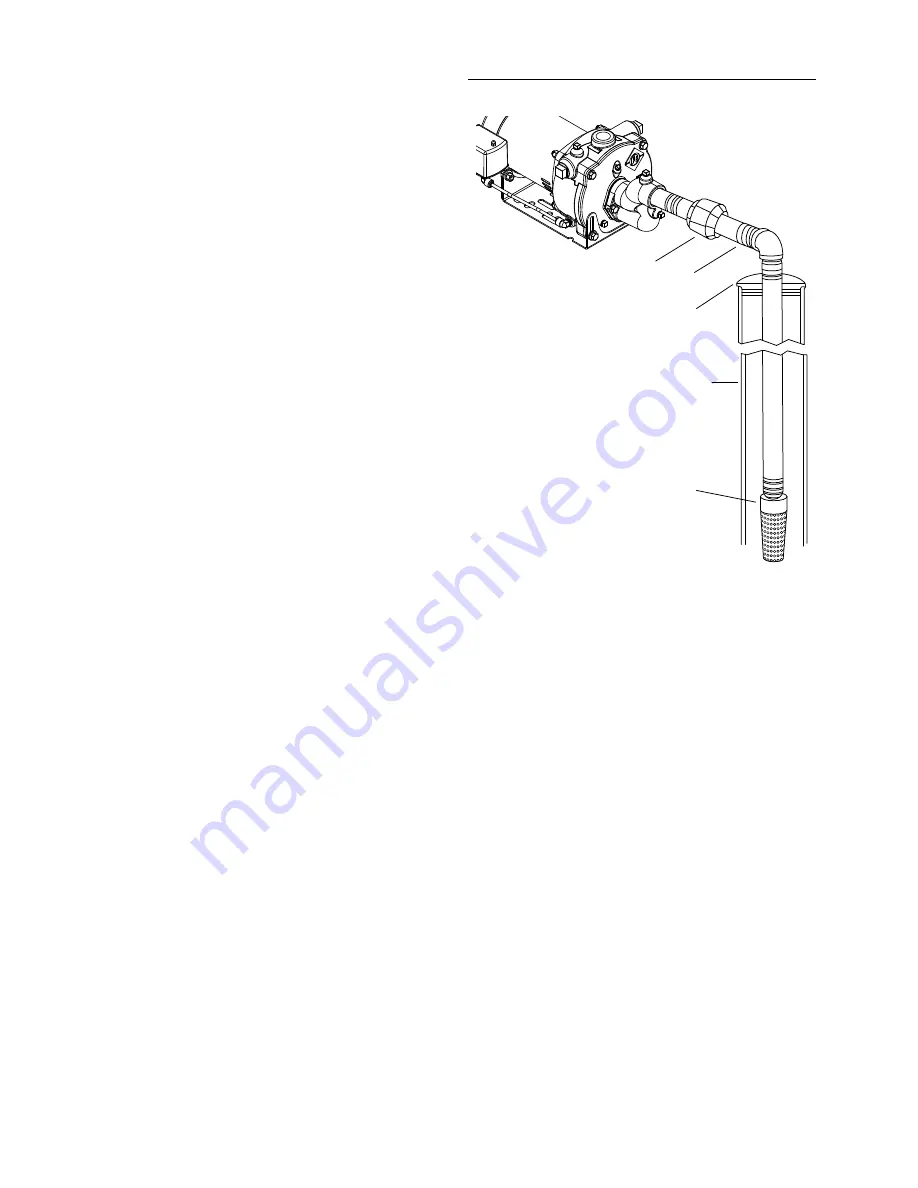
possible, the pump and piping system must be drained
completely of water to prevent possible damage.
Decide how to seal the well from surface contamination
as required by local authorities. The most common device
for this purpose is the Sanitary Well Seal. If the pipes
from the well have to be kept below the frost line, either
bury the wellhead or use a Pitless Adapter that leaves the
wellhead exposed for servicing while providing sealed
openings in the well casing below the frost line.
GENERAL PIPING
Follow all state and local plumbing codes.
Plan your piping layout before starting the installation so
that the correct pipe and fittings are on hand to complete
the job.
Keep the pipes clean, since pebbles and other foreign
material can block the injector or pump impeller.
Make sure that the bottom of your suction pipe is at least
3’ below the lowest dynamic water level in the well, and
not closer than 3’ from the bottom of the well.
If you use poly pipe with barbed adapters we recommend
two hose clamps at every fitting connection to protect
against leaks.
HORIZONTAL OFFSET PIPING (Horizontal piping
between the top of the well and the pump)
A jet pump performs best when installed close to the well
because suction lift and friction losses are kept to a
minimum. Although an installation near the water source
is preferred, it may be necessary or more convenient to
locate the pump away from the well. High spots in the
piping between the top of the well and the pump will
create air pockets and make priming the system very
difficult. To avoid air pockets slope horizontal pipes
continuously upward from water source to pump by at
least 1 vertical inch for every 30” of Horizontal run. When
the pump is offset from the well, the horizontal offset
suction piping may have to be increased in diameter to
reduce pressure loss. The pressure loss in a system
increases:
1.) As the flow rate increases
2.) As the piping size decreases
Consult included friction loss tables (Appendix III) to
determine the amount of head loss for a given
application.
DISCHARGE PIPING
When the pump is located a long distance from points of
water use, it may be necessary to increase the discharge
pipe size in order to reduce pressure loss. The pressure
loss in a system increases:
1.) As the flow rate increases
2.) As the piping size decreases
Consult included friction loss tables (Appendix III) to
determine the amount of head loss for a given application.
SHALLOW WELL INSTALLATION (FIGURE 1 & 2)
SHALLOW WELL SUCTION PIPING (FIGURE 1)
Suction tapping on the pump is 1-1/4” (FNPT) in size.
Suction pipe diameter should never be smaller than the
suction tapping. Use of smaller pipe reduces flow and
pressure in the system. We recommend increasing the
suction line size as the length of horizontal offset piping
increases (see “HORIZONTAL OFFSET PIPING” above).
Shallow well operation, suitable for depths not exceeding
25 feet, requires only a single pipe to the water source.
Typical water sources are wells, lakes, ponds, streams,
or rivers. Support the suction pipe, so its weight is not
carried by the pump. Installation should include a foot
valve in the well (preferred) or a check valve as close to
the water level as possible. A check valve is necessary
for pumping from a drive point well where the suction line
is driven into the ground to extract the surrounding
groundwater. A foot valve is more suitable for a cased/
dug well. Either can be used for pumping from a lake or
stream, provided the end of the suction pipe is also
protected by a strainer. Special care should be taken to
ensure that all suction fittings are tight and sealed.
Otherwise, the pump cannot be primed or will lose prime
over a period of time.
1-1/4
”
Suction Pipe
Sanitary
Well Seal
Well
1-1/4
”
Foot Valve
Union