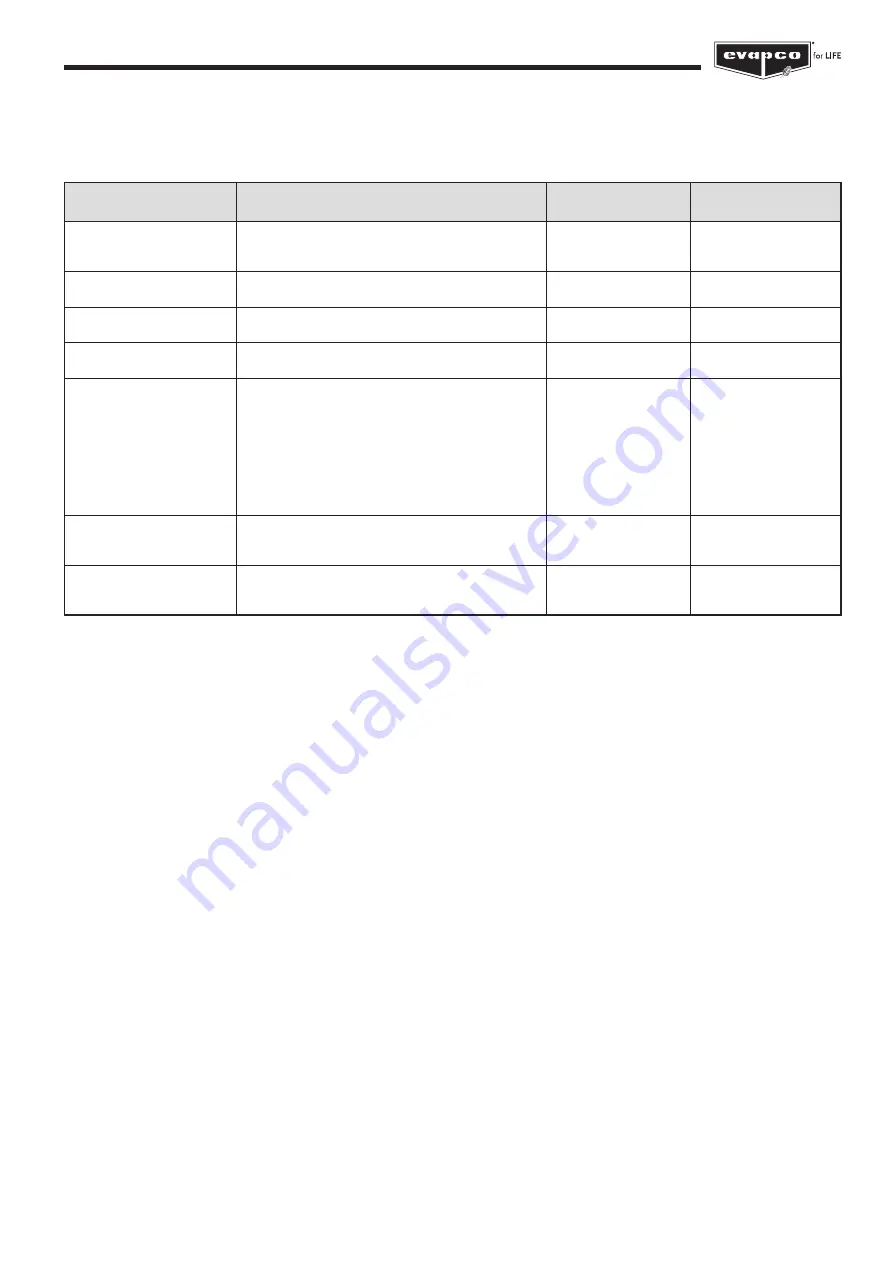
9
Operation and Maintenance Instructions
Operating Level of Water in Cold Water Basin
The operating level should be checked monthly to make sure the water level is correct. Refer to
Table 2
for unit specific levels.
Evaporative Condenser
Model Number
Closed Circuit Cooler Footprint
Operating Water Level*
(inch)
Operating Water Level*
(mm)
ATC-E Products
50E to 165E,
170E to 3714E
ATWB, eco-ATW & eco-ATWE Products
3’ and 4’ wide units**
8.5’ wide to “7’ wide thru 24’ wide”
9”
11”
229
279
ATC-DC
8.5’ Wide to 24’ Wide
11”
279
eco-ATC Products
122A to 3846A
eco-ATWB-E
8.5’ wide thru 24’ wide
11”
279
LRC Products
25 to 379
LRWB Products
3’ wide thru 8’ wide units
8”
203
LSC-E Products
36 to 170
185 to 385
400 to 515, 800 to 1030
550 to 805, 1100 to 1610
PMC-E, eco-PMC
175E to 375E, 183 to 387
332E to 2019E, 275 to 2191
LSW Products
4’x6’ thru 4’x12’
5.5’x12’, 5.5’x18’
8’x12’, 8’x24’, 10’x12’, 10’x24’
8’x18’, 8’x36’, 10’x18’, 10’x36’
11”
11”
12”
15”
10”
14”
279
279
305
381
254
356
—
ESW4 Products
8.5’ and 14’ wide units
12’ wide unit
9”
10”
229
254
PHC-E Products
S-79 to S-1236
D-1224 to D-2826
9”
10”
229
254
Table 2
- Recommended Operating Water Level
* Measured from lowest point on basin floor.
** Not available on eco-ATWE.
At initial start up or after the unit has been drained, the unit must
be filled to the overflow level. Overflow level is above the normal
operating level and accommodates the volume of water normally
in suspension in the water distribution system and the riser piping.
The water level should always be above the strainer. Check by
running the pump with the fan motors off and observing the water
level through the access door or remove the air inlet louver.
Water Make Up Valve
A mechanical float valve assembly is provided as standard
equipment on the evaporative cooling unit (unless the unit has
been ordered with an optional electronic water level control
package or the unit is arranged for remote sump operation).
The make up valve is easily accessible from outside the unit
through the access door or removable air inlet louver. The
make up valve is a bronze valve connected to a float arm
assembly and is activated by a large foam filled plastic float.
The float is mounted on an all-thread rod held in place by wing
nuts. The water level in the basin is adjusted by repositioning
the float and all-thread using the wing nuts. The bottom center
of the float should be set at 1” (25mm) below the middle of the
overflow. At its highest point, float arm should be parallel to
the water level.
The make up valve assembly should be inspected monthly
and adjusted as required. The valve should be inspected
annually for leakage and if necessary, the valve seat should
be replaced. The make up water pressure for the mechanical
valve should be maintained between 140 and 340 kPa.
Drift Eliminators
Check the drift eliminators quarterly to make sure the drift
eliminators are still in the correct position and not clogged
by any debris. If required after inspection, drift eliminators
must be removed, cleaned and reinstalled correctly.On forced
draft models, the worker must use personal precautions
and adequate safety measures against the risk of a fall,
in accordance with local regulations. Remove one or two
eliminator sections from the top of the unit, protect the fill by
use of a hard board before entering the unit and walking on
the fill. Never walk on the eliminators! Once standing on the
fill, the remaining drift eliminators can be removed. On induced
draft models, lifting handles are provided along the top
layer of eliminators. Remove one or two eliminator sections,
protect the fill by use of a hard board before entering the unit
and walking on the fill. Never walk on the eliminators! Once
standing on the fill, the remaining drift eliminators can be
easily removed through the access door.
Pressurized Water Distribution Systems
Check the water distribution system monthly to make sure it
is operating properly. Always check the spray system with the
pump on and the fans off (locked and tagged out).
On forced draft models, remove one or two eliminator sections
from the top of the unit and observe the operation of the water
distribution system.
On induced draft models, lifting handles are provided along
the top layer of eliminators. Eliminators can be easily removed