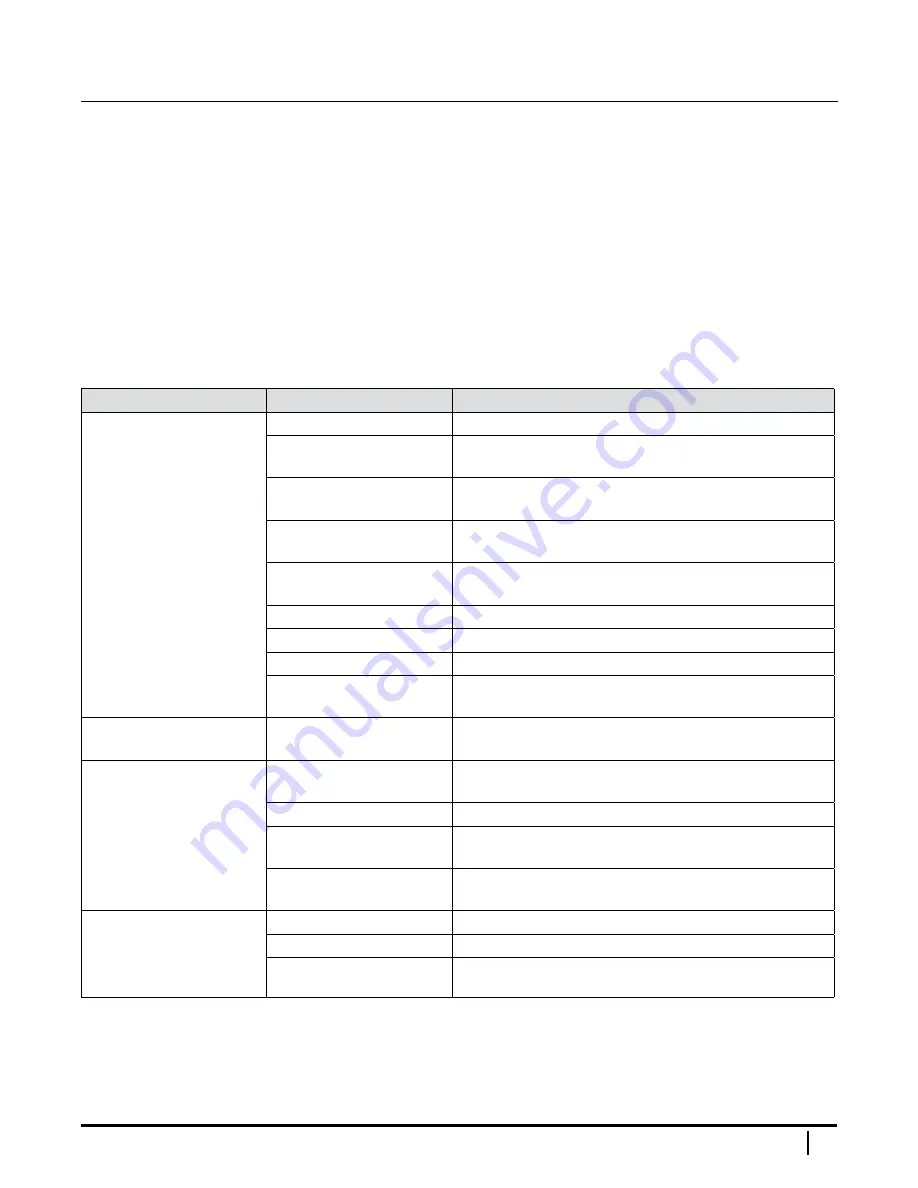
FCI WATERMAKERS, INC.
127
Troubleshooting
One of the most important steps in a high pressure system is to establish a
regular maintenance program. This will vary slightly with each system and
is determined by various elements such as the duty cycle, the liquid being
pumped, the actual specifications vs. rated specifications of the pump, the
ambient conditions, the inlet conditions and the accessories in the system. A
careful review of the necessary inlet conditions and protection devices required
before the system is installed will eliminate many potential problems.
These pumps are very easy pumps to service and require far less frequent service
than most pumps. Typically, only common tools are required, making in‑field service
convenient, however, there are a few custom tools special to certain models that do
simplify the process.
will assist in troubleshooting the high pressure pump.
HIGH PRESSURE PUMP TROUBLESHOOTING
GUIDE
Table 4: High Pressure Pump Troubleshooting Guide
Problem
Probable Cause
Solution
LOW PRESSURE
Air leak in inlet plumbing.
Tighten fittings and hoses. Use PTFE liquid or tape.
Pressure gauge inoperative
or not registering accurately.
Check with new gauge. Replace worn or damaged gauge.
Inlet suction strainer (filter)
clogged or improperly sized.
Clean/adjust relief valve. Replace worn seats/valves and o-rings.
Abrasives in pumped liquid.
Clean filter. Use adequate size filter. Check
more frequently. Install proper filter.
Leaky discharge hose.
Replace discharge hose with
proper rating for system.
Inadequate liquid supply.
Pressurize inlet.
Severe cavitation.
Check inlet conditions.
Worn seals.
Install new seal kit. Increase frequency of service
Worn or dirty inlet/
discharge valves.
Clean inlet/discharge valves or install new valve kit.
PULSATION
Foreign material trapped
in inlet/discharge valves.
Clean inlet/discharge valves or install new valve kit..
WATER LEAK
• Under the manifold
•
Into the crankcase
Worn V-Packings or
Lo-Pressure Seals.
Install new seal kit. Increase frequency of service.
Worn adapter o-rings.
Install new o-rings.
Humid air condensing into
water inside the crankcase.
Install oil cap protector. Change oil every 3 months or 500 hours.
Excessive wear to seals
and V-Packings.
Install new seal kit. Increase frequency of service.
KNOCKING NOISE
•
Inlet supply
• Bearing
•
Pulley
Inadequate inlet liquid supply. Check liquid supply. Increase line size, pressurize.
Broken or worn bearing.
Replace bearing.
Loose pulley on crankshaft
Check key and tighten set screw.
Summary of Contents for MAX-Q+
Page 1: ......
Page 2: ......
Page 16: ......
Page 22: ......
Page 26: ......
Page 31: ......
Page 32: ......
Page 33: ......
Page 34: ......
Page 35: ......
Page 36: ......
Page 37: ......
Page 38: ......
Page 40: ......
Page 41: ......
Page 42: ......
Page 45: ......
Page 46: ......
Page 47: ......
Page 50: ......
Page 51: ......
Page 52: ......
Page 53: ......
Page 54: ......
Page 55: ......
Page 56: ......
Page 57: ......
Page 58: ......
Page 62: ......
Page 72: ......
Page 87: ......
Page 108: ......
Page 113: ......
Page 115: ......
Page 117: ......
Page 122: ......
Page 130: ......
Page 136: ......
Page 137: ......
Page 138: ......
Page 139: ......
Page 140: ......
Page 141: ......
Page 142: ......
Page 143: ......
Page 144: ......
Page 145: ......
Page 146: ......
Page 147: ......
Page 148: ......
Page 149: ......
Page 150: ......
Page 151: ......
Page 152: ......
Page 153: ......
Page 154: ......
Page 155: ......
Page 156: ......
Page 157: ......
Page 158: ......
Page 159: ......
Page 160: ......
Page 161: ......
Page 162: ......
Page 163: ......
Page 164: ......
Page 165: ......
Page 166: ......
Page 167: ......
Page 169: ......