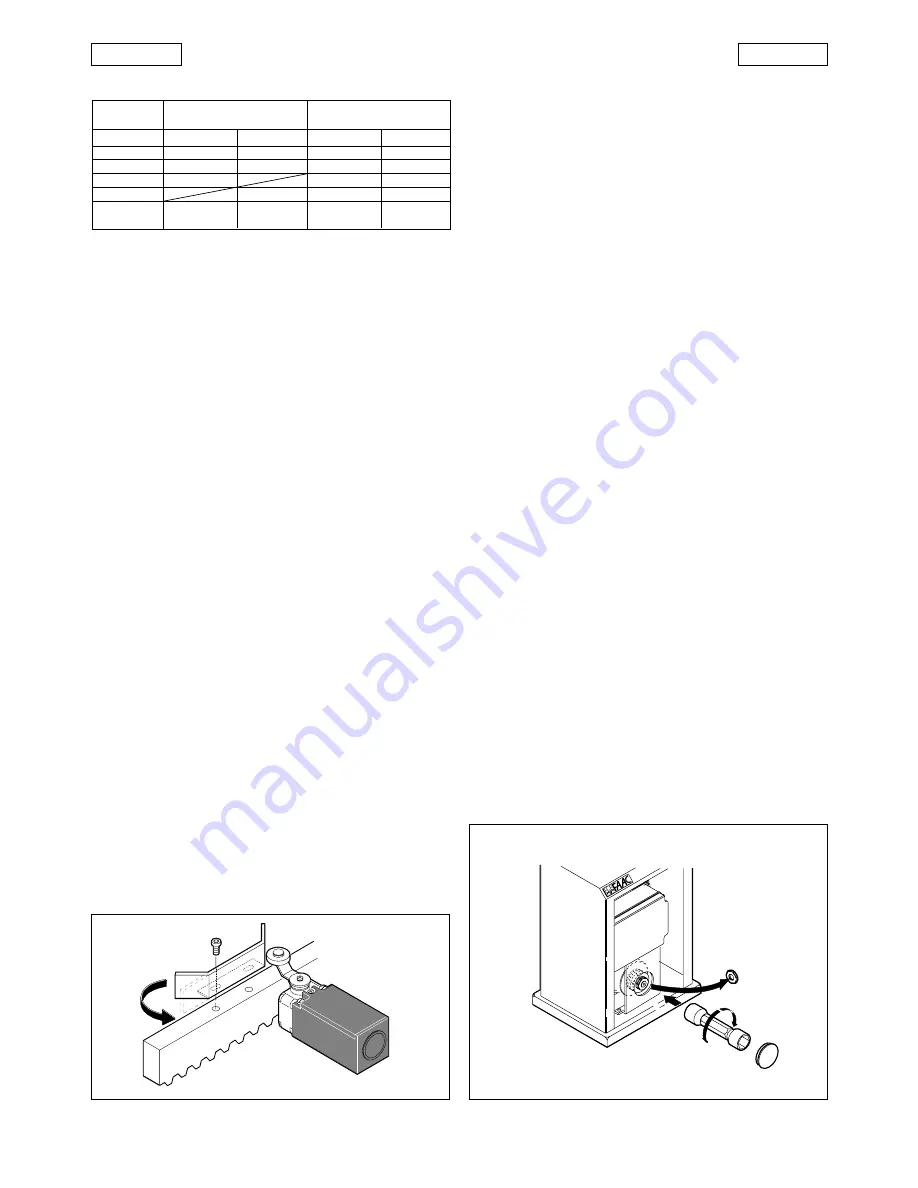
19
ENGLISH
ENGLISH
Fig. 21
Fig. 22
GATE STATUS
CLOSED
OPEN
CLOSING
OPENING
STOPPED
LOGIC C
CONTROLS HELD DOWN
CONTINUOUSLY
OPEN A (5)
opens
no effect
no effect
completes
opening
OPEN B (4 and 5)
no effect
closes
no effect
completes
closing
SAFETY DEVICES
no effect
prevents closing
stops movement
no effect
prevents
closing
STOP
no effect
no effect
stops movement
stops movement
no effect
TABLE 12
LOGIC C (DEAD-MAN)
PULSES
(1) OPEN B input controls partial opening.
(2) With pre-flashing selected, movement begins after 5 sec.
(3) If the pulse is sent during pre-flashing, counting is restarted.
(4) OPEN B input controls closing.
(5) Push-button must be kept pressed to activate gate movement. When
the push-button is released, the gate stops.
5.4.
FAULT CONDITIONS
The following conditions cause certain effects to normal
operation of the automated system:
햲
microprocessor error
햳
safety electronic timing tripped (operation is interrupted
if continuous work time exceeds 255 sec. ).
햴
limit
-
switches disconnected (or both engaged)
•Conditions
햲
and
햳
cause the automated system to stop and
nothing more.
•Condition
햴
causes an alarm situation disabling any activity:
Normal operation can be restored only after eliminating the
alarm cause and pressing the RESET push-button (or turning
off power supply momentarily).
To have this condition signalled, the indicator- light must be
connected: the alarm is signalled by very rapidly flashing
light (0.25 sec).
5.5.
POSITIONING LIMIT-SWITCH PLATES
The 884 operator has an electro-mechanical limit-switch with
roller and lever, which controls gate movement to stop when
a profiled plate, secured on the top of the rack, activates the
lever until the microswitch is tripped (fig. 21).
Procedure for correct positioning of the two limit-switch plates
supplied:
1) Power up the system.
2) Manually take the gate toward opening position, but leave it
5 cm from the required opening position.
3) Allow the plate to slide over the rack in opening direction.
As soon as the FCA limit-switch LED on the 884 T control board
(fig. 13) goes off, move the plate a further 10 mm and secure
it provisionally on the rack by two weld spots.
4) Manually take the gate to closing position, leave it 5 cm
from the limit stop.
5) Allow the plate to slide over the rack in closing direction.
As soon as the FCC limit-switch LED on the 884 T control board
(fig. 13) goes off, move the plate a further 10 mm and secure
it provisionally on the rack by two weld spots.
Note: The plates are designed for securing with screws (fig. 21)
if necessary.
The securing slot allows you to finely locate the limit-switch
position.
Important :
a) The plate must activate the limit-switch on the
profiled part as shown in figure 21.
b) To prevent the plate from going beyond the
limit-switch (long braking), we advise you to
straighten the final profiled part as shown in
fig.21.
6) Re-lock the system (see Chapter 8).
Important:
to prevent damage to the operator and/or
interrupting operation of the automated system, allow a
clearance of about 5cm between the limit-switch tripping
position and the required closing position.
5.6.
LIMIT-SWITCH CONNECTION CHECK
Manually take the gate toward opening position, and check if,
with the leaf open, the FCC LED is lighted and the FCA LED is off.
Manually take the gate toward closing position, and check if,
with the leaf closed, the FCA LED is lighted and the FCC LED is
off.
If the LEDs are inverted, changeover the cables connected to
terminals 12 and 13.
5.7.
ROTATION DIRECTION CHECK
1)
Release the operator, take it manually to mid-travel and
re-lock it (see Chapter 7 - 8).
2)
Power up the system and then press the RESET push-button.
3)
Give an Open command to the operator, check if the gate
moves in opening direction and then press the RESET push-
button to stop the leaf moving.
4)
If rotation direction is incorrect, changeover wiring of
cables T1 and T3 of the electric motor.
5.8.
SETTING THE MECHANICAL CLUTCH
To calibrate the transmitted torque adjustment system, refer to
fig. 22.
Remove the safety lid and the lock nut. Adjust the clutch using
a socket wrench (fig. 22).
Turn the nut clockwise to increase torque.
Turn the nut anticlockwise to decrease torque.
Activate the operator and check that the clutch is set to allow
the leaf to slide without being too dangerous.
Refit the lock nut and the safety lid.