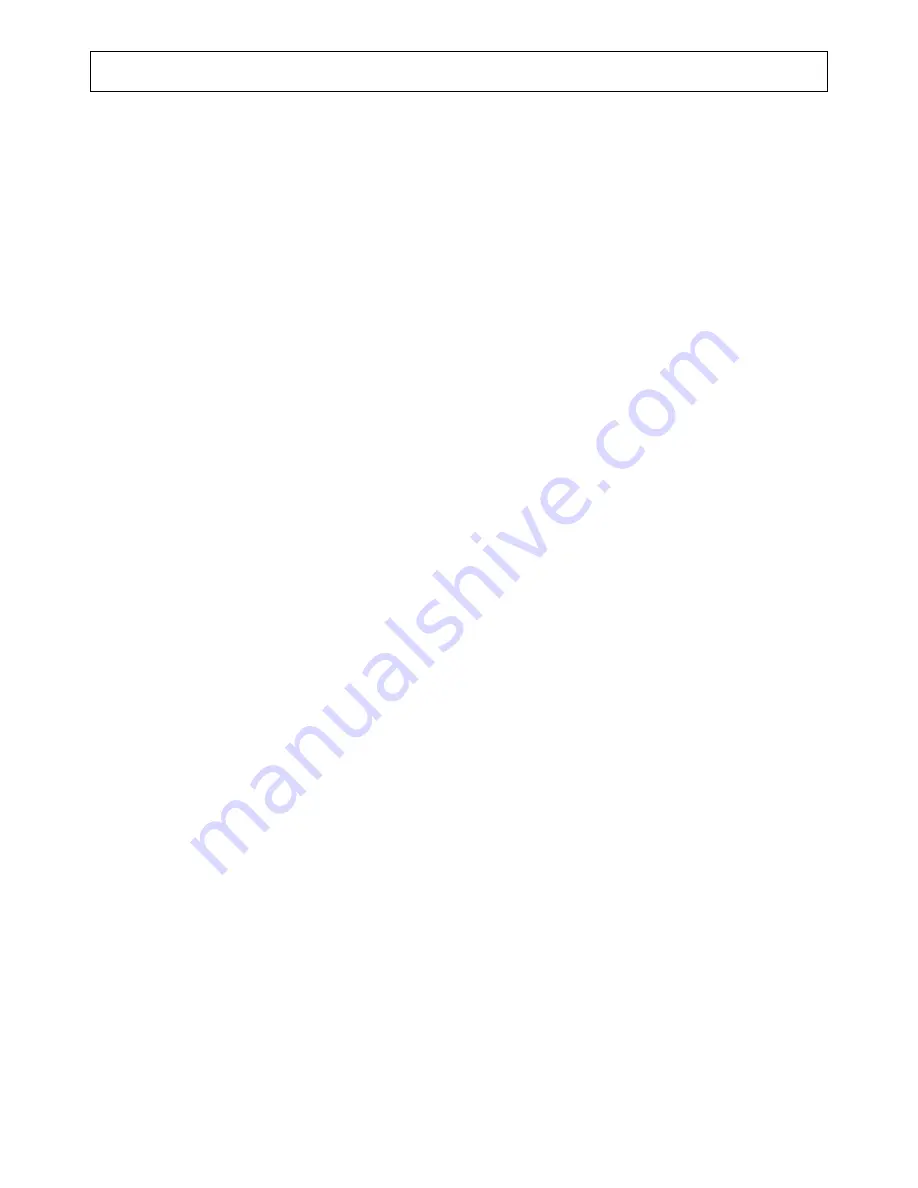
66
• Inspection of the condensing system
wARNING:
The finned pack exchanger has fins made of aluminium or some other thin material, thus even accidental contact could
cause cuts. Comply with the instructions in the relative section.
• Condensing coils
In view of the function of this component, it is very important for the surface of the exchanger to be as free as possible from clogging
caused by items that could reduce the fan’s air flow rate and, thus, the performances of the unit itself.
The following operations may be required:
- Remove all impurities (such as paper scraps, leaves, etc.) that could be clogging the surface of the bank either by hand or using a
brush (comply with the above mentioned safety prescriptions).
- If the dirt has deposited on the fins and is difficult to remove by hand, use a flow of compressed air or pressurized water on the
aluminium surface of the coils, remembering to direct the flow in a vertical and opposite to the standard flow direction to prevent the
fins from being damaged.
- “Comb” the coils with the relative tool, using the appropriate comb spacing for the fins if some parts of them are bent or squashed.
• Helical electric fans
Visually inspect these parts to make sure that the electric fans are well fixed to the bearing grille and that this latter is fixed to the
structure of the unit. Check the fan bearings, causing abnormal noise and vibration, and close the terminal box and cable glands.
• Water heat exchanger
The exchanger must ensure the maximum heat transfer possible so keep it clean and free from dirt that may reduce efficiency; make
sure that the temperature difference between water outlet temperature and evaporation does not increase over time, if the difference
exceeds 8 -10 ° C is necessary to proceed cleaning the water side of the exchanger, keeping in mind the following: water circulation
must be in the opposite direction than normal, the fluid velocity does not exceed 1.5 times the nominal velocity and use just water or
moderately acid products but only water for final washing.
• Water filter
Make sure to clean the filter and remove any impurities that block the proper flow of water, contributing to increase pressure drop and
therefore energy consumption of the pumps.
• Water pumps (if present)
Check leakage, the state of the bearings (any anomalies are highlighted by noise and vibration), the closing of the terminal box and
integrity of the cable.
• Reading and adjustment of the operating parameters
This control can be done using the pressure gauges (if installed) of the refrigerant circuits and using the pressure and temperature
gauges (if installed) of the hydraulic circuits of the unit (evap heat recovery - if present)
Provide a machine book that allows you to track of the actions taken on the unit, so it will be easier to cadence adequately
the various interventions and will facilitate a possible troubleshooting.
Please take note of: date, type of action, description of action, measurements performed, anomalies identified, alarms re
-
gistered in the alarm history, etc. ...
MAINTENANCE
Summary of Contents for RHA series
Page 71: ...71 ...