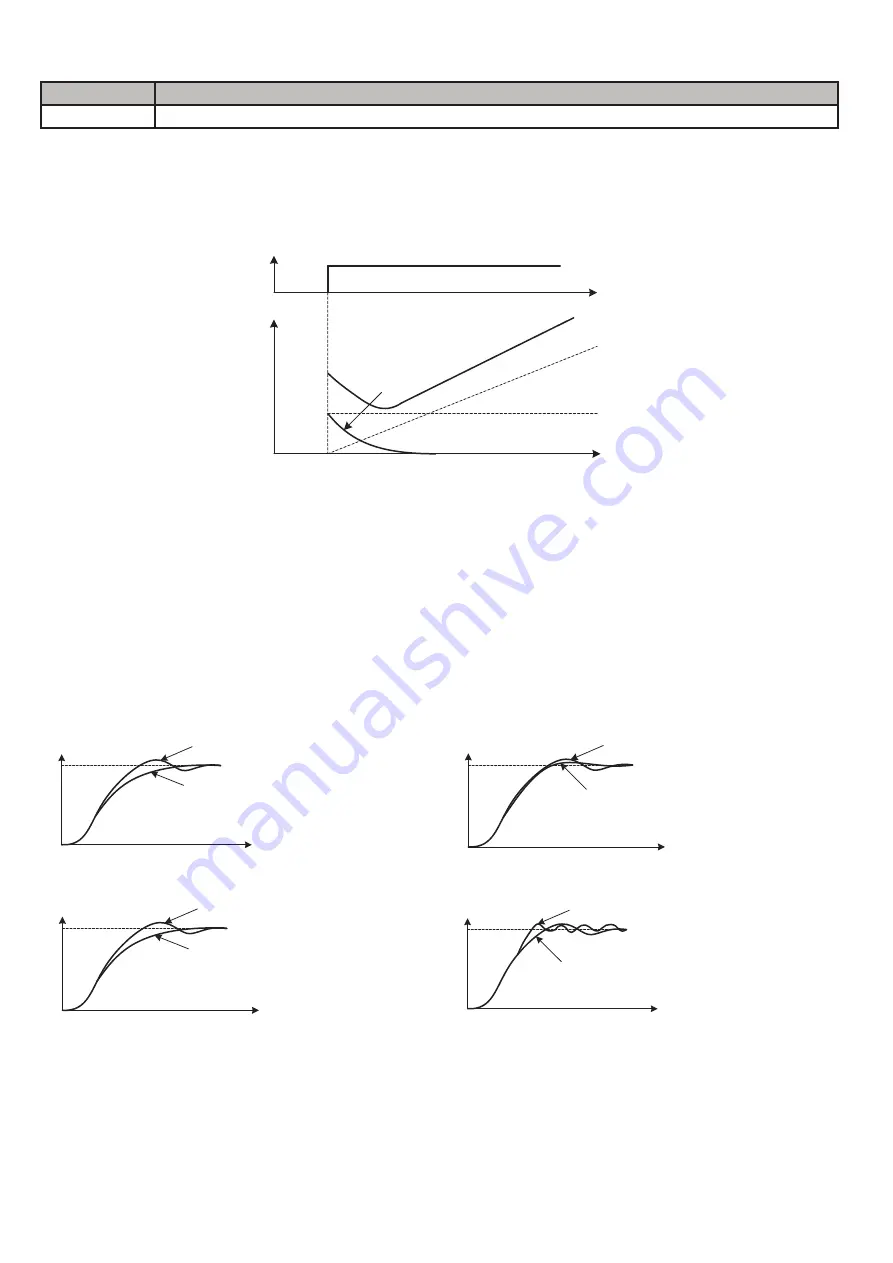
4-124
PID Fine Tuning
All PID control parameters are related to each other and require adjustment to the appropriate values. Procedure for
achieving the minimum steady-state is as follows:
Reduce long-period oscillation
Output
Before
After
t
Adjust integral
time (I) in case of
long-period
system oscillation.
Reduce short-period oscillation
Output
Before
After
t
Adjust differential
time (D) and
proportional (P)
gain when
experiencing
short-period
oscillation.
Reduce overshoot
Output
Before
After
t
If overshoot occurs,
reduce derivative
time (D) and
increase integral
time (I).
Stabilize PID control
Output
Before
After
t
To quickly stabilize
the PID control,
reduce integral time
(I) and increase
differential time (D) if
overshoot occurs.
(1) Increase or decrease the proportional (P) gain until the system is stable using the smallest possible control
change.
(2) Integral (I) reduces the system stability which is similar to increasing the gain. Adjust the integral time so that the
highest possible proportional gain value can be used without affecting the system stability. An increase in the
integral time reduces system response.
(3) Adjust the differential time if necessary to reduce overshoot on startup. Acceleration / deceleration time can also
be used for the same purpose.
10-07
Differential time (D) Default: 0
Range
【
0.00–10.00
】
Sec
Control
Deviation
t
PID Control
t
I Control
P Control
D
10-07 Differential control
: This control is the inverse from integral control and tries to guess the behavior of the error
signal by multiplying the error with the differential time. The result is added to the PID input. Differential control slows
down the PID controller response and may reduce system oscillation.
Note
: Most applications that PID control (fan
and pump) do not require differential control.
Refer to Figure below for PID control operation