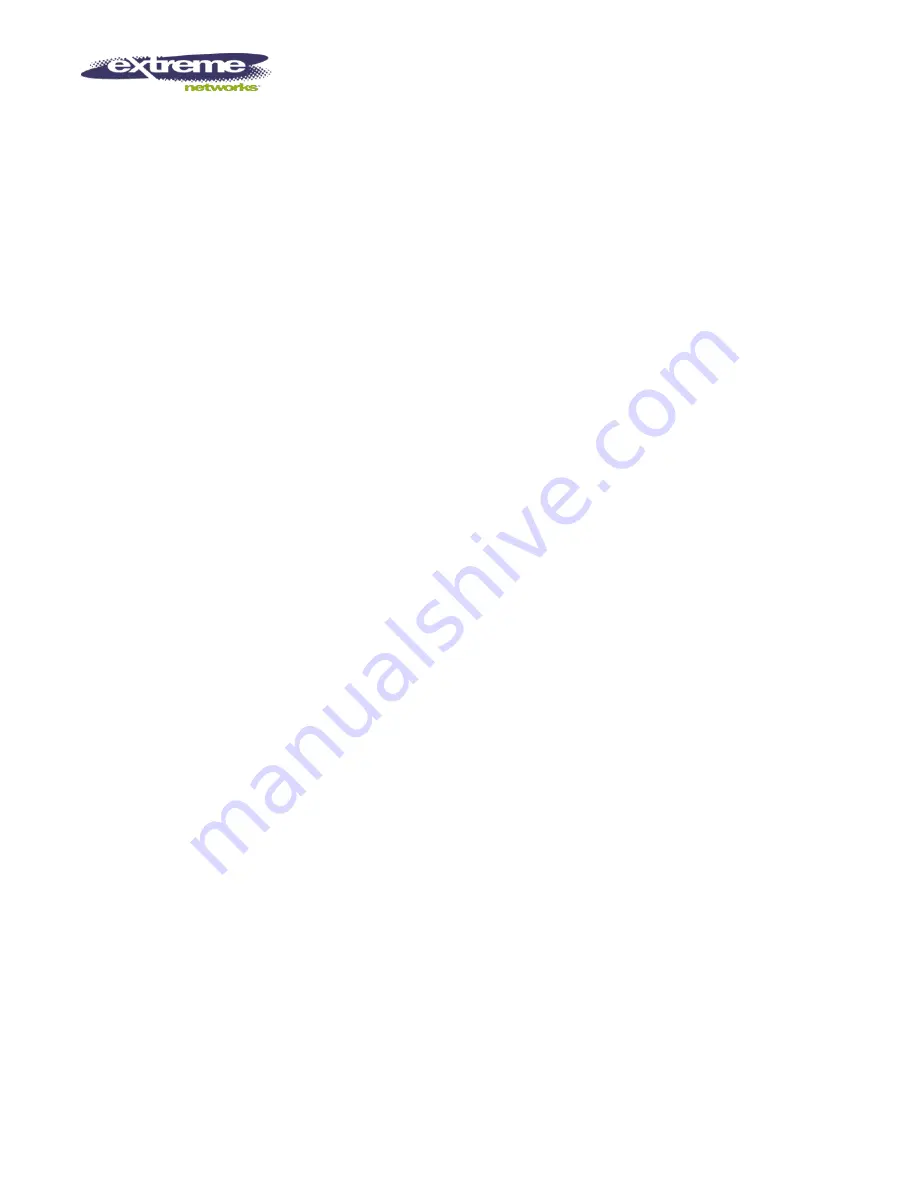
Doc. #: 1.02.L01
Extreme Networks, Inc.,
copyright, 2009
Page 9 of 11
Rev. R03, 28-Apr-09
Printed Copy is Uncontrolled
Owner: Corporate Quality
9.3
Manufacturing & Production:
Extreme Networks outsources manufacturing to qualified Contract
Manufacturer (CM), and Joint / Original Design Manufacturer, (JDM / ODM) partners. Per
agreements with various manufacturing partners, material used in production is inspected prior to use.
Non-conforming materials are segregated for review and disposition. Appropriate product handling
is maintained at all production stages to prevent damage. Compliance with workmanship standards is
confirmed through inspection results and supplier reports. Relevant processes are managed and
monitored to confirm compliance to safety, environmental, and other agency standards.
9.4
Services:
The Services team manages post-product-delivery service, including: customer queries,
warranty and technical support, professional services and technical training. Customers’ technical
issues are addressed by qualified technical support representatives for evaluation and timely
resolution.
10.0
Supply Chain Partnerships
10.1
Supplier Qualification:
Extreme Networks evaluates and selects supply chain partners on the basis of
their ability to meet established requirements. Qualification is defined and performed by a team
consisting of subject matter experts from Purchasing, Operations, and Engineering. Extreme
Networks’ manufacturing partners all hold ISO-9001 and ISO-14001 certifications for their quality
and environmental management systems.
10.2
Supplier Partnership:
Extreme Networks expects its suppliers to provide defect-free products and
services that conform to requirements. Extreme Networks is responsible for ensuring requirements
are clearly defined, and communicated in an effective and timely manner. Extreme Networks works
with suppliers committed to continual improvement in their own quality system, and to a relationship
with Extreme Networks.
10.3
Supplier Performance:
Supplier performance is measured on a continual basis with key metrics
evaluated against established goals. Performance issues are reviewed by the Operations team.
Periodic communication meetings are held with key suppliers to ensure alignment with corporate
objectives. Continual improvement activities are used to address issues or to improve organizational
efficiencies and performance.
10.4
Supplier Review:
Per an established schedule, approved suppliers are reviewed to ensure their on-
going ability to meet established quality requirements. This review includes performance metrics,
workmanship, account management, product delivery, communication, and technical capability. The
scope and timing of these reviews is based on the nature of the supplier relationship, and their impact
to the business.
11.0
Operational Requirements
11.1
Production Materials:
Purchase Orders contain the information required to clearly identify the
product or service ordered. When needed, supporting data is included (drawings, specifications,
standards). Purchasing documents are reviewed for adequacy prior to use for quotations and/or
purchases. The Receiving department ensures the product received conforms to order requirements.
11.2
Identification & Traceability:
All material is identified on receipt by an item number, attached label,
or marking on the material. Serial number, part number, and product name identify finished products.
Products are identified at delivery by packing lists and external markings on shipping container(s).
Test stamps, serial numbers, and customer order numbers ensure traceability through production,
delivery, and service.