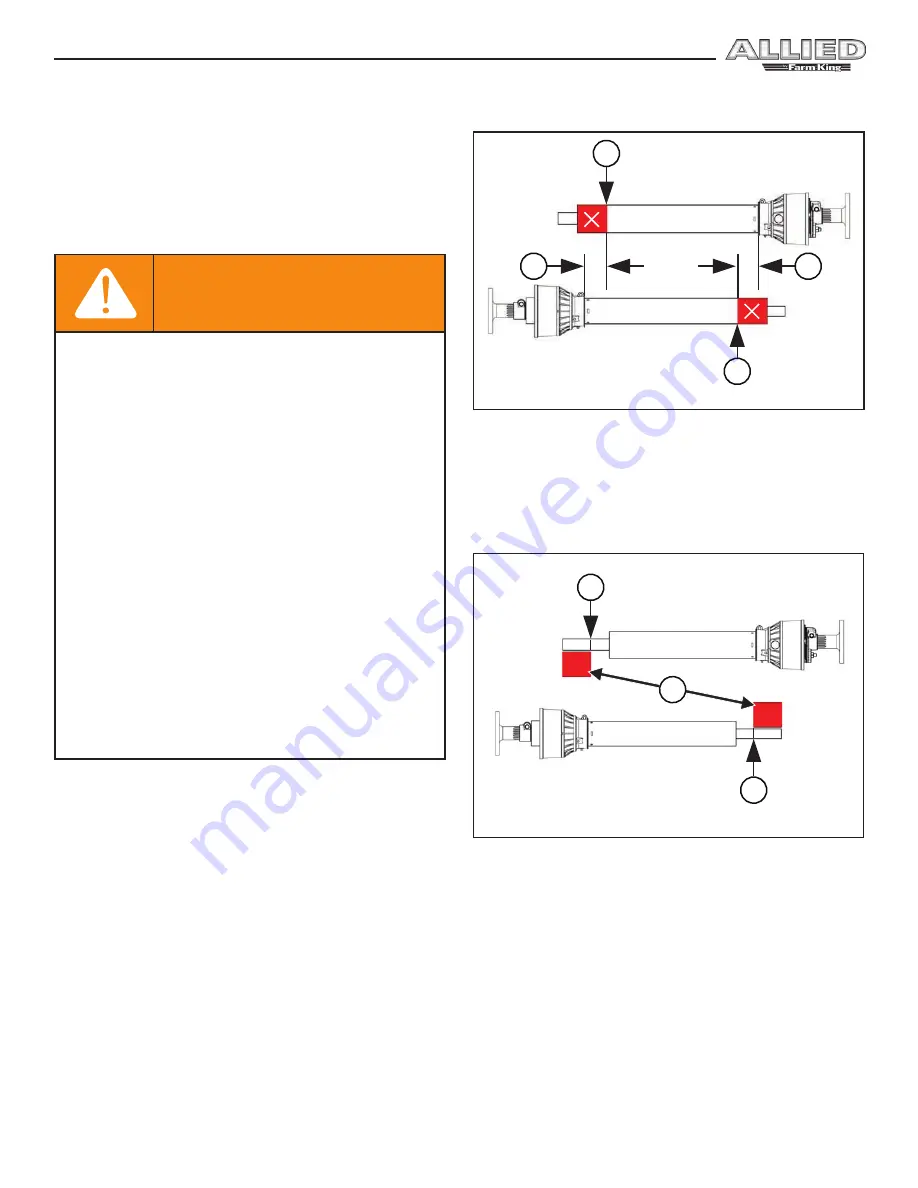
Operation - Binary Series
44
Reducing The PTO Driveline Length
Stop the engine and leave the operator’s position
(See “Leaving The Operator’s Position” in the
Operation section). Make sure the PTO driveline and
all rotating components have come to a complete
stop before leaving the operator’s position.
WARNING
AVOID INJURY OR DEATH
•
Do NOT exceed the rated implement PTO speed.
•
Stay clear of rotating driveline.
•
Keep bystanders away.
•
Keep hands, feet, clothing and long hair away.
•
Keep PTO shields and all guards in place.
•
Disengage PTO, move the tractor controls to
the Neutral position, stop the engine and make
sure all rotating components are stopped before
leaving the operator’s position.
•
Do NOT service the tractor or implement with
the PTO engaged.
•
Do NOT service the implement in a raised
position unless properly blocked and with all
rotating components stopped.
•
Disengage PTO for road travel.
Remove the PTO driveline from the tractor and
place in storage position (if equipped).
Enter the operator’s position (See “Entering The
Operator’s Position” in the Operation section).
Start the engine.
Raise or lower the three-point implement to get
the shortest distance between the tractor PTO shaft
and three-point implement gearbox PTO shaft.
Stop the engine and leave the operator’s position.
Pull the PTO driveline apart and reinstall each
individual section; one half to the tractor PTO shaft
and one half to the implement gearbox PTO shaft.
Figure 32
1. Hold PTO driveline sections parallel to one another
and measure back 2 in. (50.8 mm) (Item 1)
[Figure
32]
from the yoke of each section and place mark on
opposite section. Cut the plastic shield at this length
(Item 2)
[Figure 32].
Figure 33
2. Using the plastic guard lengths that were cut off in
[Figure 32]
, align the cut off lengths (Item 1)
[Figure
33]
with the end of the inner & outer shafts. Place a
mark (Item 2)
[Figure 33]
on the inner & outer shafts
and cut the inner & outer shafts off at this length.
3. Round off all sharp edges and deburr.
4. Thoroughly grease and install the PTO driveline
halves together.
5. Recheck for proper operation.
TRACTOR
PTO SHAFT
TRACTOR
PTO SHAFT
IMPLEMENT
PTO SHAFT
IMPLEMENT
PTO SHAFT
2
2
2
1
1
2
1
Summary of Contents for Allied Binary Series
Page 1: ...092018 FK407 OPERATOR AND PARTS MANUAL Binary Series Snowblower Model 5010 6010 6610 7420 8420...
Page 2: ......
Page 6: ...Warranty Registration Form Binary Series 4...
Page 8: ...Introduction Binary Series 6...
Page 12: ...Introduction Binary Series 10...
Page 14: ...Safety Binary Series 12...
Page 24: ...Assembly Binary Series 22...
Page 40: ...Assembly Binary Series 38...
Page 42: ...Operation Binary Series 40...
Page 52: ...Operation Binary Series 50...
Page 54: ...Maintenance Binary Series 52...
Page 60: ...Maintenance Binary Series 58...
Page 62: ...Parts Identification Binary Series 60...
Page 82: ...Parts Identification Binary Series 80 PTO Shaft 50 60 66 1 5 3 6 7 8 4 5 2 9 11 11 10...
Page 84: ...Parts Identification Binary Series 82 PTO Shaft 74 84 4 5 7 6 1 3 2 10 11 9 3 8...
Page 86: ...Parts Identification Binary Series 84...
Page 88: ...Specifications Binary Series 86...
Page 94: ...Specifications Binary Series 92...
Page 96: ...Warranty Binary Series 94...
Page 99: ......