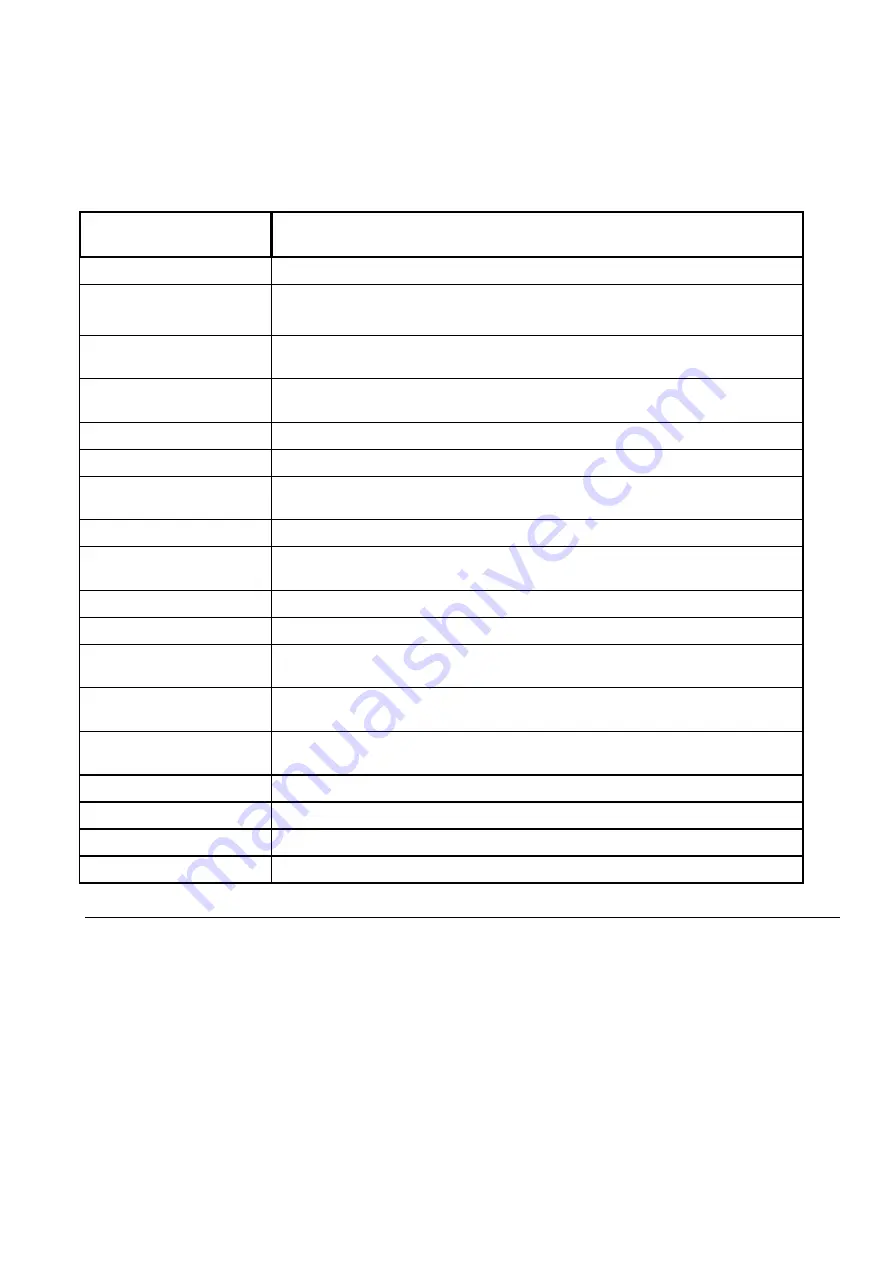
2.5
General messages on the display
In addition to the fault messages the inverter also gives general messages on the status display. These messages
provide information for operation and parameterization of the inverter.
Fault message
on the display
Cause of message
V/I-ctrl. active
The DYNAVERT L reaches the current limit e.g. because of overload of the drive;
wrong motor parameters; too high initial breakaway torque (in case reduce jerk 1);
too high acceleration (in case reduce acceleration)
Initialization
running
The inverter initializes itself after mains voltage ON or processor reset
Para. protected !
no inverter off !
With the current setting of S1.1 no parameter can be changed. The inverter must not
be operating, if the selected parameter should be changed.
Fact.setting copied!
The factory setting has been copied into the actually selected parameter set.
R1 updated !
Automatic R1 measurement has been performed.
No motor connected
Automatic R1 measurement could not be performed, because no motor is
connected, or controller 24V at X1:42) is missing.
Motor too small
The connected motor is too small for automatic R1 measurement.
not possible !
Automatic R1 measurement not possible at the moment (e.g. because of a fault); or
controller 24V at X1:42) is missing.
Para.set changed
Switch-over to another parameter set has been performed.
Check-Up successful
Check of the set parameters for plausibility has been concluded successfully.
Before travel please
perform Check-Up
A parameter has been changed, the value of which has a direct influence on the
travel curve and thus makes Check-Up necessary before travel can be started
Wrong password!
A Password has been arranged in order to protect the parameters, that has not been
entered yet or has not been entered correctly. First of all enter the correct password!
Password correct!
The password has been set correctly, the parameters are enabled to be
parameterized(if not generally avoided by adjusting of S1.1).
Password activated!
A password unequal to 0 has been entered.
No password ness.!
No password has been entered. The password monitoring has been switched off.
Intern paramet.off !
„Internal“ has not been set as parameter source (DIL switch S4).
Param. RS485. off!
„RS 485“ has not been set as parameter source (DIL switch S4).