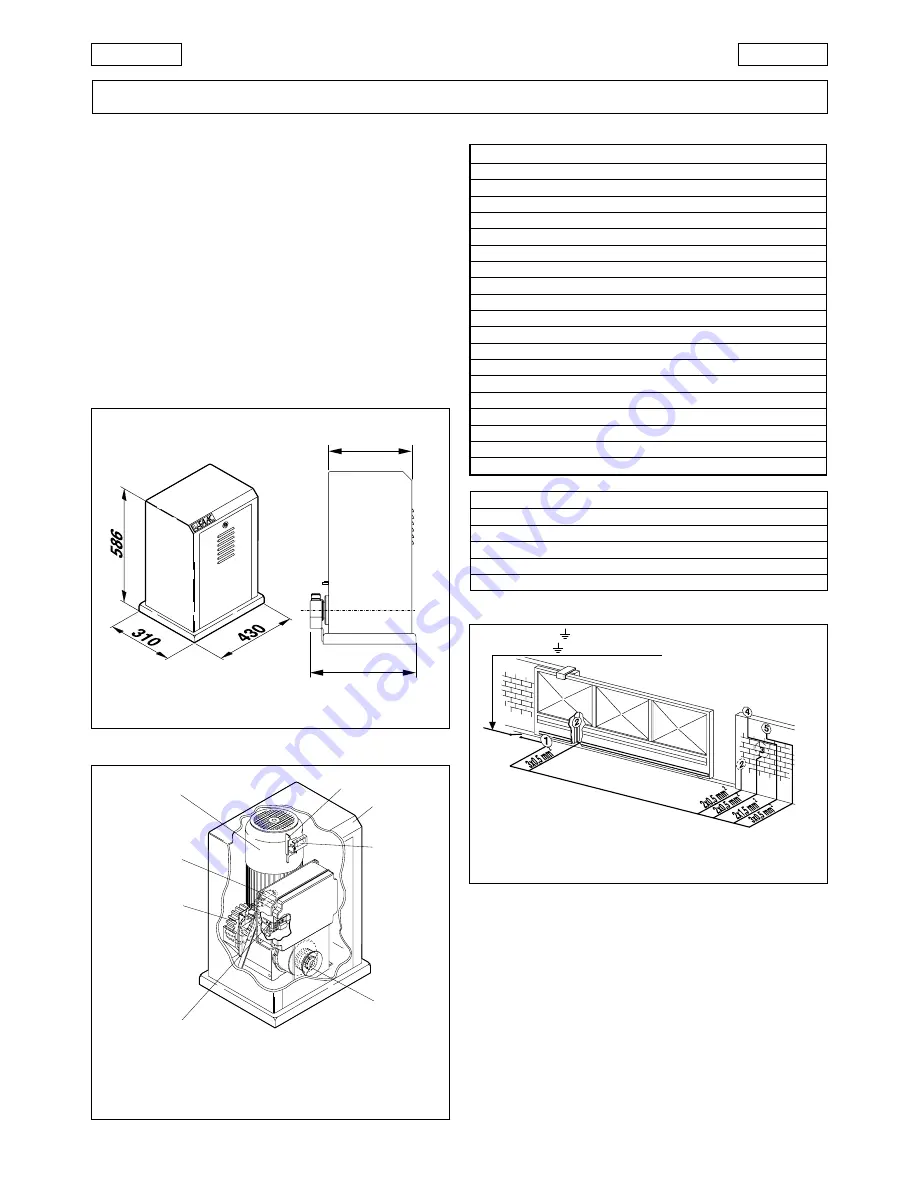
13
ENGLISH
ENGLISH
AUTOMATION 884 & 884 T
Values are expressed in mm.
Power supply
230V 3ph / 400V 3ph + N (+ 6 % - 10 %) 50Hz
Power consumption (W)
850
Reduction ratio
1 : 43.2
No. of pinion teeth CR
Z 16 - Rack 30x30 Module 6
Nominal torque Nm
155
Max. thrust N
3200
Duty rating
50% / 100% (2000 Kg)
Oil quantity (kg)
2
Temperature range
- 20 ÷ + 55 °C
Gear motor weight (kg)
50
Housing protection
IP 55
Max. gate weight (kg)
3500
Gate speed
10 m/min
Max. gate length
42 m
Clutch
Twin discs in oil bath
Housing treatment
cataphoresis
Casing painting
polyester RAL 2004
Control unit
884 T (incorporated)
Limit switches
mechanical
Gear motor dimensions LxHxD (mm)
see Fig. 1
Table 1 Technical specifications
3.
ELECTRICAL SET-UP
Fig. 3
Fig. 1
햲
884 operator with
884 T control unit
햳
Photocells
햴
Key switch
햵
Flashing light
햶
Radio receiver
280
354
RST
220V 4x2,5 mm
RSTN
380V 5x2,5 mm
2
2
Electric motor technical specifications
Power supply
230V (+ 6 % - 10 %) / 400V (+ 6 % - 10 %)
Frequency Hz
50
Current A
2.7 / 1.6
Power consumption kW
0.8
Motor speed rpm
1400
These instructions apply to the following models:
884 MCT
The FAAC model 884 automations for sliding gates are
electromechanical operators which transmit movement to the
leaf by means of a pinion with rack coupled in an appropriate
manner to the sliding gate.
By using a self-braking motor the system is guaranteed to be
mechanically locked when the motor is not in operation so a
lock does not need to be installed. The gear motors have
adjustable mechanical clutches to ensure correct use of the
automation. A convenient manual release device allows the
gate to be opened in the event of a power failure or malfunction.
The electronic control unit is incorporated in the gear motors.
The 884 automations have been designed and built for vehicle
access control in industrial areas. Do not use for any other
purpose.
4.
INSTALLING THE AUTOMATION
4.1.
PRELIMINARY CHECKS
For safe, correct operation of the automation, make sure that
the following requirements are met:
•
The gate’s structure must be suitable for automation. Take
special care to ensure that the wheels are large enough to
support the full weight of the gate, that a top runner is
installed and that mechanical limit stops are fitted to
prevent the gate from coming off the runner.
•
The characteristics of the ground must ensure sufficient
support for the foundation plinth.
•
There must be no pipes or electrical cables in the area to be
dug for installing the foundation plinth.
1.
DIMENSIONS
Fig. 2
햲
884 T electronic control unit
햳
Casing
햴
Electric motor
햵
Clutch adjustment screw
햷
Manual release device
햸
Manual release device safety microswitch
햹
Mechanical limit switch with roller
햺
Transmission pinion
6
2
7
1
4
8
3
9
2.
DESCRIPTION AND TECHNICAL SPECIFICATIONS