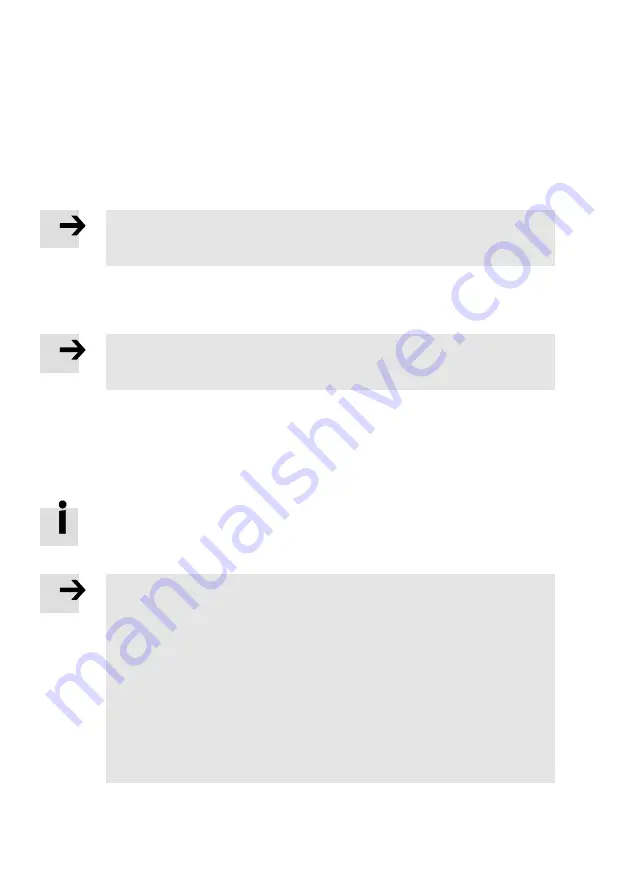
3
Installation
22
Festo – P.BE-CPX-CTEL-EN – 1411a – English
3.5
Connecting the power supply
Take the following aspects into consideration when installing a CPX system with the CTEL master mod
ule:
–
Power supply (
è
–
Current consumption (
è
3.5.2 Determining the current consumption)
–
Formation of voltage zones (
è
CPX system description P.BE-CPX-SYS-…)
Note
Observe the instructions on earthing the I-port devices in the description for the
relevant module.
Recommendation:
When implementing an EMERGENCY-OFF function, guide the load voltage for the corresponding
actuator technology separately.
Note
Check whether pressure switch-off is also necessary for an EMERGENCY-OFF func
tion on your machine/system.
3.5.1
Power supply
The CPX terminal has 3 different conductors:
–
U
EL/SEN:
Power supply (PS) for internal electronics of the module and connected devices
–
U
OUT:
Load voltage supply for digital output modules
–
U
VAL:
Load voltage supply (PL)
for valve terminals, output modules or other consumers.
The load voltage supply U
OUT
is not used by the module described here.
Additional information on power supply and formation of voltage zones (
è
CPX system
description P.BE-CPX-SYS-…).
Note
Malfunctions due to insufficient power supply.
Supply of the load voltage supply U
VAL
must be sufficiently dimensioned to be able
to supply the connected actuators.
Observe that, dependent on the respective length of the I-port connecting cable and
current consumption of the connected I-port device, a voltage drop results between
the CTEL master module and the device.
Therefore, when connecting cables > 5 m are used, the operating voltage supply
U
EL/SEN
should not be fallen below by more than 10 %.
The total current requirement of the CPX terminal and the CTEL system, as well as
the limit values for the maximum current intensities, must be taken into account in
the design of the voltage supply (
è
Summary of Contents for CPX-FB13
Page 62: ......