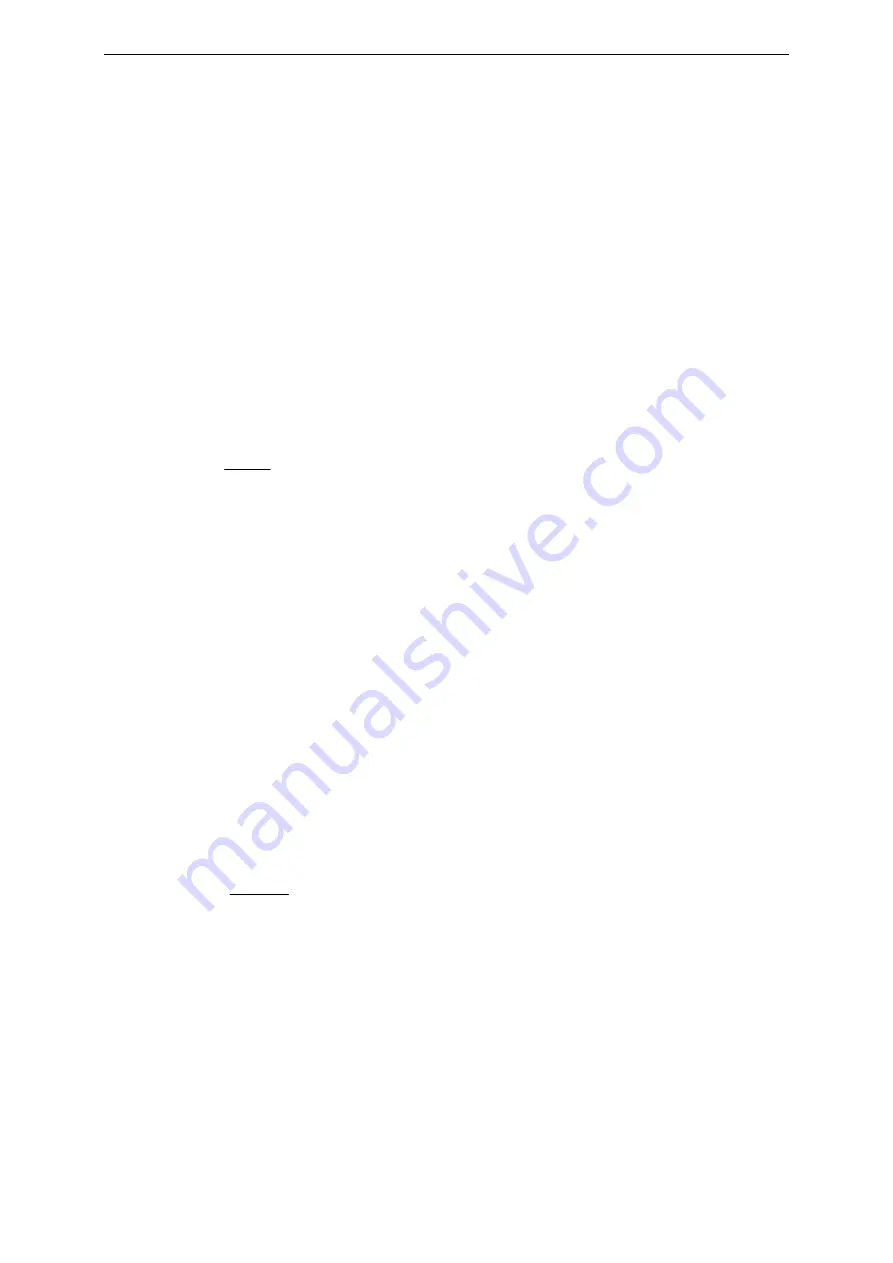
Operating Manual CMGZ 622
35
Parametrization of the tachometer roller
For the controller knowing the actual line speed, the line speed signal has to be set in
relation to the diameter and speed of the tachometer roller:
•
Set line speed signal on the master computer or on a drive already setup to a certain
value, for ex. 5V. Note that value:
U
Line
= ________________ [V]
•
Set tachometer to the running drive roller and read the rotation speed.
Note that value:
n
Tacho
= ________________ [rpm]
•
Reset line speed signal to 0, so that the drive roller will stop.
•
Measure the diameter of the drive roller and input it into parameter
Tachometer
diameter
.
•
Calculate number of rotations per volt using the following formula:
•
Line
Tacho
U
n
P
=
1
= ________________ [rpm/V]
•
Store the
P
1
value in parameter
Tachometer voltage
.
Parametrization of the drive roller
For the controller being able to drive the drive roller correctly, the output signal has to
be set in relation to the diameter and speed of the drive roller:
•
Drive the drive unit with a certain output value, for ex. 5V. Note that value:
U
Output
= ________________ [V]
•
Set tachometer to the running drive roller and read the rotation speed.
Note that value:
n
Drive
= ________________ [rpm]
•
Reset the output signal to 0, so that the drive roller will stop.
•
Measure the diameter of the drive roller and input it into parameter
Center
diameter
.
•
Calculate number of rotations per volt using the following formula:
Output
Drive
U
n
P
=
2
= ________________ [rpm/V]
•
Store the
P
2
value in parameter
Controlled drive
.
Partition the output into line speed overlay signal and PID output signal
•
Set parameter
Line speed overlay
to
Yes
(ref. to „14. Parametrization“)
•
Set parameter
Influence of PID
to an appropriate value, for ex. „10%“
•
Proceed for a test run. Adjust PID control parameters and parameter
Influence of
PID
until the control loop will run stable under all conditions.