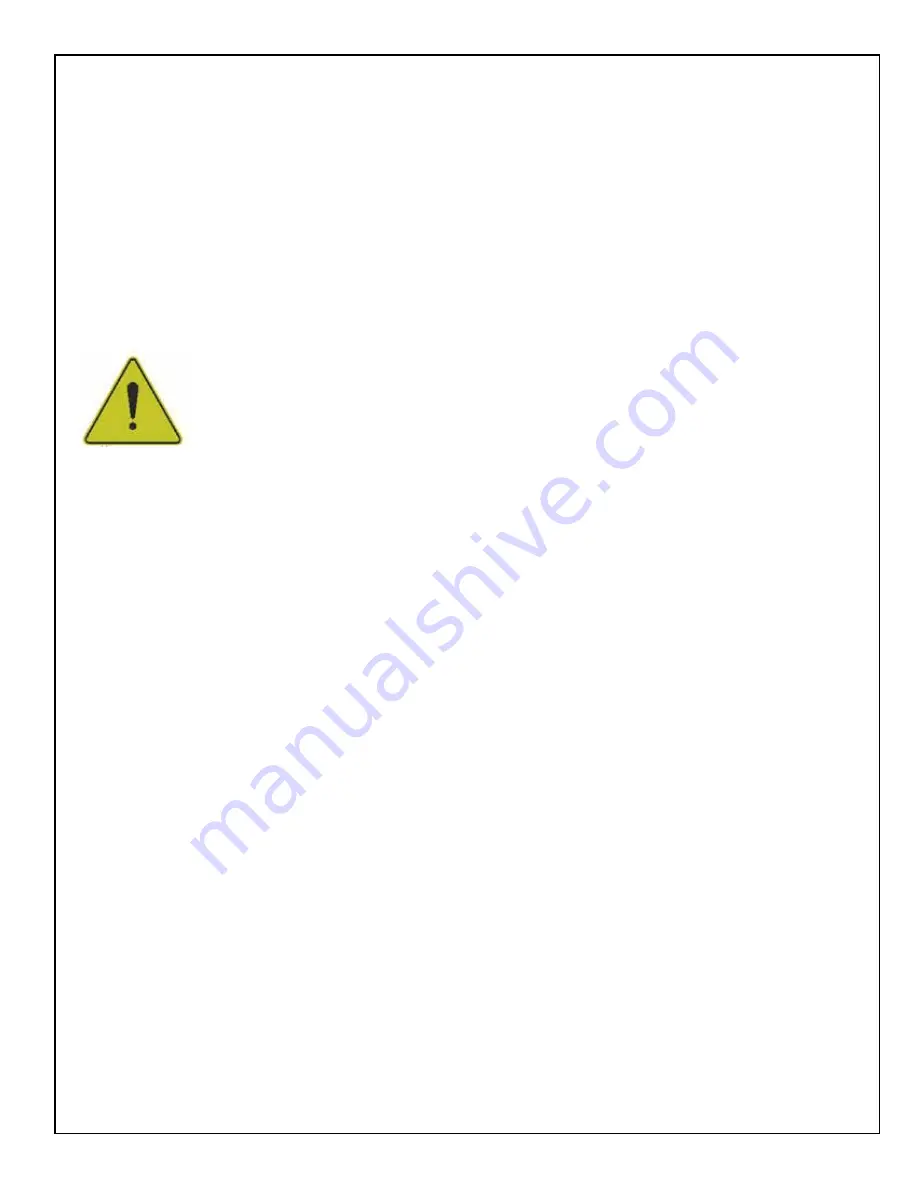
21
- ORIGINAL INSTRUCTIONS -
OPERATION
ELECTRIC WINCH (OPTIONAL)
This unit is activated via the switch at the end of the
one foot cord. To remove wire rope from the winch,
depress the "CABLE OUT" button. The load will
stop without coasting when the button is released.
To pull a load or spool wire rope onto the drum,
depress the "CABLE IN" button.
This winch is designed to pull 400 lbs (180 KG) for
20 second on the wire rope layer closest to the
drum. Attempts to pull more than this weight or
exceed the duty cycle (on time) may cause damage
to the winch or wire rope. It may also cause
the circuit breaker to trip, and the winch to not
operate. Maintain a minimum of four wraps of wire
rope around the winch drum before attempting any
pulls.
DO NOT PUT ANGULAR LOADS ON THE WINCH.
PULL SHOULD ALWAYS BE PERPENDICULAR TO
WINCH.
KEEP WIRE ROPE TIGHT AND EVEN ON THE
SPOOL.
REPLACE WIRE ROPE WHEN FRAYED.
KEEP WIRE ROPE UNDER TENSION WHEN
OPERATING WINCH. WIRE ROPE WILL "STACK
UP" LOOSELY ON SPOOL IF NOT KEPT UNDER
TENSION.
The wire rope will require periodic attention and
eventual replacement. Inspect the wire rope
frequently. If any fraying exists, replace the wire
rope at once. Your winch uses a galvanized aircraft
type 1/8" DIA. [3 mm] 7 x 19 cable. Always replace
the wire rope with the replacement rope specified in
the parts section of this manual. Because all rope is
subject to wear, it is excluded from our warranty.
LUBRICATION
Your new winch has lifetime lubrication. Grease
leakage out of the winch, especially during the first
few operations, is normal. It is not necessary to
grease or oil any part of the winch at any time. If
grease leakage continues beyond a short period of
time, the winch should be inspected and replaced, if
necessary.
TROUBLESHOOTING
If the winch fails to operate, the circuit breaker on
the end of the winch motor should be checked. If
the circuit breaker has tripped, this will be indicated
by the center portion of the breaker protruding
from the main body. To reset the breaker, press the
center portion back into the assembly.
OPTIONAL WORKSTATION
This OPTIONAL WORKSTATION has been designed
to lift a maximum of 400 lbs (180 KG) once every
10 minutes. Attempts to lift more than this weight
or exceed the duty cycle (on time) may cause the
circuit breaker to trip and the lift to not operate.
For detailed information on the OPTIONAL
WORKSTATION see the manual included with the
Workstation.
NOTE: Repeated tripping of the breaker indicates an
overload condition. Overloading will shorten the life
of your winch.
NEVER USE THE WORKSTATION WITH A PERSON ON
THE RAMP.
Summary of Contents for 622 SO
Page 32: ...32 ORIGINAL INSTRUCTIONS...