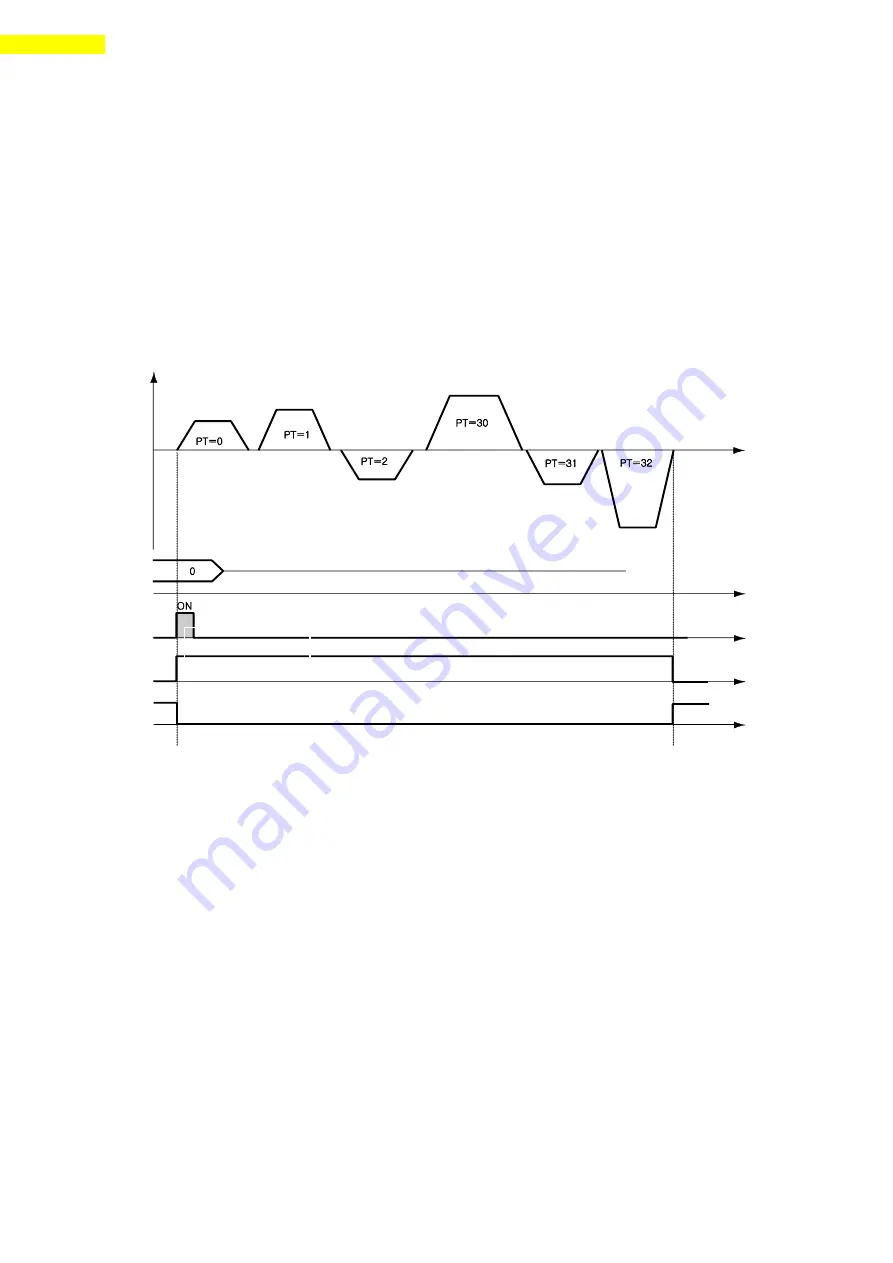
www.fastech.co.kr
Control I/O signal
30
4) Position Table start (PT Start) Input
By using PT A0~A7 signals, set and input the running PT start number. Then the motion pattern
corresponds to the PT No. will be executed.
Following example shows that total 6 motion patterns are in order to execute from No.0 to No.32 and
then stopped.
1) All of PT A0~A7 is set to ‘0’ and PT number is set to ‘0’.
2) Set PT Start signal to [ON], and PT No.0 motion pattern will be executed.
3) When the motion pattern is started by PT, ACK signal and END signal are displayed to [ON] at CN1
output port as illustrated below. The signal is kept until one motion pattern loop is stopped. After all
motions are stopped, the output signal level is set to [OFF].
4) PT Start signal is
edge trigger
type and pulse scale is 10ms or more.
*1. Timing of signals : PT A0~A7 signals must be set before(50msec) PT Start signal set to
[ON].
*2. If the PT A0~A7 signals are not used and the PT Start signal set to [ON] the PT No. 0 will
be executed..
*3. Checking the ‘Moving’ and ‘In-position’ signals:
Between sequential ‘PT Start’ motion command signal, the checking step for motion status
Moving, In-position) is needed before next motion command.
Position table address input (PTA0 – A7)
po
Position table start execution input signal ( PT Start )
po
ACK output signal
po
END output signal
po
Motion pattern
po
Summary of Contents for Ezi-Step II Plus-E
Page 1: ... Rev 03 User Manual Text ...
Page 8: ...www fastech co kr Specifications of the Drive 8 ...
Page 11: ...www fastech co kr 11 Specifications size of the Motor Motor Size 3 2 ...
Page 12: ...www fastech co kr Specifications size of the Motor 12 ...
Page 17: ...www fastech co kr 17 Configuration 2 86 mm motor drive ...
Page 19: ...www fastech co kr 19 Configuration 2 86 mm Motor Drive ...
Page 67: ...www fastech co kr 67 Appendix Brake Installed Motor Specification and Size 12 3 ...