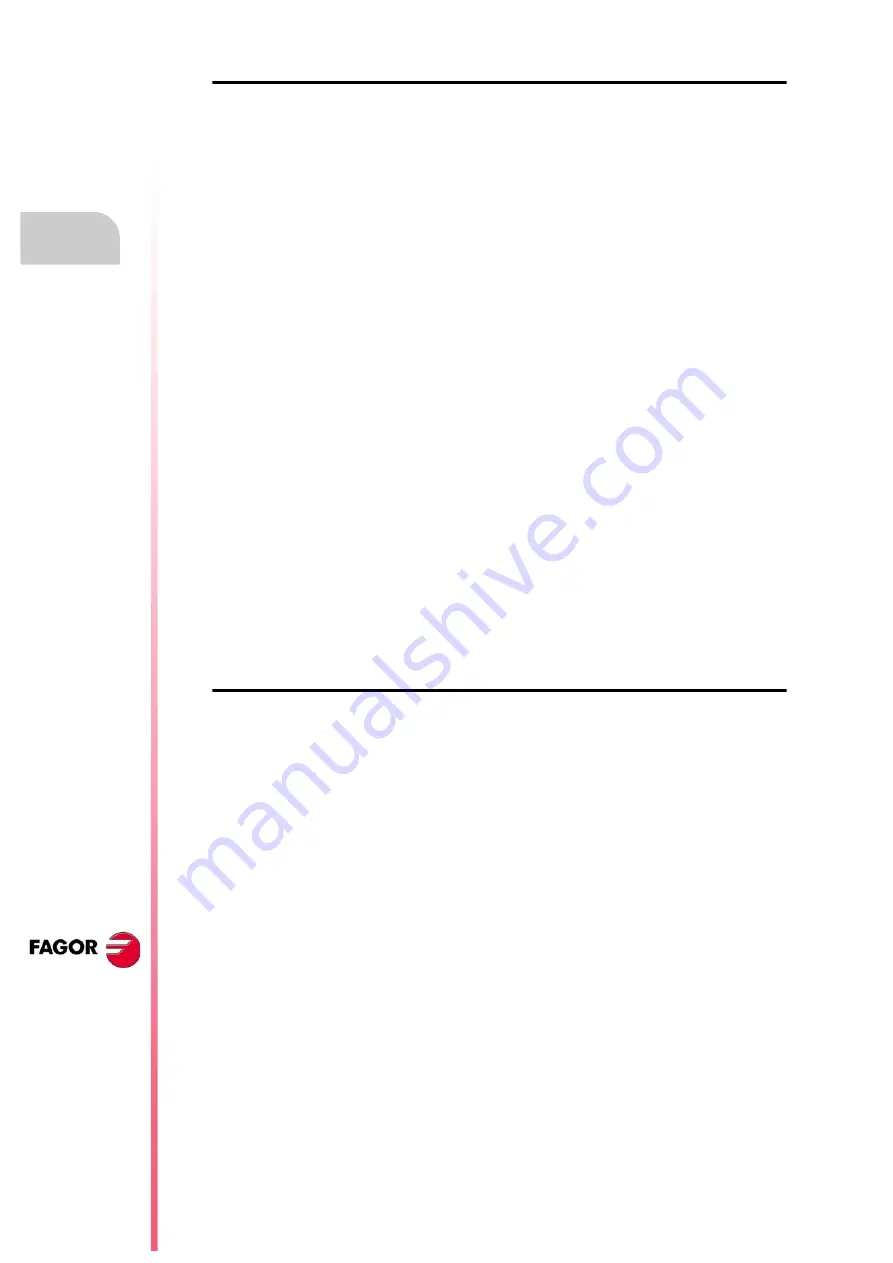
Installation manual
CNC 8035
3.
MA
CHIN
E
AND
POWER
CONNECTION
Setup
(S
OFT
M: V15.3
X
)
(S
OFT
T: V16.3
X
)
·68·
Machine reference point (home) adjustment for each axis
Once the movement of the axes has been properly adjusted, place the travel-limit switches back
where they should be.
The following adjusting sequence is one of the many that could be used:
•
This adjustment should be done one axis at a time.
•
Indicate in the a.m.p. REFPULSE (P32) the type of marker pulse Io being used for Home Search.
•
Set a.m.p. REFDIREC (P33) to indicate the direction of the axis when searching Home.
•
Set g.m.p. REFEED1 (P34) and REFEED2 (P35) to indicate the feedrates for Home search.
•
a.m.p. REFVALUE (P36) will be set to “0”.
•
Once in the JOG mode and after positioning the axis in the right area, start homing the axis.
When done, the CNC will assign a "0" value to this point.
•
If the machine reference zero is in a different physical location from the machine reference point
(location of the marker pulse), proceed as follows:
After moving the axis to a known position (with respect to Machine Reference Zero), observe
the position reading of the CNC for that point.
This will be the distance away from the machine reference point; thus, the value to be assigned
to a.m.p. REFVALUE (P36) will be:
Machine coordinate of the measured point - CNC reading at that point.
Example:
If the point whose known position is located 230 mm from Machine Reference Zero and the CNC
reads -123.5 mm as the coordinate value for this point, the coordinate of the Machine Reference
Point with respect to Machine Reference Zero will be:
REFVALUE = 230 - (-123.5) = 353.5 mm.
Assign this new value and press [RESET] so it is assumed by the CNC.
It is also necessary to search Home once again in order for this axis to assume the correct
reference values.
Axis travel limits (software limits)
Once all the axes have been referenced, their software limits must be measured and set.
This is achieved a single axis at a time as follows:
•
Move the axis in the positive direction towards the end of the axis travel stopping at a safe
distance from the mechanical end-of-travel stop.
•
Assign the coordinate shown by the CNC for that point to a.m.p. LIMIT+ (P5).
•
Repeat these steps in the negative direction assigning the resulting coordinate to a.m.p. LIMIT-
(P6).
•
Once this process is completed, hit SHIFT RESET or turn the CNC off and back on in order for
it to assume the new values.
Summary of Contents for 8035-M
Page 1: ...Soft M V15 3x Soft T V16 3x CNC 8035 Ref 1106 INSTALLATION MANUAL M T MODELS...
Page 2: ......
Page 4: ......
Page 10: ......
Page 12: ......
Page 18: ...CNC 8035 18 Version history M...
Page 24: ...CNC 8035 24 Version history T...
Page 28: ...CNC 8035 28 Safety conditions...
Page 32: ...CNC 8035 32 Material returning terms...
Page 34: ...CNC 8035 34 Additional remarks...
Page 36: ...CNC 8035 36 Fagor documentation...
Page 56: ...Installation manual CNC 8035 1 CNC CONFIGURATION CNC structure SOFT M V15 3X SOFT T V16 3X 56...
Page 178: ...Installation manual CNC 8035 4 MACHINE PARAMETERS Tables SOFT M V15 3X SOFT T V16 3X 178...
Page 424: ......
Page 430: ...Installation manual CNC 8035 B APPENDIX Probe connection SOFT M V15 3X SOFT T V16 3X 430...
Page 450: ...Installation manual CNC 8035 G APPENDIX Key codes SOFT M V15 3X SOFT T V16 3X 450...
Page 454: ...Installation manual CNC 8035 I APPENDIX Key inhibiting codes SOFT M V15 3X SOFT T V16 3X 454...
Page 468: ...CNC 8035 N APPENDIX SOFT M V15 3X SOFT T V16 3X 468 Installation manual...
Page 469: ...CNC 8035 N SOFT M V15 3X SOFT T V16 3X 469 Installation manual...
Page 470: ...CNC 8035 N SOFT M V15 3X SOFT T V16 3X 470 Installation manual...