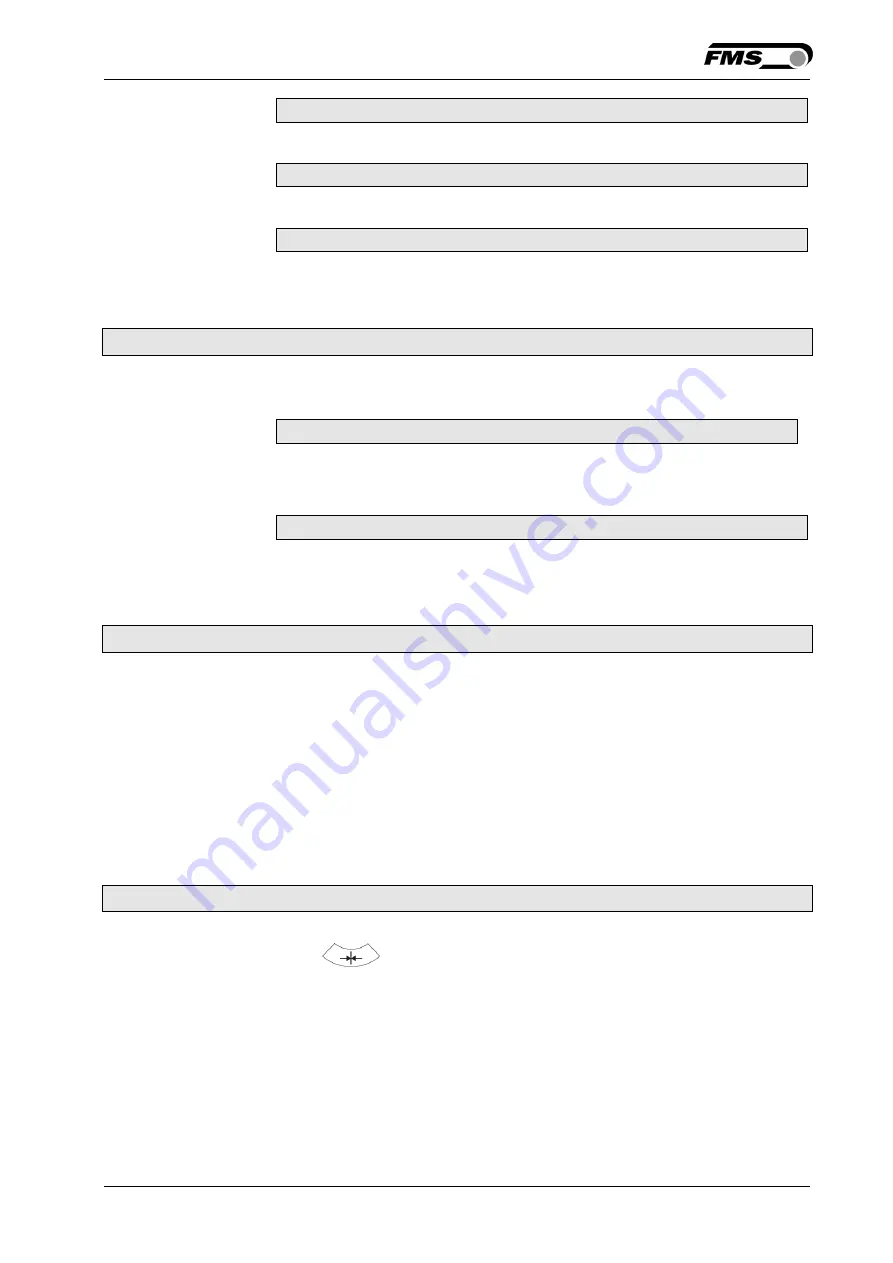
Operating Manual BKS309.W.M
22.02.2019
28
Setting: [Manual]
Description:
The controller is set to manual mode (default)
Setting: [Auto]
Description:
The controller is set to automatic mode.
Setting: [Last
Set]
Description:
The controller is set to the mode that was set before the system has
been shut down.
Leaving the automatic mode [Auto
→
Man]
Description:
This parameter determines the behavior of the controller when you
leave the automatic mode.
Setting: [Manual]
Description:
The control is determined and the controller switches to manual
mode. (Default)
Setting: [Center]
Description:
The control is determined and the steering frame/actuator moves to
the center position. (Default)
Home position of the actuator [Home Pos]
Description:
This parameter determines the home position of the actuator in
retracted position. This position acts as stop and will never be
crossed. Refer to page 17.
Range:
0.0 to
300.0
Default:
0.0
Increment:
0.1
unit: [ mm]
Requirement:
This parameter is only accessible if an actuator of the FMS
winderGLIDE series is installed.
Center position of the actuator [CentrPos]
Description:
This parameter determines the center position of the actuator. If you
press
the actuator approaches this position automatically.
Refer to page 17
.
Range:
0.0 to
300.0
Default:
62.5
4)
Increment:
0.1
unit: [ mm]
Requirement:
4)
The default setting is depending on the type (stroke) of the
installed actuator. This parameter is only accessible if an actuator of
the FMS winderGLIDE series is installed.