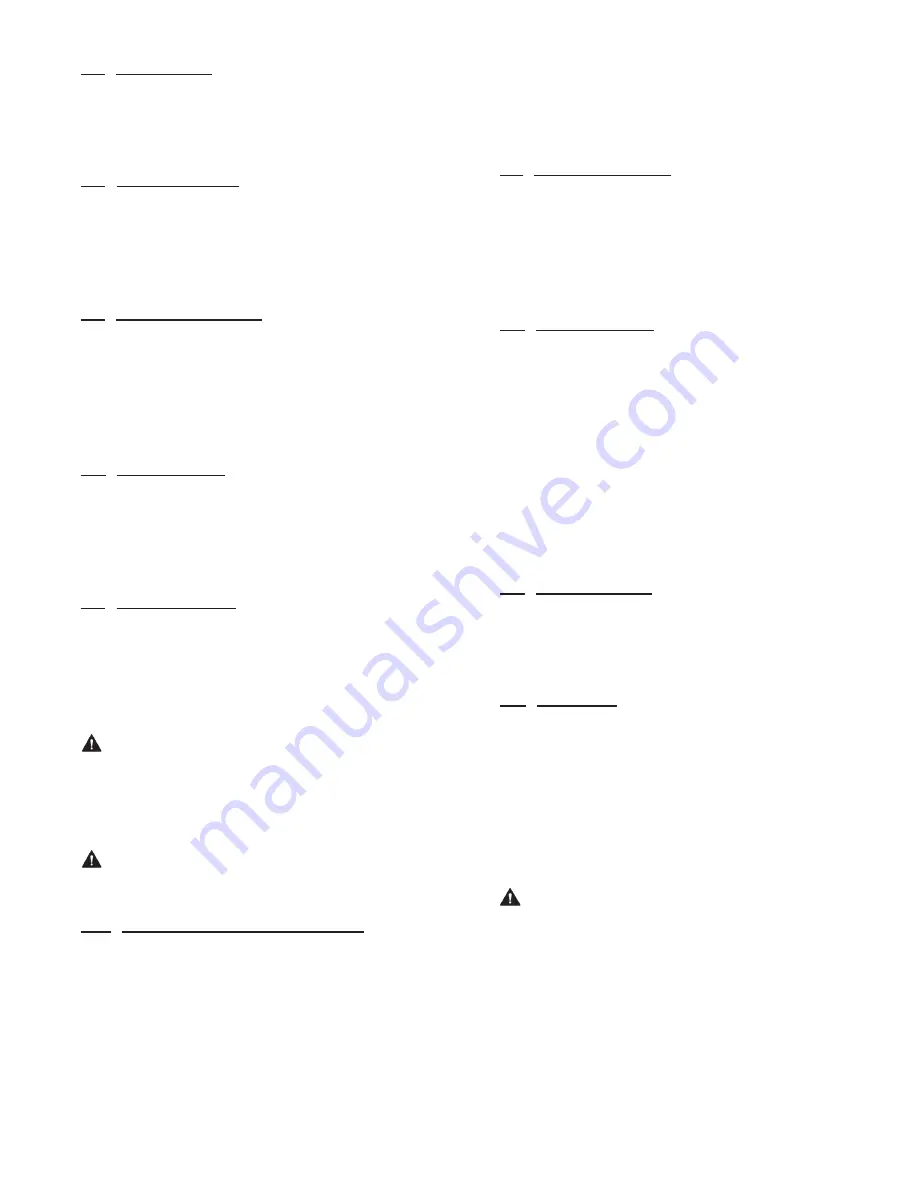
15
11.5 Turn On Power
With the control panel grinder pump disconnect/breaker in the “off”
position, turn on the property service panel breakers supplying power
to the pump and system monitor.
11.6 Fill Collection Tank
Fill the collection tank with water until the “high-level” alarm sounds
and the light illuminates in the control panel. This should occur within
6" of the inlet pipe invert. The “high-level” alarm should also be visible
and audible. Press the “stop” button to silence the audible alarm.
11.7 Turn Grinder Pump On
Move the grinder pump power disconnect/breaker to the “on”
position. The grinder pump should turn on immediately. Within two
minutes the high-level alarm LED will turn off and automatically reset.
Within five minutes the grinder pump should turn off, with the liquid
level approximately 1' from the bottom of the collection tank.
11.8 Troubleshooting
If the PowerSewer® system does not respond as described, review the
installation instructions to ensure that they were followed completely.
If the system still does not respond properly, refer to specific pump
owner's manual.
11.9 Secure the System
Close the Junction Box cover, align cover tabs and uniformly tighten
all four fasteners. Replace wet well access cover. Make sure the wet
well cover seats completely for a watertight seal. The cover fits very
tightly. Step on the cover to ensure it is seated properly. Replace the
tank cover and uniformly tighten all six bolts to 100 in-lbs.
CAUTION
The PowerSewer® cover must be properly
secured to the collection tank at all times If bolts or sealing
washers are lost or damaged, contact your Franklin Electric Sales
Representative or Franklin Electric Customer Service immediately
at 866-271-2859
CAUTION
Failure to create watertight seals at the cord
grips or enclosure lid may result in premature system failure
11.10 Review System with Property Owner
Review the PowerSewer® system and monitor features with the
property owner.
12. OPERATION
The PowerSewer® grinder pump sewer system is equipped with a float
control system that continuously controls the grinder pump operation.
12.1 Automatic Operation
Sewage enters the collection tank through the drop inlet pipe. When the
level reaches a preset “on” point, the “on” float switch sends a signal to
the pump start relay energizing the pump motor. The pump motor will
remain energized until the sewage level reaches the preset “off” point
and activates the “off” float switch and de-energizes the pump motor.
12.2 Manual Operation
The PowerSewer® residential and commercial grinder pump system
is equipped with a manual override button, labeled “Hand,” which
allows for temporary manual operation of the pump. Press and hold
the manual override button to operate the pump. As soon as the
button is released, the system is immediately returned to automatic
operation. The manual override option is helpful when diagnosing a
problem because it will isolate the pump from the control system.
It also can be used to clean the collection tank by operating the pump
past the “off” position to remove scum or grease that has collected on
the surface of the sewage.
12.3 High-Level Alarm
The High-Level Alarm will energize when the sewage level rises to a
level that activates the high-level float switch. The PowerSewer® does
have reserve capacity, but should only be used for emergency purposes.
12.4 System Care
Properly installed, operated and maintained, the PowerSewer®
grinder pump system will provide many years of reliable service. The
service life of your PowerSewer® grinder pump could be shortened if
the following items are put down a drain or toilet:
Bones, Cloth, Condoms, Dental Floss, Diapers, Glass, Metal,
Nylons, Plastic, Sanitary Napkins, Seafood Shells, Tampons,
Wood, Cigarette Filters.
CAUTION
Resulting premature wear is not covered by warranty
The following hazardous items should never be introduced into any
sewer system because of the potential for blockage, contamination,
corrosion, explosion or fire:
Corrosive Chemicals, Explosives, Flammable Liquids or
Materials, Gasoline, Grease, Oil, Paint, Paint Cleaners,
Volatile Organic Chemicals
Summary of Contents for PowerSewer V4PS
Page 1: ...V4PS Installation Operation Maintenance Manual...
Page 31: ...31 NOTES...