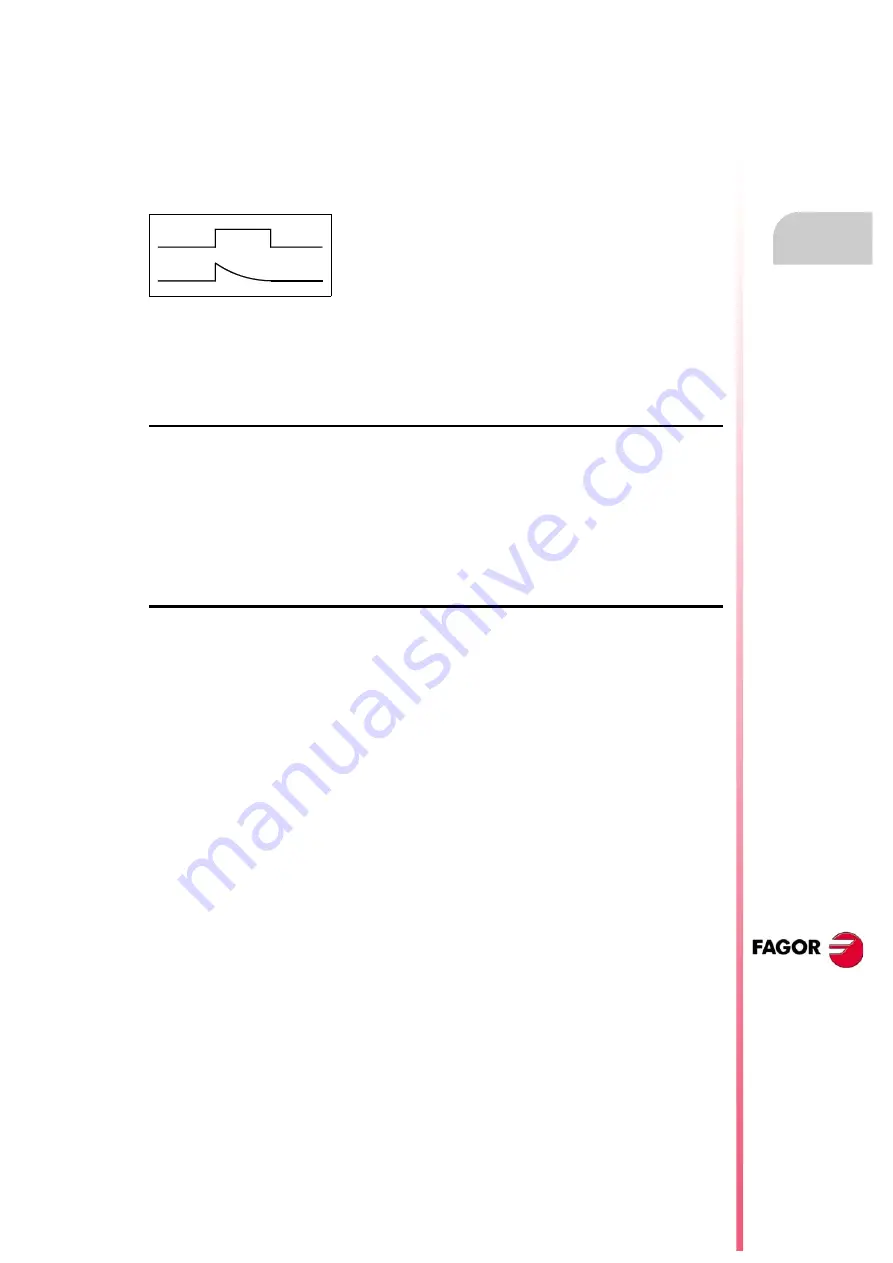
Installation manual
CNC 8035
CONC
EPTS
Axi
s
ad
justment
5.
(S
OFT
M: V15.3
X
)
(S
OFT
T: V16.3
X
)
·209·
5.5.6
Leadscrew backlash compensation.
On this CNC, the leadscrew backlash may be compensated for when reversing the direction of
movement. Leadscrew backlash is defined with a.m.p. BACKLASH (P14).
Sometimes, an additional velocity command pulse may also be needed to recover the possible
backlash when reversing the axis movement. The additional velocity command pulse may be either
rectangular or exponential.
a.m.p. BACKNOUT (P29) sets the value of the additional velocity command and a.m.p. BACKTIME
(P30) indicates the duration of this additional command pulse and general machine parameter
ACTBAKAN (P145) indicates the type of backlash peak applied.
Cutting the compensation peak off.
Every time the axis movement is inverted, the CNC will apply to that axis the velocity command
corresponding to the movement plus an additional velocity command (to make up for backlash). This
additional command is eliminated (compensation peak cutoff) depending on the values of the
following parameters:
G.m.p. BAKTIME (P30), g.m.p. ACTBAKAN (P145) and a.m.p. PEAKDISP (P98).
Hysteresis in the reversal movement compensation command
Axis machine parameter REVEHYST (P99) is used to be able to control when the compensation
should really be applied after detecting a movement reversal and not applying it every time a reversal
command is received.
This feature should only be applied in situations where the moving direction reversals are very small
(e.g. ±1dµm) The purpose is to prevent the reversal compensation to be applied in these situations,
because it can cause slight machining marks (ridges) on the part.
If the duration of the rectangular pulse is adjusted for low speed,
it may be too high for high speed or not enough for low speed when
adjusted for high speed. In these cases, it is recommended to use
the exponential type that applies a strong pulse initially and
decreases in time.
Summary of Contents for 8035-M
Page 1: ...Soft M V15 3x Soft T V16 3x CNC 8035 Ref 1106 INSTALLATION MANUAL M T MODELS...
Page 2: ......
Page 4: ......
Page 10: ......
Page 12: ......
Page 18: ...CNC 8035 18 Version history M...
Page 24: ...CNC 8035 24 Version history T...
Page 28: ...CNC 8035 28 Safety conditions...
Page 32: ...CNC 8035 32 Material returning terms...
Page 34: ...CNC 8035 34 Additional remarks...
Page 36: ...CNC 8035 36 Fagor documentation...
Page 56: ...Installation manual CNC 8035 1 CNC CONFIGURATION CNC structure SOFT M V15 3X SOFT T V16 3X 56...
Page 178: ...Installation manual CNC 8035 4 MACHINE PARAMETERS Tables SOFT M V15 3X SOFT T V16 3X 178...
Page 424: ......
Page 430: ...Installation manual CNC 8035 B APPENDIX Probe connection SOFT M V15 3X SOFT T V16 3X 430...
Page 450: ...Installation manual CNC 8035 G APPENDIX Key codes SOFT M V15 3X SOFT T V16 3X 450...
Page 454: ...Installation manual CNC 8035 I APPENDIX Key inhibiting codes SOFT M V15 3X SOFT T V16 3X 454...
Page 468: ...CNC 8035 N APPENDIX SOFT M V15 3X SOFT T V16 3X 468 Installation manual...
Page 469: ...CNC 8035 N SOFT M V15 3X SOFT T V16 3X 469 Installation manual...
Page 470: ...CNC 8035 N SOFT M V15 3X SOFT T V16 3X 470 Installation manual...