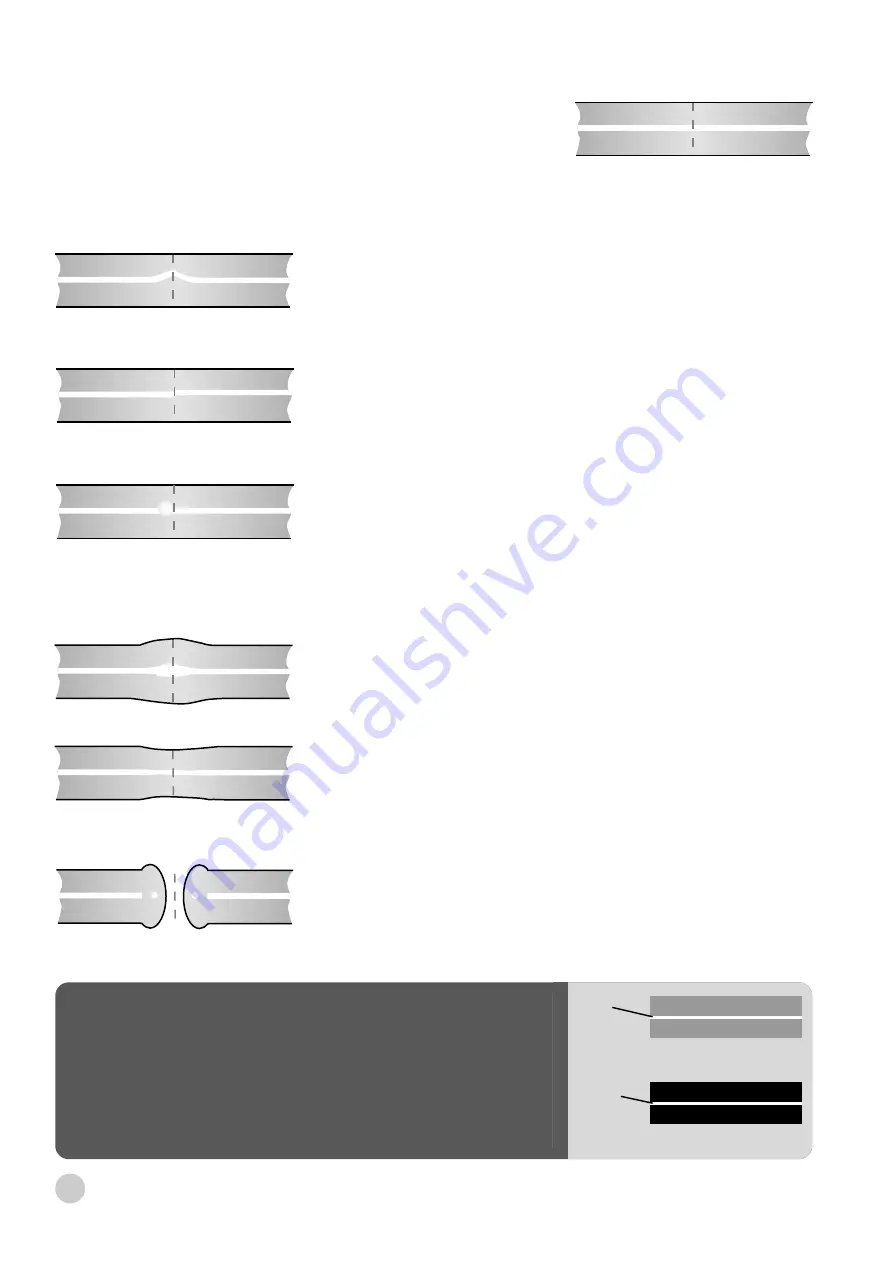
22
Cold image and basic hot image analysis
The best thing to have in your mind as you look at the images
after splicing is a representation of a successful splice, such
as the one here. The thing to note in particular is that the
core and the outer edges form straight lines. If your splice
does not look like this, you should check for one of the com-
mon splice defects shown below.
Bent core
This is when the core, rather than form a straight line, bends
at the splice point. A bent core is most often caused by a
bad cleave, and is thus a problem that can be remedied by
careful re-preparation of the fibers.
Example of a successful splice
Core offset
This is where the cores of the original fibers do not line up,
even though their claddings do. This is most often the result
of fibers with large core eccentricity, and you should use the
Hot core or Small core alignment process with them when re-
splicing.
Hot spot
A hot spot shows up as a bright point on the fiber. It can be
the result of a variety of factors: dirt on the fiber, poor cleav-
ing, or air bubbles inside the fiber. When a hot spot is lo-
cated outside the core, it reduces splice strength, when
inside the core, it also contributes to higher splice loss. The
best action to take is to carefully re-prepare the fibers.
Bulge
A bulge in the outer diameter usually indicates that you have
used the wrong splicing program parameters, so you should
check the program you are using before re-splicing.
Throughout the splicing process, but especially during
visual splice evaluation it is important to keep in mind the
following: Whereas the white line one sees in hot images
is the core, it is NOT in cold images. Rather, the white line
one sees in a cold image is nothing more than the result of
the round fiber acting as a lens and focusing the light
shining through it.
core
focused
back-
ground
light
Hot image of fiber
Cold image of fiber
BASIC OPERATION - Splice evaluation
Waisting
When the splice area is thinner than the fiber diameter, it
means that either the fusion current was too high or that the
fibers did not overlap sufficiently during splicing. You should
check the program parameters before re-splicing.
Matchsticking
A number of problems can cause matchsticking. The most
common causes are excessive fusion currents, dirty elec-
trodes, and presence of primary coating left on the fibers.
You should check these things and re-splice.