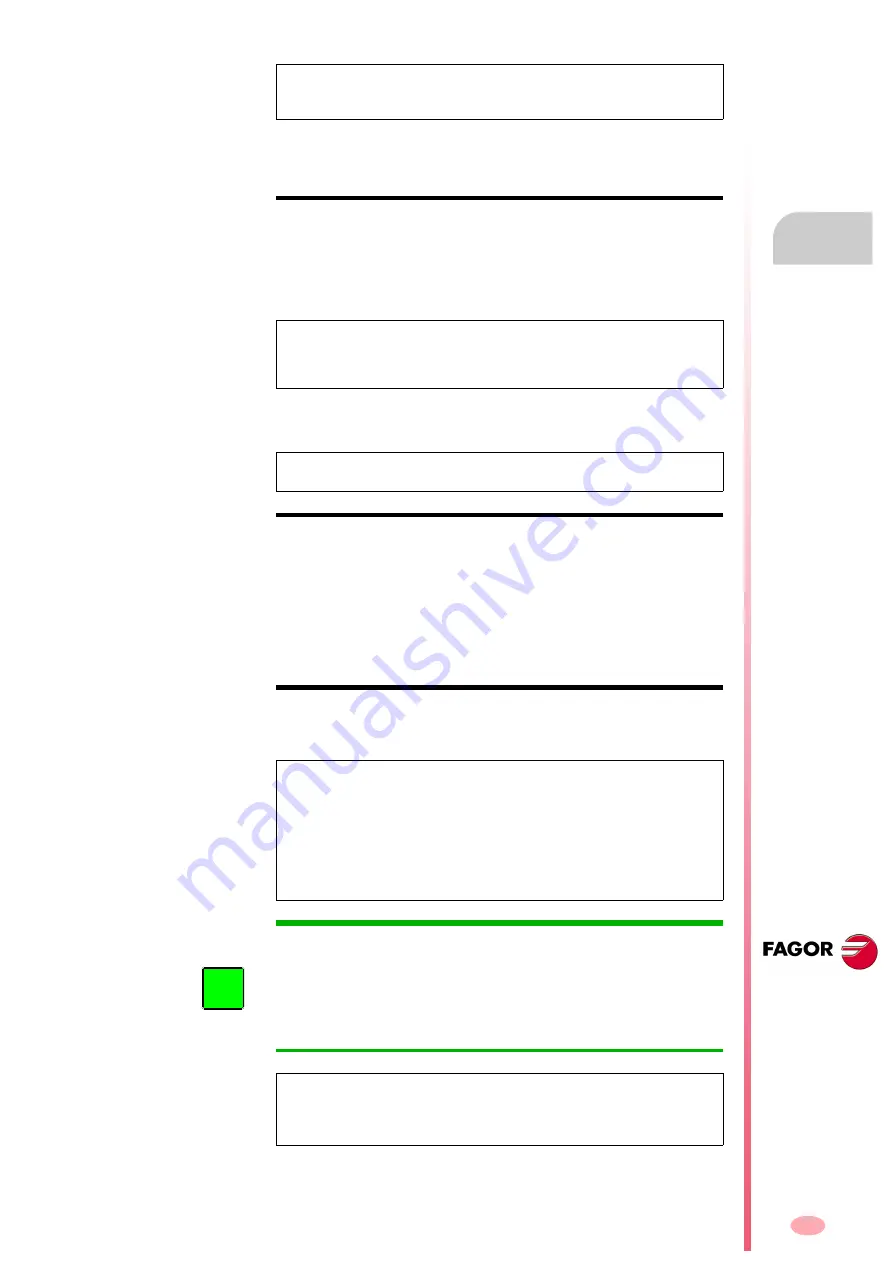
Connection diagrams
CON
N
ECTION DIAGRAMS
El
ectri
cal cabin
et. Dia
grams
10.
333
DDS
HARDWARE
Ref.1310
After activating the relay - KA1, its associated contact closes, to allow sup-
plying three-phase power to the system by pressing the ON button closing
the contactor - KM1. To remove power, press the OFF button.
Error reset
When an error appears at any drive, its “Drive OK” and, therefore, the “Sys-
tem OK” contact of the power supply that feeds it will be open. The relay -
KA1 will be deactivated and its associated contact open and will not be
possible to supply power to the power supply until the cause of the error is
eliminated, as long as it is a non-resettable error.
The contact associated with the ON button resets the errors. This proce-
dure may close the “Drive OK” and “System OK” activating the - KA1 re-
lay and, while ON is still pressed, enable - KM1.
Activating the “System Speed Enable” of the power supply and the
“Speed Enable” of the drives
The “System Speed Enable” signal of the power supply is activated after
closing the contact KA2 with 24 V DC as a result of activating the relay -
KA2. Observe that KM1 has been closed earlier.
Now, the CNC may enable each axis (CNC Enable) and enable the
“Speed Enable” signal of each drive by means of relays - KA4, - KA5, -
KA6 and - KA7.
Activating the “Drive Enable” of the drives
Closing the contact associated with - KA2 excites the relay - KA3 with 24
V; this relay activates the “Drive Enable” signal of all the drive modules.
NOTE. Observe that
a push-button (N.O.,
N
ormally
O
pen) is included in
parallel with the limit switches for disabling (via PLC) the movement of
the axes of the machine in the opposite direction.
NOTE.
Some of these errors (called non-resettable) may be eliminated by
applying 24 V DC to the Error Reset pin of the power supply. See chapter
14 in the “man_dds_soft.pdf” manual for further information on these er-
rors.
NOTE.
This circuit configuration joins the error reset and the system
power-up in a single push-button.
NOTE.
Observe that - KA3 is a delayed-deactivation relay where the de-
sired delay time t may be programmed. It may be used to keep contactor
- KM1 closed while braking a system for the necessary number of sec-
onds to give the power supply enough time to return the excess energy to
mains as long as the system has regenerative power supplies and it is
connected to mains (S1 closed) obviously. The delay time “t” to program
relay - KA3 must be slightly longer than the time it takes the system to
come to a full stop.
INFORMATION.
In the diagrams provided later on, the green ON light indi-
cates that the “System Speed Enable” of the power supply is activated; in
other words, the “Speed Enable” in each drive related to it and the SPENA
signal of the CNC (sent to each drive via SERCOS or CAN) are activated
and there will then be motor torque (Drive Enable signal at each drive and
DRENA signal of the CNC). The red OFF light indicates that all the previ-
ous signals are disabled.
i
NOTE.
Remember that a drive will only respond to an external velocity
command when the Drive Enable, Speed Enable and System Speed En-
able signals (besides the DRENA and SPENA signals of the CNC) are ac-
tive (24 V DC).
Summary of Contents for APS-24
Page 1: ...DRIVE DDS Hardware manual Ref 1310...
Page 6: ...I 6 DDS HARDWARE Ref 1310...
Page 9: ......
Page 10: ......
Page 11: ......
Page 12: ......
Page 16: ...16 Ref 1310 DDS HARDWARE...
Page 30: ...1 DESCRIPTION 30 Description DDS HARDWARE Ref 1310...
Page 94: ...2 POWER SUPPLIES 94 Power supplies DDS HARDWARE Ref 1310...
Page 188: ...3 DRIVE MODULES 188 Drive modules DDS HARDWARE Ref 1310...
Page 204: ...4 AUXILIARY MODULES 204 Auxiliary modules DDS HARDWARE Ref 1310...
Page 232: ...SELECTING CRITERIA 5 232 Selection criteria DDS HARDWARE Ref 1310...
Page 266: ...7 CABLES 266 Cables DDS HARDWARE Ref 1310...
Page 312: ...8 INSTALLATION 312 Installation DDS HARDWARE Ref 1310...
Page 326: ...9 FUNCTIONAL SAFETY 326 Functional safety DDS HARDWARE Ref 1310...
Page 354: ...10 CONNECTION DIAGRAMS 354 Connection diagrams DDS HARDWARE Ref 1310...
Page 378: ...12 SALES REFERENCES 378 Sales references DDS HARDWARE Ref 1310...
Page 384: ...13 COMPATIBILITY 384 Compatibility DDS HARDWARE Ref 1310...
Page 385: ......