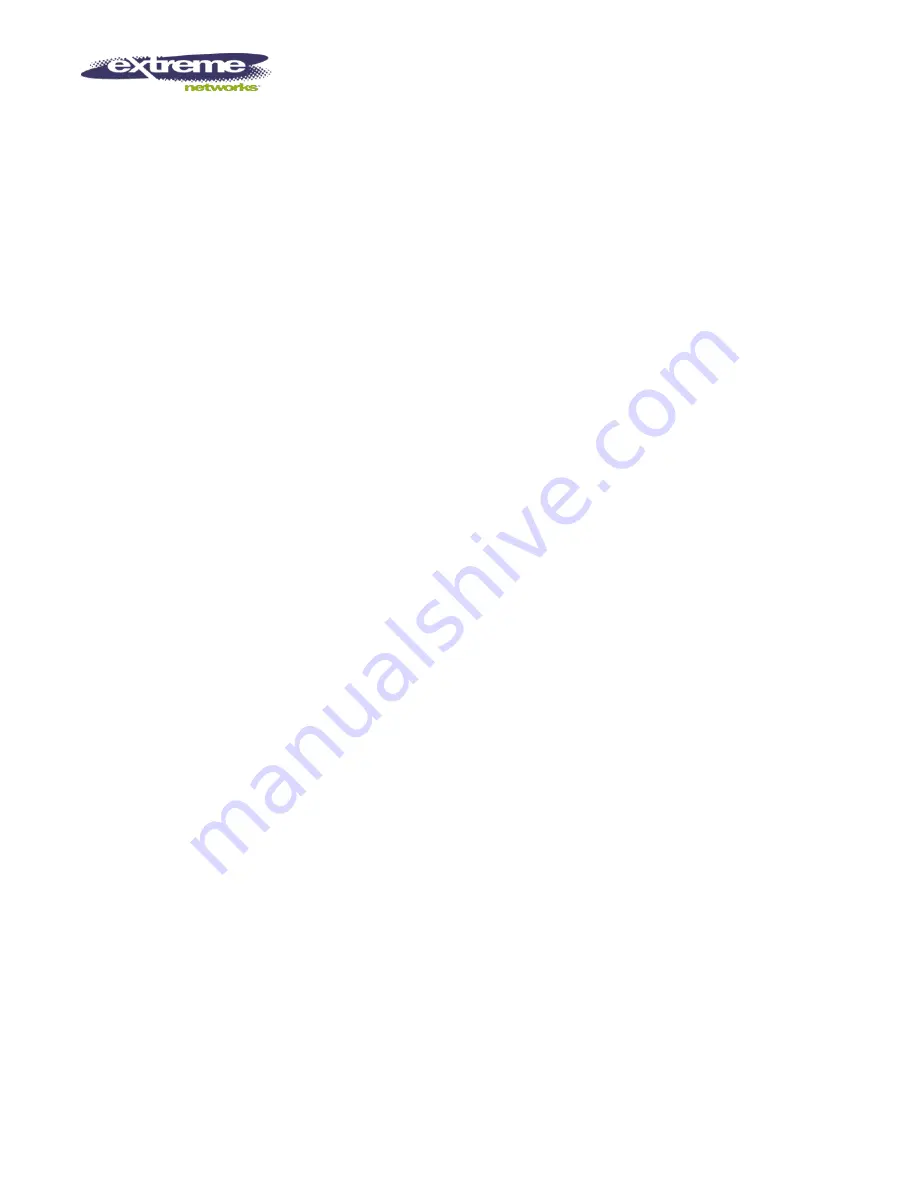
Doc. #: 1.02.L01
Extreme Networks, Inc.,
copyright, 2009
Page 8 of 11
Rev. R03, 28-Apr-09
Printed Copy is Uncontrolled
Owner: Corporate Quality
♦
Test & Evaluation:
This phase ensures overall readiness for initial product shipments. The
product, documentation, testing methods, and manufacturing processes are validated. All
hardware and software is made Generally Available upon exit of this phase.
♦
Optimization
: The Optimization phase introduces the product to the market and verifies how
well the product meets its performance goals, quality criteria, sales projections, revenue or
profit objectives, order processes, and cost projections from initial ramp-up to volume
production. For hardware products, all optimization activities are completed during this
phase. For software products, code is released to manufacturing at the end of this phase.
♦
Sustaining:
The Sustaining phase begins after the Optimization phase is completed and
encompasses all activities required for successful sale and deployment of the product until an
end-of-life decision.
♦
End-of-Life:
The End-of-Life phase encompasses the activities required to discontinue
production of a product. Warranty obligations, when applicable, are honored. As needed, a
product transition plan is developed to support customers through platform upgrades or
changes. Typically, the hardware service period extends for five (5) years past the published
end-of-sale date.
9.2
Product Development Elements
♦
Planning:
Project development plans include: product functionality and features, the
organizational relationships and responsibilities of the development team, and required
resources and project activities. Plans are updated as the design evolves to document verified
project milestones.
♦
Inputs:
Design input is based on customer input and internal research of potential market
opportunities. Design input documents are maintained by the appropriate project manager for
the duration of the development
effort.
♦
Outputs:
Design output is documented as product manufacturing specifications, drawings,
acceptance tests, and regulatory compliance reports. Each development team ensures design
output meets the design input requirements through peer- and cross-functional reviews.
Released and approved documents provide information for purchasing, production, delivery,
deployment, customer-use, and service.
♦
Review:
Design review meetings are held regularly throughout the development phase to
ensure the product meets performance requirements, customer expectations, regulatory
requirements, and manufacturability standards. Review minutes with any follow-up actions are
documented and maintained as part of the project file. Scheduled reviews are also held with
selected customers and supply-chain partners throughout the development and test phases.
♦
Verification & Validation:
Design verification establishes that product functional parameters
conform to design requirements. Engineering prototype tests evaluate product functionality
against established specifications. Compliance testing to safety and environmental standards,
contractual requirements, product reliability goals, and external agency certifications are
completed prior to the release of the product. The Technical Marketing group evaluates the
product based on its intended uses(s) in a customer environment. This group also assists with
customer beta trials and product demonstrations.