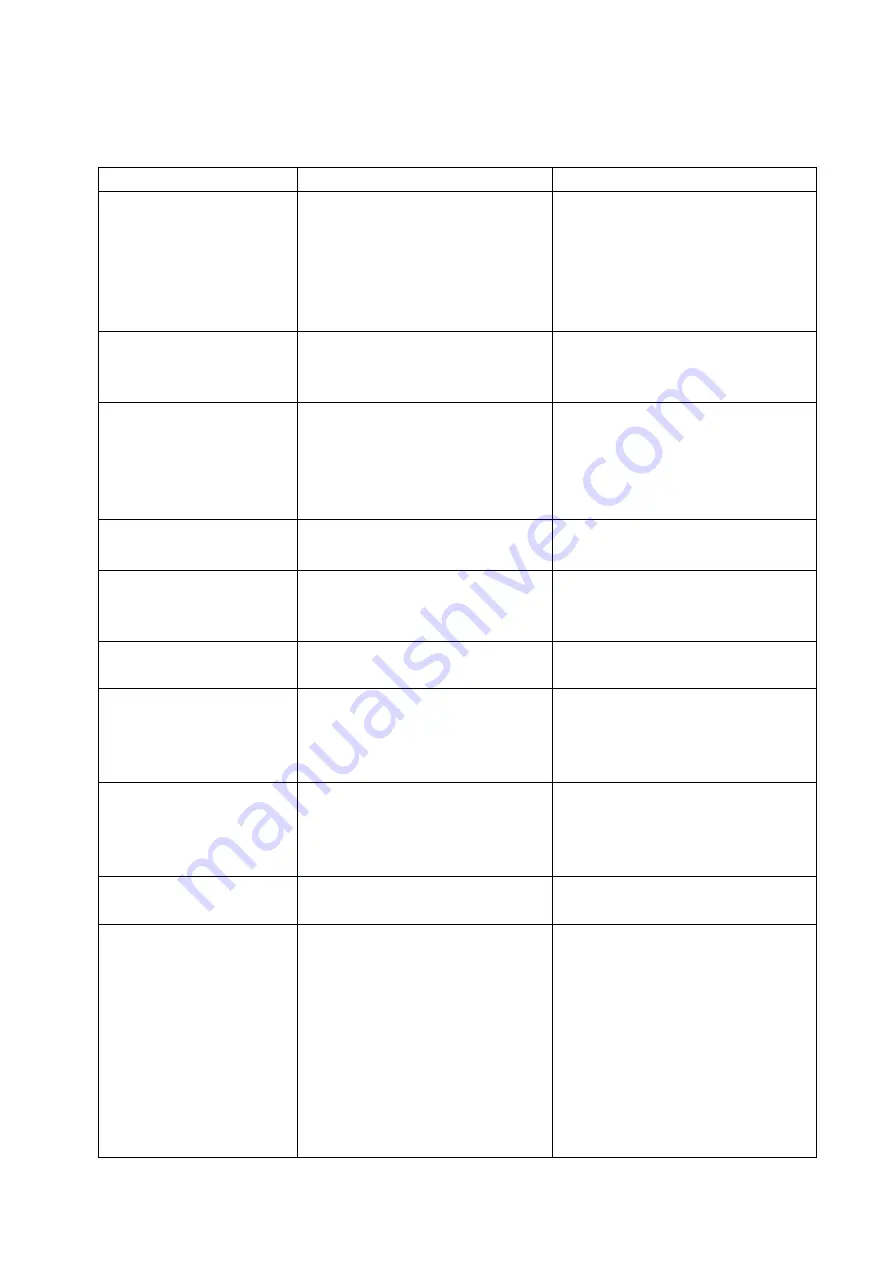
77
6.7 Malfunction and troubleshooting
Table 6-6 Malfuction and troubleshooting
Trouble
Causes
Solution
1. Temperature of extruder
barrel fails to reach the
required temperature.
Steam conditioning temperature is low.
Steam pipeline of Jacket is blocked.
The inlet of steam pipeline in extrude
barrel is blocked
Raise conditioning temperature to make
material temperature to 80
℃
-90
℃
after
conditioning
Clean the steam pipeline of jacket.
Clean the steam pipeline into extruder
barrel.
2. Temperature of conditioning
fails to meet the requirement.
Steam pressure is not sufficient
Steam pipeline is blocked
Check steam pressure.Adjust it to normal
4bar.
Clean the steam pipeline
3. Products look rough with
uneven lengths.
Poor conditioning.
Some die plate holes are blocked
Ground particle size too coarse
Bad quality of die plate.
Enhance material conditioning.
Stop production and clean the die plate.
Improve grinding for finer particles.
Use the die plate made by the reputable
manufacturer.
4.Throughput decreases
Pressure ring or wear ring is worn out;
Screw head is seriously worn out.
a) Replace wear ring or pressure ring
b) Replace screw head
5.Material
cannot
be
discharged in a sudden during
normal operation
Excessive feeding in short-time or
feeding cut-off.
Blocked die holes.
Stop production to check and correct.
6.Uneven
intermittent
discharge
Low filling degree of extruder barrels
Increase feeding.
7.Insufficient expansion
Insufficient gelatinization
Increase feeding.
Raise conditioning temperature.
Raise jacket heating temperature.
Increase rotary speed of main motor.
8.Excessive expansion
Excessive temperature
Rotation speed of main motor too high.
Opening area of die plate does not
match the output
Decrease temperature.
Reduce the rotating speed.
Change the open area of die plate or
adjust the output.
9.Product length too long or
too short
Cutter speed too low or too high
Adjust the cutting transmission speed
10.Poor product forming
Improper raw material formula
Processing temperature too high or too
low.
Unstable feeding
Product moisture content too high or too
low.
Incorrect cutting speed.
Blade is worn out.
Ground particles too coarse.
Change formula of raw materials
Reconfigure the components in machine
barrels.
Adjust to even feeding.
Reduce or increase water or steam
addition.
Adjust the rotating speed appropriately.
Replace blade.
Grind the raw materials to obtain the
defined granularity.