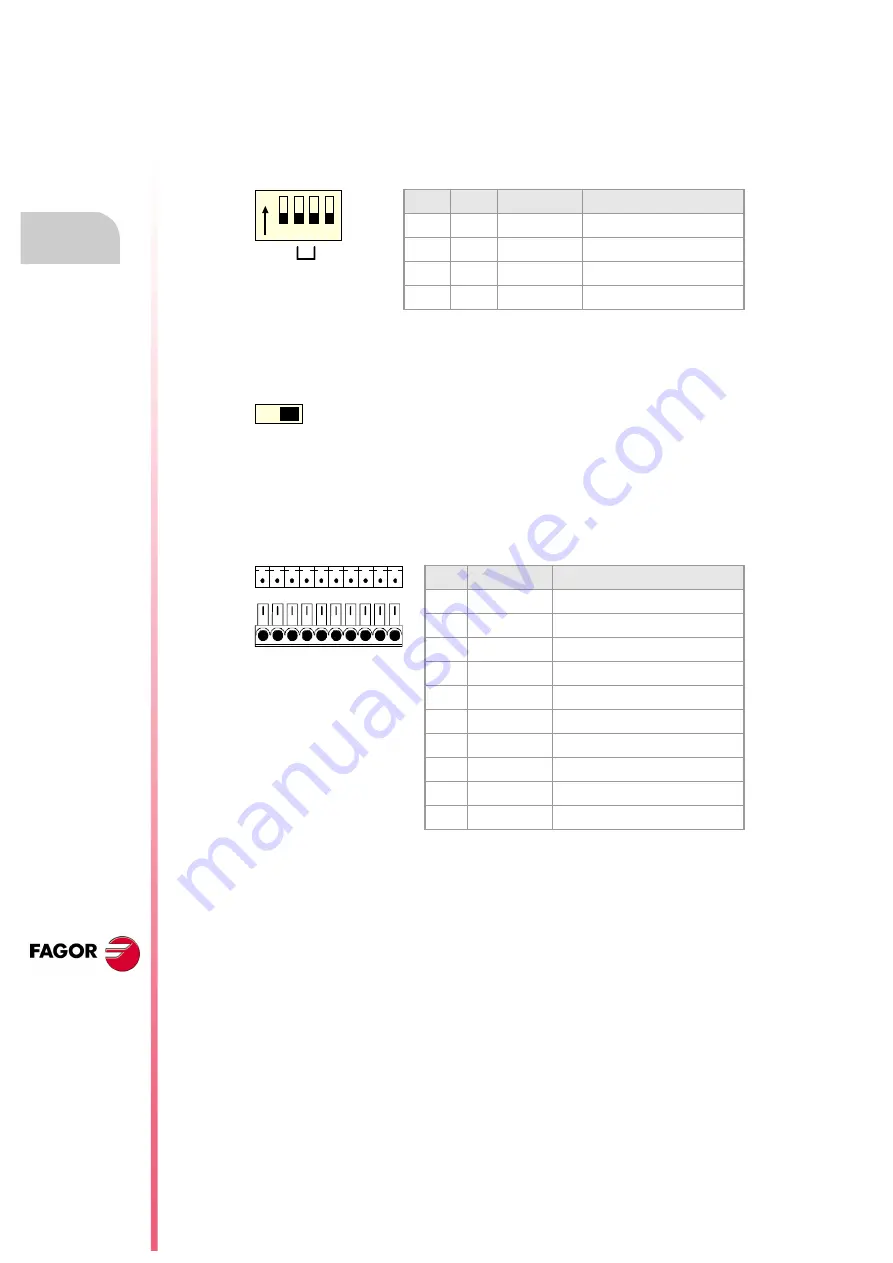
·92·
Hard ware confi gura tion
CNC 8065
8.
(R
EF
: 1404)
OP-
P
ANEL MODULE.
OPERATOR
PANEL W
ITH OR
W
ITHOUT
SPI
NDLE
SPEED OVERRI
DE SELECT
O
R.
CAN bus. Selecting the baudrate for the CANopen bus.
When using the CANopen protocol, the transmission speed at the bus is defined in each node
and they all must run at the same speed. The speed is selected with switches ·2· and ·3· (CO
BR).
The transmission speed depends on the total length of the bus. Using the following illustrative
values; assigning other values may cause communication errors due to signal distortion.
In order for any change of speed to be assumed, the corresponding module must be reset;
however, we recommend to change the speed while the modules and the CNC are off.
CAN bus. ·ST· selector.
The switch position of the terminating elements must be "1" and that of the rest of the
elements "0".
·HANDWHEEL· connector. Handwheel connection.
10-pin male Phoenix minicombicon contact (3.5 mm pitch).
Line terminating resistor. The ·LT· switch identifies which are the
elements that occupy the ends of the CAN bus; i.e. the first and last
physical element in the connection.
1 2 3 4
ON
CAN F
/O
CO
BR
ADD M
S
B
DS ·2·
DS·3·
Speed
Length of the CAN bus.
on
on
1000 kHz
Up to 20 meters.
off
on
800 kHz
From 20 to 40 meters.
on
off
500 kHz
From 40 to 100 meters.
off
off
250 kHz
From 100 to 500 meters.
0
1
Pin
Signal
Function
1
+5 V
Power supply.
2
- - -
3
- - -
4
MPG3-B
B signal of the third handwheel.
5
MPG3-A
A signal of the third handwheel.
6
MPG2-B
B signal of the second handwheel.
7
MPG2-A
A signal of the second handwheel.
8
MPG1-B
B signal of the first handwheel.
9
MPG1-A
A signal of the first handwheel.
10
GND
Power supply.
7
8
9
3
4
5
6
1
2
10
MP
G
2
-B
MP
G
2
-A
MP
G
1
-B
MP
G
1
-A
GN
D
MP
G
3
-B
MP
G
3
-A
5 V
D
C
Summary of Contents for CNC 8065
Page 1: ...Ref 1404 8065 CNC Hardware configuration...
Page 8: ......
Page 10: ......
Page 12: ......
Page 16: ......
Page 20: ......
Page 22: ......
Page 110: ...110 Hardware configuration CNC 8065 REF 1404...