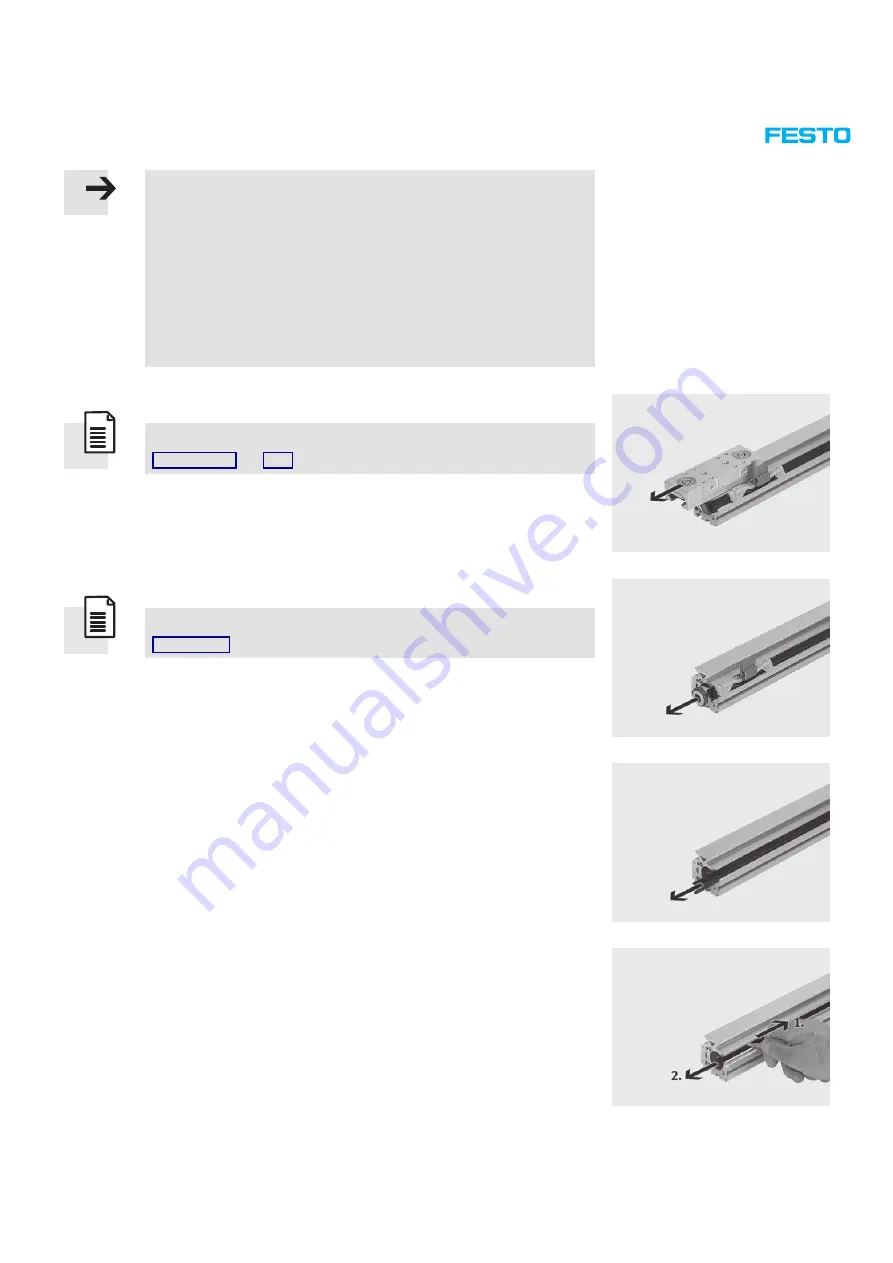
17 / 44
Festo 7DGC-GFa_en
Note
The parts of the slide-piston connection are paired with the slide. In order
to ensure the slide and the slide-piston connection fit backlash-free, the indi
-
vidual parts of the slide-piston connection must be glued in a very precise
manner.
If the glued parts break apart, they can be placed on top of each other again
and re-installed.
You must not apply any additional glue as this will change the fit.
If a part of the slide-piston connection is faulty, the slide itself has to be
replaced because of the pairing.
Push the slide off the cylinder barrel.
•
Documents
Chapters 4.1.3 and 4.1.4 describe how to dismantle and repair the slide.
Push the piston out of the cylinder barrel.
•
Documents
Chapter 4.1.5 describes how to dismantle and repair the piston module.
Pull the cover band out of the cylinder barrel.
•
Push the sealing band inwards and out of the guide slot (1) with a blunt
•
object and pull it out of the cylinder barrel (2).
Summary of Contents for DGC G Series
Page 1: ...Repair instructions en Linear drive DGC G 7DGC Ga_en...
Page 46: ......
Page 47: ......
Page 48: ......
Page 49: ...Repair instructions en Linear drive DGC GF 7DGC GFa_en DG C 2 5 330 GF PPV A 123 456 W7 08...
Page 91: ......
Page 92: ......
Page 93: ...Repair instructions en Linear drive DGC KF 7DGC KFa_en...
Page 136: ......