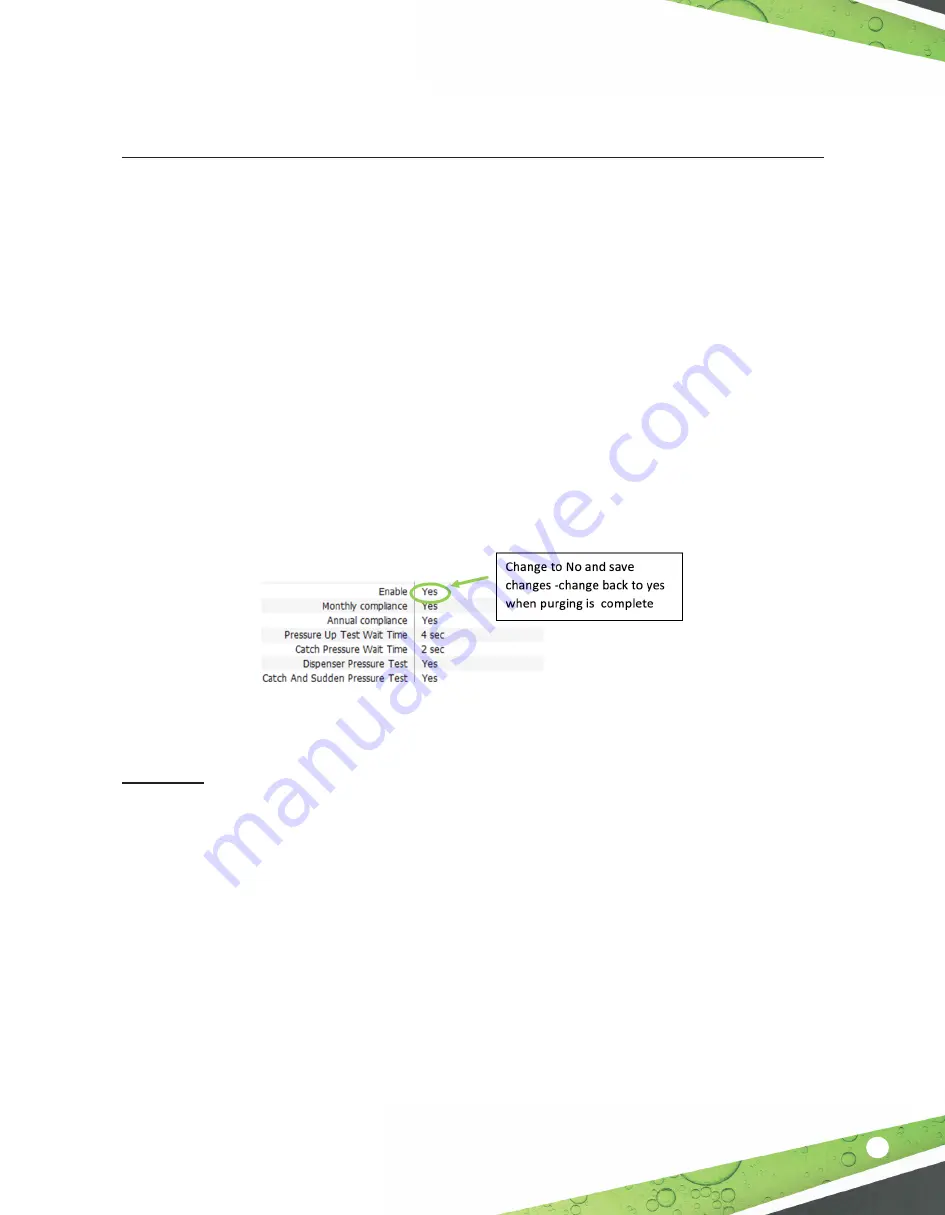
19
Purging the line
• If air is in the system, the lines must be purged of the air. If needed, this procedure should
be done before the Line Stability Test.
• Purge the line by dispensing from each fueling point starting with the dispenser furthest
from the tank. The STP should be running the full time that the line is purged.
• Purging of lines is required prior to performing the AUTO-LEARN
®
process. Submersibles
should operate prior to programming or prior to learning of lines.
• FE PETRO
®
Smart controllers can be put in bypass mode for the purpose of purging lines by
setting Pole 7 – Switch Bank 1 to ON. (The best practice is to power off the controller prior
to changing dip switch settings). This will allow submersible to run in Bypass mode for 10
minutes. If longer time is required simply reset controller (push reset button) for another
10 minutes of bypass mode.
• When needing to purging lines after the console is programmed for line leak detection and
prior to the AUTO-LEARN
®
process. Purging must be completed with the line testing disabled
in the line programming section of Set-up parameters. This will allow pumps to run without
interruption from line leak software during purging. Once purging is complete re-enable
testing under set-up parameters.
NOTE
: If purging is required after the lines have been learned, the same process is required to disable
testing in setup parameters to allow a pump to run for purging purposes.
Zero Offset
• TS-LS500 AUTO-LEARN
®
ELLD requires that the line reach 0 PSI prior to starting the learn
process.
• Failure to follow this step can lead to improper pressure readings, an inability to fail a test
properly and overall improper operation of the ELLD application.
• IF the line cannot reach 0 PSI when opening the needle valve and bleeding off the line
pressure additional purging of line is required to remove air that is preventing the line to
fully bleed off to 0 PSI.
Summary of Contents for TS-LS500
Page 1: ...TS LS500AUTO LEARN LINE LEAK DETECTION INSTALLATION GUIDE...
Page 37: ...33 Control Drawing 1...
Page 38: ...34 Control Drawing 2...
Page 39: ...Intentionally Blank...
Page 40: ...000 2145 r11...