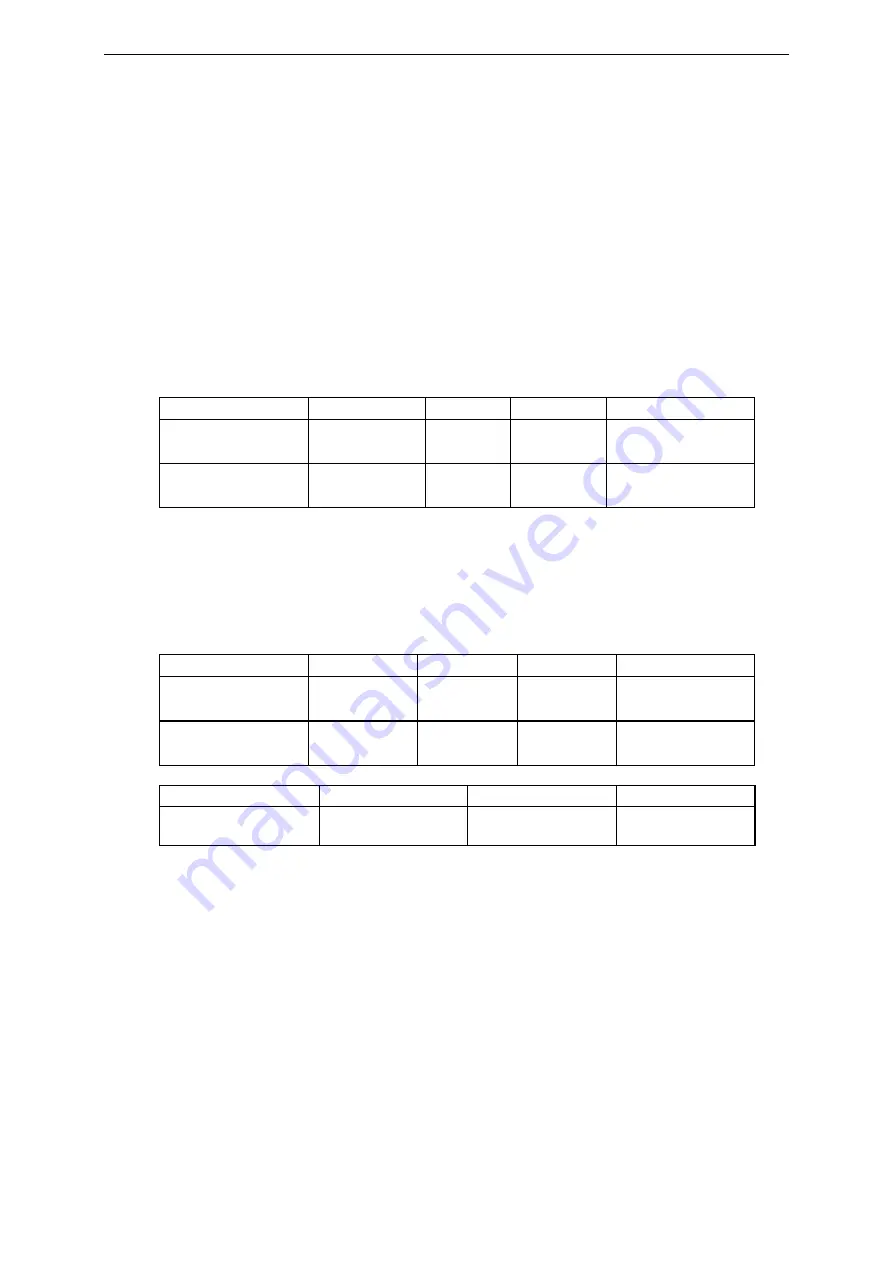
Operating Manual CMGZ 622
60
17.4
Configuration
The configuration defines how many process data (byte and word) are sent during the
cyclic communication from the control system to the tension controller and from the
tension controller to the control system.
To ensure maximum flexibility using the tension controller, there are different
modules supplied. in a single tension controller only one module can be set active at a
time.
Module 1: Basic telegram
4 bytes (2 word) are transmitted from the control system to the tension controller and
also 4 bytes (2 word) from the tension controller to the control system in each data
cycle.
Byte 0
Byte 1
Byte 2
Byte 3
request telegram
(master
→
slave)
function code
channel
number
empty empty
response telegram
(slave
→
master)
function code
or error FFh
channel
number
data
(high byte)
data (low byte)
or error code
Modul 2: Reserved
Modul 3: Basic telegram and 4 word operation value (CMGZ611A, CMGZ630A)
The tension controller responses with 4 bytes of the basic telegram and the 4 words
(feedback, reference, control error, output).
Byte 0
Byte 1
Byte 2
Byte 3
request telegram
(master
→
slave)
function code
channel
number
empty empty
response telegram
(slave
→
master)
function code
channel
number
data
(high byte)
data (low byte)
or error code
Word 0
Word 1
Word 2
Word 3
Feedback Reference
Controller
Error
Output
(HB)/(LB) (HB)/(LB) (HB)/(LB)
(HB)/(LB)
Modul 4: Reserved