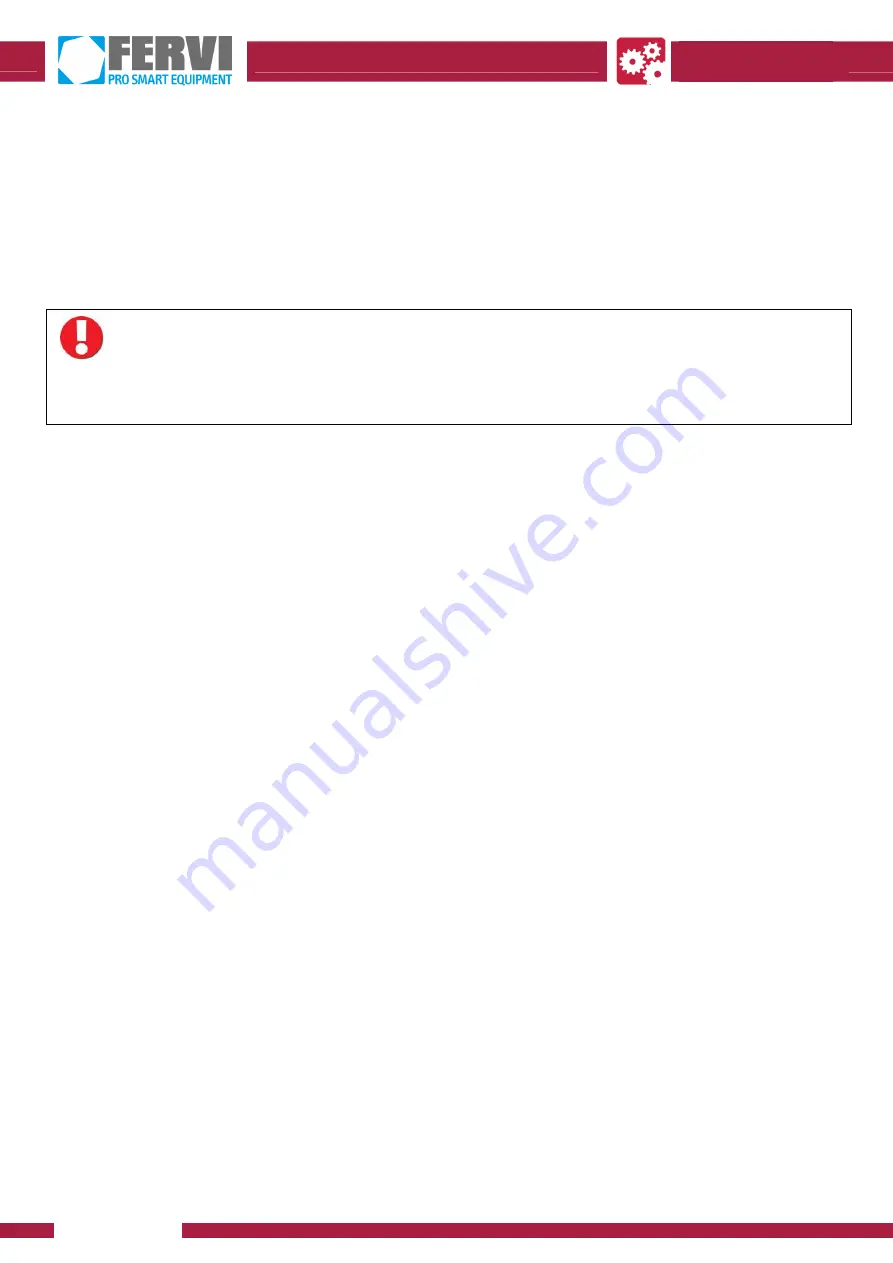
MACHINES AND
ACCESSORIES
Page 26 of 44
8 TRANSPORT AND LIFTING
Use suitable lifting equipment to move the Drill. Please remember that the machine weighs
about 400 kg, so please use lifting equipment with a higher maximum load capacity.
Lifting cranes, cranes and hoists with sufficient load capacity may be considered appropriate.
Means of transport
For choosing an adequate lifting equipment, you should take into account the weight of the
machine and of its packaging (if any).
fervi.com
Summary of Contents for T066
Page 37: ...MACHINES AND ACCESSORIES Page 37 of 44 14 EXPLODED VIEW AND SPARE PARTS f e r v i c o m...
Page 39: ...MACHINES AND ACCESSORIES Page 39 of 44 f e r v i c o m...
Page 42: ...MACHINES AND ACCESSORIES Page 42 of 44 f e r v i c o m...
Page 44: ...MACHINES AND ACCESSORIES Page 44 of 44 15 WIRING PLAN f e r v i c o m...