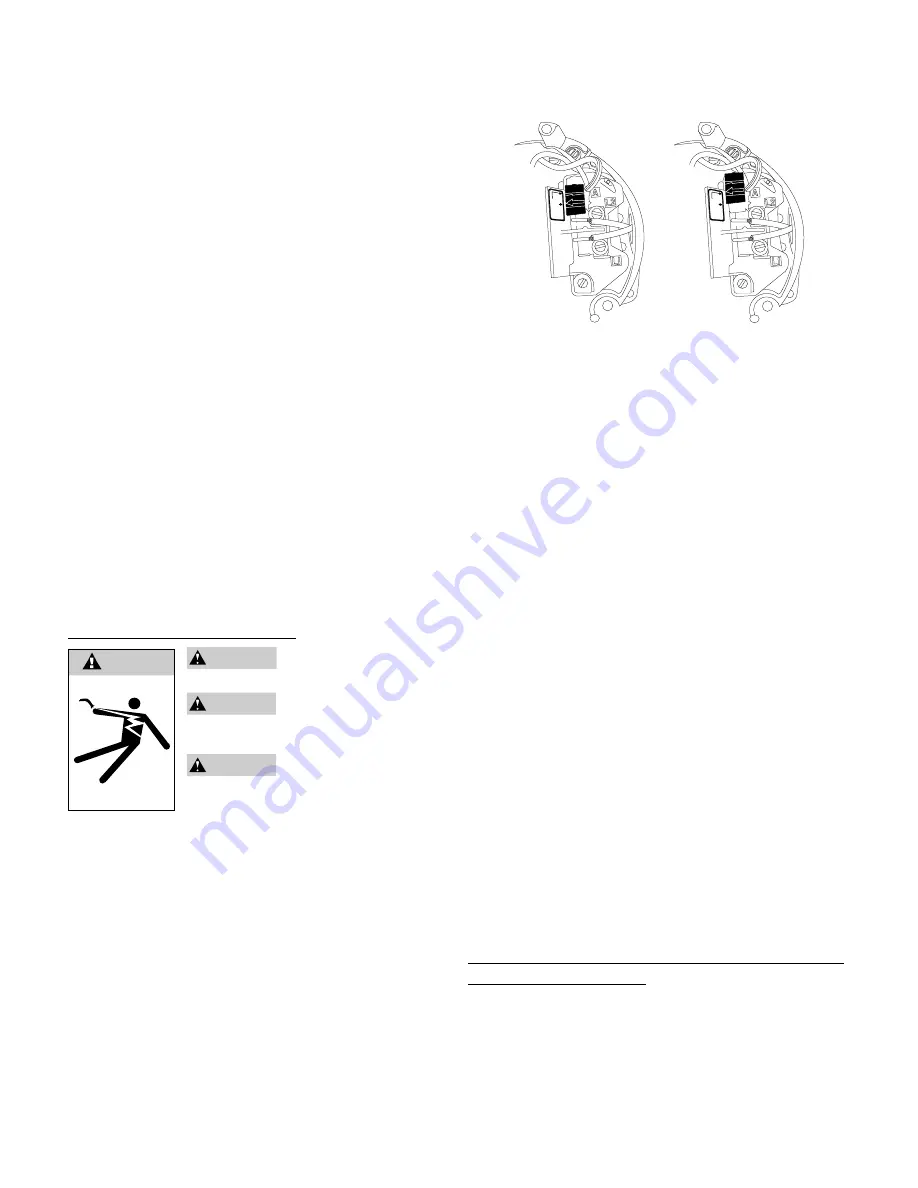
230V
115V
230V
115V
115V
230V
FIGURE 6
energize the pump, and you will have to re-prime the
system. Once the pump is turned on it may take several
minutes to remove all of the air from the system. On
installations with long suction piping, you may have to
add water several times to complete the priming process.
DEEP WELL PUMPS
Priming the pump means filling the pump, suction piping,
and drive water piping with water. Priming is completed
when you start the pump, and all the air is removed from
the piping system, but before you energize the pump you
must manually fill the pump and piping with water. Deep
well installations require a complete prime before starting
the pump. If you used one of the side discharge
connections on the pump, you can easily fill the pump
and piping with water through the 1” top port. If you
installed the control valve in the top discharge port, you
can prime the pump through the 1” priming hole in the top
of the valve. You will need to provide a priming tee if you
used the top discharge port but did not install the control
valve there. Fill the pump with water until full. All
horizontal offset piping should slope up from the well to
the pump to ensue that it is filled with water. Plug the
priming hole. Perform the “ADJUSTING THE CONTROL
VALVE” procedure listed below. Once the pump is
turned on it may take several minutes to remove all of the
air from the system. On installations with long suction
and drive water piping, you may have to add water
several times to complete the priming process.
ELECTRICAL INSTALLATION
WARNING
Hazardous voltage can
shock, burn or cause death.
CAUTION
If you are not sure of
proper electrical connections, consult a
licensed electrician.
CAUTION
Improper wiring can
result in permanent damage to the
motor. All electrical wiring should meet
the local electrical code.
NOTICE:
READ AND FOLLOW ALL INSTRUCTIONS!
Pump connection must comply with National Electric
Code (NEC) or Canadian Electric Code (CEC), and all
applicable local codes.
All dual voltage units come factory preset for 230
volts. (Figure 6)
Disconnect power at electrical panel before making any
electrical connections or changes.
Supply voltage must be +/- 10% of motor nameplate
voltage. Low or high voltage can damage the motor and
will void the warranty.
If possible, connect pump to dedicated branch circuit with
no other appliances on it.
Do not operate pump unless pump is grounded.
VOLTAGE CHANGE
NOTE:
To change the motor voltage(Figure 6) unplug the
dual voltage plug on the motor and reconnect it in the
position required to match the supply voltage. The motor
can be set for 115 volts or 230 volts. The voltage setting
of the motor can be determined by looking at the
alignment of the arrow on the plug and the arrow on the
motor terminal board (located under the motor’s end
cover). Any questions as to which voltage setting is
required for proper motor and pump operation in your
system should be directed to an electrical professional.
The factory preset is 230 volts.
NOTICE:
Check motor terminal cover or nameplate for
wiring instructions. The essential pump motor facts are as
follows:
1. 3450 RPM
2. Single Phase
3. Dual Voltage, 115/230
4. 1/2, 3/4, 1, and 1-1/2 Horsepower motors are wired for
230 volts as a factory standard.
NOTE: All wiring is subject to official inspection and must
conform to the local electrical code. Install a circuit
breaker or fused disconnect switch near the pump.
Remove the cover from the pressure switch. Connect the
incoming power wires to the LINE terminals and the
green or bare wire to the ground screw, then ground the
entire unit. Refer to
FIGURE 7 for internal sketch of
pressure switch.
CONTROL VALVE ADJUSTMENT (DEEP WELL
INSTALLATION ONLY)
A control valve is required for all deep well installations.
At system start-up, this valve will need to be adjusted as
described below to assure optimum performance.
1. Install a pressure gauge that reads pressure at the
pump case.
2. Open several faucets downstream from the
control valve.
WARNING