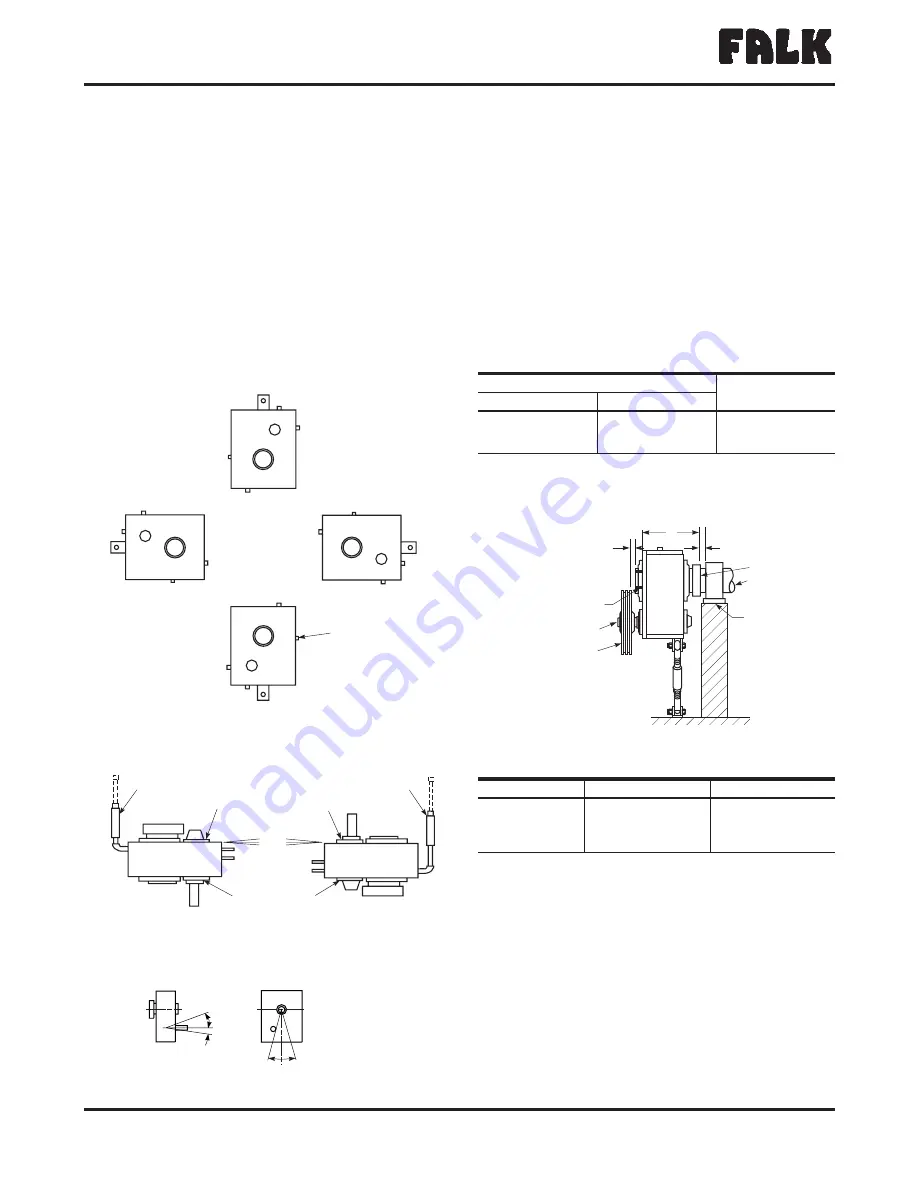
Section I
Drive Installation
Outfitting
1.
JR, JF & JSC —
Find the desired mounting position in Figure
1 and install air vent and magnetic drain plug (packaged
separately with drive). Also note and/or mark the oil level
plug location OR in the case of a vertical mounting, refer to
Appendix E, for installation of vertical stand pipe. If the
mounting angle exceeds the limitations shown in Figure 1,
refer to Appendix E, to determine modifications necessary
within the limits illustrated therein. DO NOT fill drive with
lubricant at this time.
2.
JR —
The tapered bore hollow shaft is designed for use with
a TA Taper bushing for mounting on a driven shaft with a
straight outside diameter. The minimum and maximum
driven shaft engagement, dimension N in Figure 2, are
shown in Table 2. The minimum engagement is necessary
for full bushing engagement; the maximum engagement is
only if a thrust plate will be employed to remove the drive
from the driven shaft (See Appendix C for preferred removal
method). Shaft tolerances for driven shafts are shown in
Table 1.
The Falk Corporation, P.O. Box 492, Zip 53201-0492
378-102
3001 W. Canal St., Zip 53208-4200, Milwaukee, WI USA Telephone: 414-342-3131
August 2004
Fax: 414-937-4359 e-mail: [email protected] web: www.falkcorp.com
Supersedes 6-92
®
a good name in industry
Owners Manual
•
Quadrive Shaft Mounted Drives
(Page 4 of 56)
Sizes 4407/M4407-4608/M4608
F
L
9 O'CLOCK
F
F
L
L
D
D
D
12 O'CLOCK
6 O'CLOCK
REPOSITION PLUGS TO
SUIT REQ'D. MOUNTING
3 O'CLOCK
D = DRAIN
F = FILL & VENT
L = OIL LEVEL
(HIGHEST
SIDE PLUG)
F
L
D
Figure 1
HORIZONTAL DRIVES
MIN. SPACE
REQUIRED FOR
V-BELT CLEARANCE
THRUST
PLATE
BORE
INPUT
SHAFT
MIN. SPACE
REQUIRED TO SPIN
BUSHING UNIT
BUSHING NUT
DRIVEN SHAFT
BEARING
SUPPORT
SHEAVE
N
Figure 2
STANDPIPE &
VENTED DIPSTICK
STANDPIPE &
VENTED DIPSTICK
FILL
FILL
DRAIN
DRAIN
INPUT SHAFT DOWN
INPUT SHAFT UP
±1°
MAX.
VERTICAL DRIVES
20 UP
MAX.
5 DOWN
MAX.
°
°
±10 MAX.
°
ANGULAR LIMITS FOR HORIZONTAL MOUNTING
(ALL CLOCK POSITIONS)
TABLE 2 — N Dimension – Inches (mm)
H
Drive Size
Minimum
Maximum
4407
8.38 (212,9)
12.40 (315,0)
4415
10.33 (262,4)
13.44 (341,4)
4507
10.66 (270,8)
14.53 (369,1)
4608
13.03 (331,0)
17.56 (446.0)
H
The minimum engagement is necessary for full bushing engagement, the
maximum engagement is only if a thrust plate will be employed to remove the
drive from the driven shaft.
TABLE 1 — Driven Shaft Tolerances – In
(mm)
Shaft Diameter
Max Undersize
Over
Thru
2.500 (63,5)
4.000 (101,6)
.006 (0,15)
4.000 (101,6)
6.000 (152,4)
.007 (0,18)
6.000 (152,4)
7.000 (177,8)
.008 (0,20)