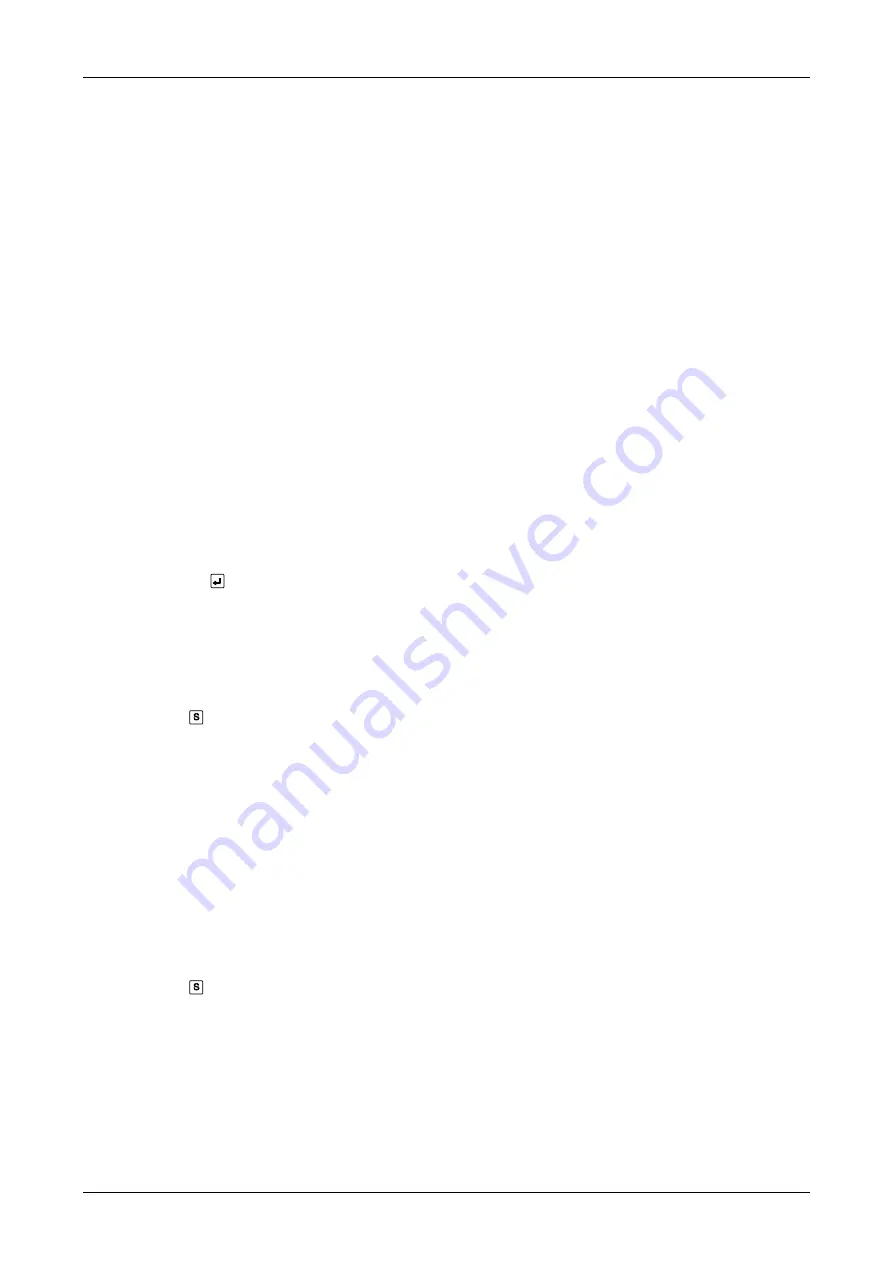
COMMISSIONING
DYNAVERT L
4Bs0503en/002
Version: 11.10.02
14
3a. Menu item P-OPERATION (w
ithout actual value feedback
)
•
enable hidden values.
3b. Menu item P- TRAVEL BEHAVIOUR
(w
ithout actual value feedback
)
•
set I-n-ctrl. to
200
.
•
if required increase
Delta jerk
, especially for systems with great centrifugal masses.
•
if required set direction dependent starting torque.
4.
Menu item P-MOTOR DATA
•
set the motor data according to the type plate:
(
rated speed
,
current
,
frequency
,
voltage
, cos phi).
ATTENTION:
With field weakening parameterize the data of the lower frequency.
•
do the
Auto
(-matic) R1-measuring, to do this activate controller enable X1:42:
1)
parameterize
R1 =
Yes
do the connection to the motor, to do this e.g. press the travel contactor(s) manually.
2)
press button , the
R1
measuring is running for about 3 seconds.
5. Menu item P-CHECK-UP
•
set
Check-Up: Yes
•
press button .
HINT:
If there is the message
Fault:v3 ><brak.dist3
after check-up, the parameterized distance of the braking tag (
P-TRAVEL
CURVE DATA:
Brak.dist.3) is too short. This means that the braking distance can physically not be reached from
nominal speed
v3
.
REMEDY:
−
Check the required minimum braking distance in menu
I-MIN.BRAKING DISTANCES:Brak.dist.3
.
−
Displace the braking tags in the shaft to a distance value higher than the shown required minimum braking
distance from v3, with this set the braking tag distances as large as possible (the delay is started time optimal
automatically).
−
parameterize the new set braking distance in
P-TRAVEL CURVE DATA: Brak.dist.3
.
−
do the
CHECK-UP
.
−
press button .
6. Adjusting the braking tag distances in the shaft (with actual value feedback)
•
travel through the shaft using
revision
and adjust the parameterized
Brak.dist.3
centimeter precisely.
•
adjust the stopping accuracy according to section 1.3.2, see the following page.