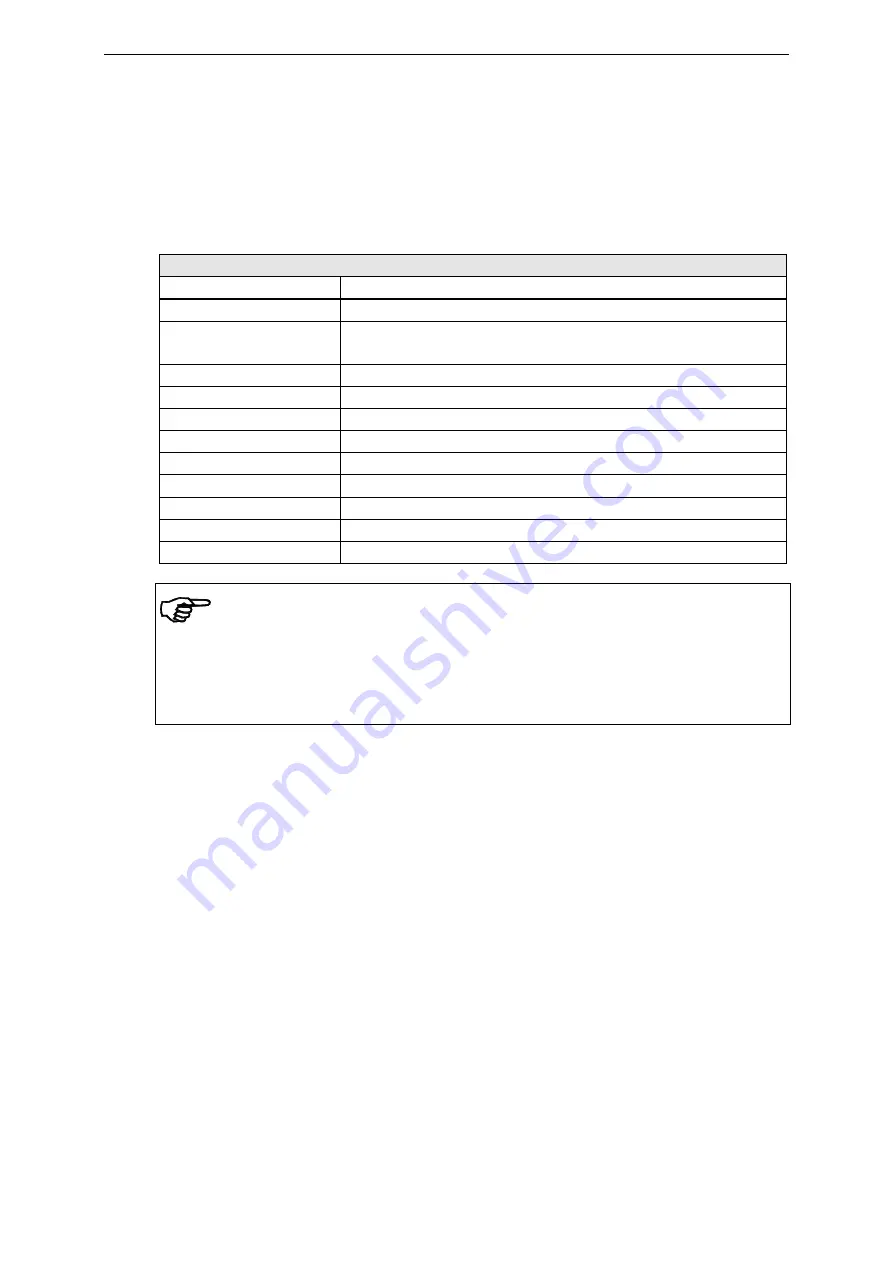
Operating Manual CMGZ 622
31
11
Setup of an Unwind Drive Controller
11.1
Configuring the basic parameters
For an unwind drive controller the following parameters must be set according to your
application:
Parameters CMGZ622
Control mode
Unwind drive
Pilot control
For the time being set to
No
PID configuration
For the time being set to
PI
; if
PID
is required, refer to „9.9
Additional settings“
Output limit
According to the signal level of the drive used
Output configuration
±10V or according to the drive used
Ramp diameter
Reset to default = 1.0 s
Ramp reference
Reset to default = 1.0 s
Reference source
According to machine configuration (
internal
or
external
)
Scale ref.input 1
(Only if reference potentiometer is used)
Scale ref.input 2
(Only if reference potentiometer is used)
Start speed
For the time being set to 0.00
Start limit
For the time being set to 0.0
Note
There is one additional analog input for external reference, diameter or line speed
signal. You cannot run the controller with external reference and pilot control the
same time. You must decide which signal you want to process with the controller and
then set the parameters
Reference source
and
Pilot control
accordingly.
Now continue with section „9.5 Inputting the reference value“. If the general setup is
done, add the special features below according to your requirements.
11.2
Automatic Start Function
With the integrated automatic start function, it is possible to start very carefully even
if the material has some slack, because the controller operates with only a small start
speed until a certain minimum tension value is reached. After reaching the minimum
tension, controlling will be fully activated.
To enable automatic start function, the parameters
Start speed
and
Limit speed
are set
to appropriate values (ref. to „14. Parametrization“).
11.3
Setup of pilot control
The pilot control enables to evaluate the actual reel diameter and to calculate the brake
torque or drive power adapted to the reel diameter (pilot control signal). In addition,
the PID control parameters are dynamically adapted to the reel diameter continuously.
Therefore the controller is only responsible for the material tension variations. This
will increase control loop stability.
Setup of pilot control is done as written under „10.3 Setup of pilot control“.