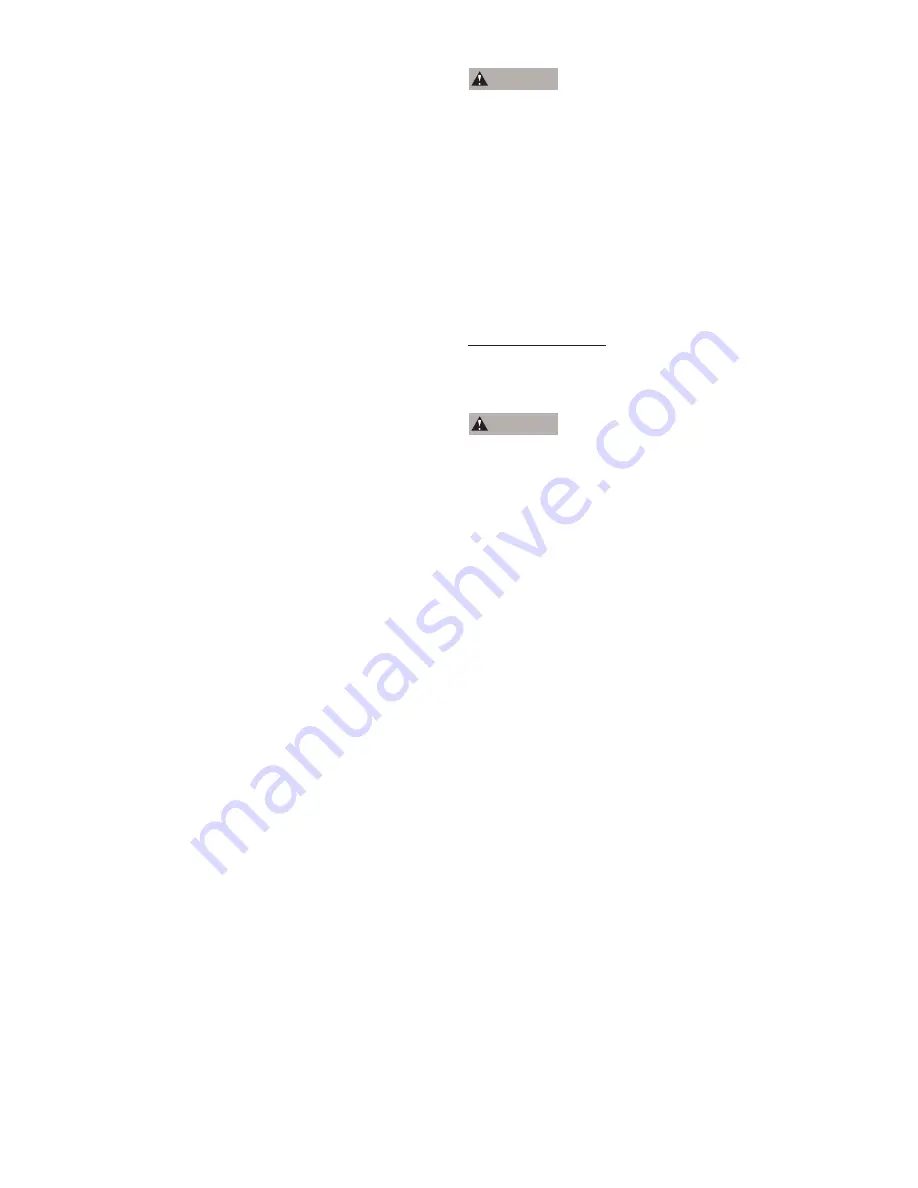
C A U T I O N
C A U T I O N
three-phase motors by turning on power only for an
instant, so that pump turns just a few revolutions
(prolonged operation of pump in the wrong direction may
damage it and void the warranty). Note whether shaft
rotation is in agreement with direction arrow on pump
case. If direction is wrong, obtain opposite rotation by
interchanging any two of three wires, either at the motor
or starter. Close the gate valve in the discharge line and
the start pump. Open the valve gradually to half-open
position after the driver attains operating speed. If the
pump fails to function after a few seconds of operation,
stop it and allow it to remain idle for several minutes. Add
more priming liquid if needed and open the air vent pipe
plug briefl y to permit any accumulated air to escape.
Restart the pump. If it still fails to function, stop it and
repeat priming and air-bleeding procedure.
If repeated attempts at starting the pump are
unsuccessful, check for leaks in the foot valve or suction
piping. Do not permit the pump to run for more than a few
seconds unless it remains full of liquid and is discharging
properly. Prolonged operation of an unprimed pump can
cause severe damage to the rotating parts and void the
warranty. A discharge pressure gauge, mounted at the
pump discharge will indicate the pressure being
developed by the pump and will assist in determining
whether the pump is operating properly. When proper
pump operation is obtained, and if the discharge line
remains full at all times, the discharge gate valve can be
opened fully and allowed to remain open until the pump
must be serviced or reprimed.
For pumping systems which are especially large or which
do not incorporate a foot valve, and yet must be primed
in order to overcome suction lift conditions, other
methods of priming are available. Hand-operated or
motor (or engine) driven vacuum pumps can be used to
evacuate air from the pump case in a reasonable length
of time. The discharge line must have a check or gate
valve located near the pump in order to limit the volume
of air to be moved.
If the pump must be shut down while exposed to below
freezing weather, protect it and connected piping from
damage by draining the system completely, or by
introducing a corrosion-inhibiting antifreeze into the
system.
LUBRICATION - PUMP
The rotating parts of the centrifugal pump (impeller, shaft,
seal elements, etc.) are lubricated by the liquid being
pumped. No additional lubrication is required.
DO NOT START OR RUN PUMP DRY.
Seal adjustments are not required; the seal is lubricated
by the liquid being pumped. Occasionally, a new seal may
leak slightly during its fi rst hour of operation, but unless
the seal is faulty or the installation has been done
incorrectly, this leakage will stop. When leakage occurs
after the pump has been used for a long time, the seal
must be replaced.
Mechanical shaft seals must not run dry.
Fill the pump with water before starting or thepump
will be damaged. The motor on this pump is
guaranteed by the manufacturer and in event of failure
it must be returned to an authorized service station
for repairs. Motor warranty is void if repairs are not
made by an authorized station.
LUBRICATION - MOTORS
The motors are generally equipped with sealed ball
bearings, requiring no additional lubrication. Service and
parts can best be obtained from the motor manufacturer’s
authorized repair shop in your area. Check your telephone
book or contact your nearest dealer for their address.
DISASSEMBLING
PUMPS WITH 56C FRAME MOTORS
To disassemble and reassemble the pump, consult Fig. 1
for identifi cation of components referenced by numbers.
Make sure power to the motor is
disconnected to prevent start-up or electrical shock.
Remove capscrews
(11)
which fasten the motor bracket to
the casing. Back out motor and bracket assembly from the
casing. The gasket
(10)
may be reusable if not mutilated;
however, it is a recommended practice to install a new
gasket each time the pump is reassembled. With the
above assembly removed from the casing, the impeller
(2)
can be removed from the stub shaft
(5)
by holding the stub
shaft
(5)
across its fl ats (through the window of the
bracket) with an open-end wrench and unscrewing the
impeller. While holding the stub shaft
(5)
, insert a
screwdriver between the vanes of the impeller
(2)
, gently
loosen the impeller in a counter-clockwise direction. Use
moderate torque so as not to damage the impeller vanes.
When reassembling the pump, tighten the impeller with
slightly extra pressure, and be sure to check rotation
under start-up.
The rotating assembly of the mechanical seal
(4)
can be
pulled off the stub shaft. If the rubber driving ring of the
seal is fi rmly gripping the stub shaft
(5)
remove the
bracket capscrews
(12)
and use the bracket
(3)
as a puller
to remove the seal assembly
(4)
. Press the cup seat
holding the ceramic seat of the seal out of the bracket.
Lubricate the outside diameter of the new rubber cup seat
with light oil; press the cup seat with seat face into the
bracket cavity, making certain that it is seated squarely in
the cavity. If the seat and ring cannot be pressed into
place with the fi ngers, cover the lapped seat face with the
cardboard ring which is packed with each new seal
assembly, and tap seat and ring into place by using a light
mallet with a piece of wood placed squarely against the
seat face.
Inspect pump shaft to see that it is clean and smooth. Use
emery cloth to polish the shaft if it is scored, or replace the
stub shaft
(5)
if there is excessive wear. The stub shaft
(5)
is locked in place on motor or frame shaft with set screws
(15)
. If the stub shaft has been disconnected from the