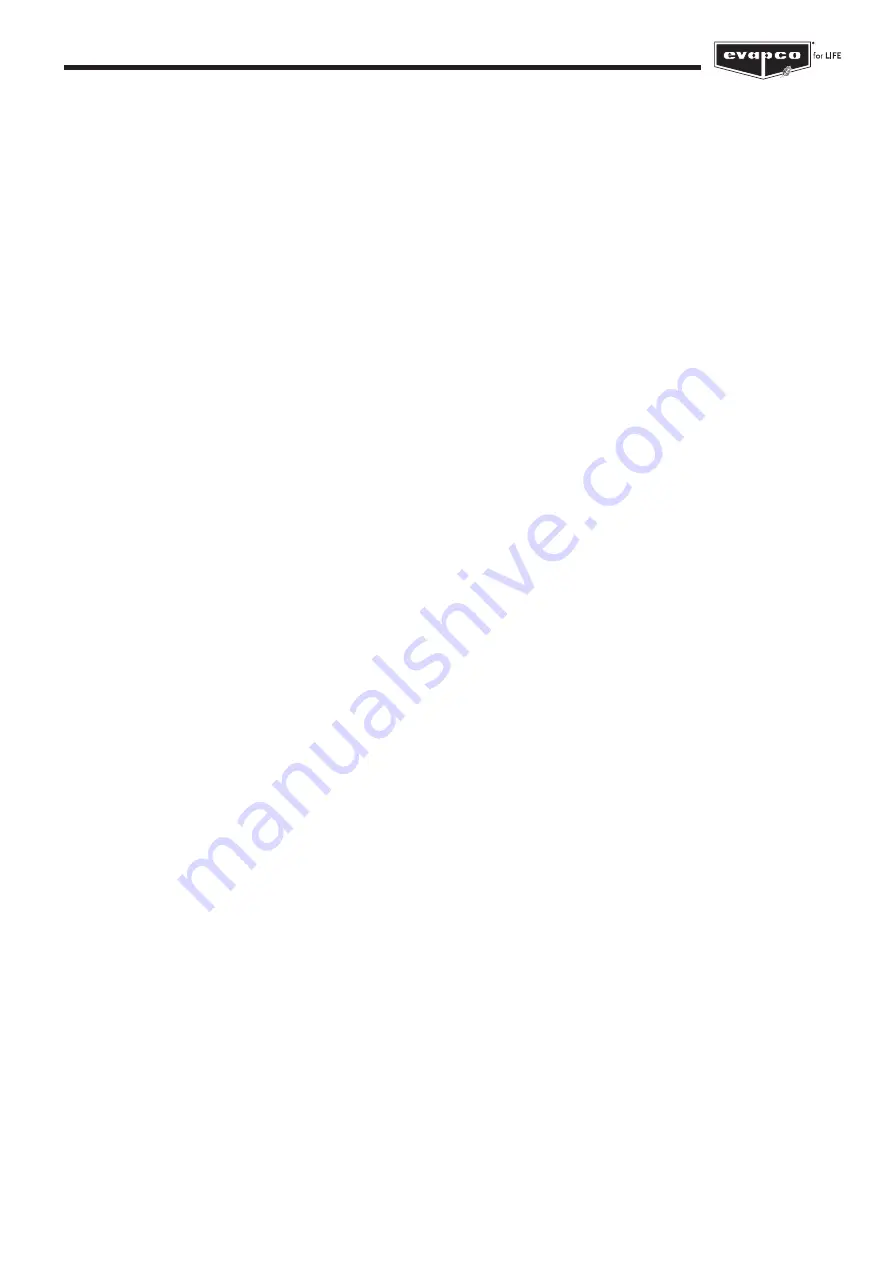
7
Operation and Maintenance Instructions
2. Two Speed Motors
The use of a two-speed motor provides an additional step
of capacity control when used with the fan cycling method.
The low speed of the motor will provide approximately
60% of full speed capacity.
Two-speed capacity control systems require not only a two-
speed motor, but also a two-stage thermostat and the proper
two-speed motor starter.
It is important to note that when two-speed motors are to
be used, the motor starter controls must be equipped with
a decelerating time delay relay. The time delay should be a
minimum of a 30 second delay when switching from high
speed to low speed.
3. Variable Frequency Drives
The use of a variable frequency drive (VFD) provides the
most precise method of capacity control. A VFD is a
device that converts a fixed AC voltage and frequency into
an adjustable AC voltage and frequency used to control
the speed of an AC motor. By adjusting the voltage and
frequency, the AC induction motor can operate at many
different speeds.
VFD technology has particular benefit on evaporative
cooling units operating in cold climates where airflow can
be modulated to minimize icing and reversed at low speed
for de-icing cycles. Applications using a VFD for capacity
control must also use an inverter capable motor built in
compliance with NEMA standard MG-1.
The VFDs need to have a pre-set shutoff to prevent water
temperatures from becoming too cold and to prevent
the drive from trying to turn the fan at near zero speed.
Operating below 25% of motor speed achieves very little
return in fan energy savings and capacity control. Check
with your VFD supplier if operating below 25% is possible.
NOTE
:
Pump Motors: VFD’s should not be used on pump
motors. The pumps are designed to be operated at full
speed and are not intended to be used as capacity control.
The type of motor, manufacturer of the VFD, motor lead
lengths (between the motor and the VFD), conduit runs and
grounding can dramatically affect the response and life of
the motor. Select a high quality VFD that is compatible with
the fan motor(s) in the EVAPCO unit(s). Many variables in
the VFD configuration and installation can affect motor and
VFD performance. Two particularly important parameters
to consider when choosing and installing a VFD are
switching frequency and the distance between the motor
and VFD often referred to as lead length. Consult the VFD
manufacturer’s recommendations for proper installation
and configuration. The motor lead length restrictions
can vary with the vendor. Regardless of motor supplier,
minimizing lead length between the motor and drive is
good practice.
VFD Lockout Notification
Sequence of Operations / Guidelines for Multi-fan Units with a
VFD during Peak Load
For eco-ATWE, see Sage
2
/Sage
3
control Panel O&M:
1. Both fan motors off – Pump running on one cell.
2. Both fan motors off – Pump running on both cells.
3. Both VFDs turn on at the manufacturer’s recommended
minimum operating speed (25%) – Pump running on both
cells.
4. Both VFDs speed up uniformly (they should be
synchronized on start-up) – Pump running on both cells.
5. Both VFDs are on full speed – Pump running on both cells.
NOTE
:
The VFDs need to have a preset shutoff to prevent
water temperatures from becoming too cold and to prevent
the drive from trying to turn the fan at near zero speed.
Operating below 25% of motor speed achieves very little
return in fan energy savings and capacity control. Check with
your VFD supplier if operating below 25% is possible.