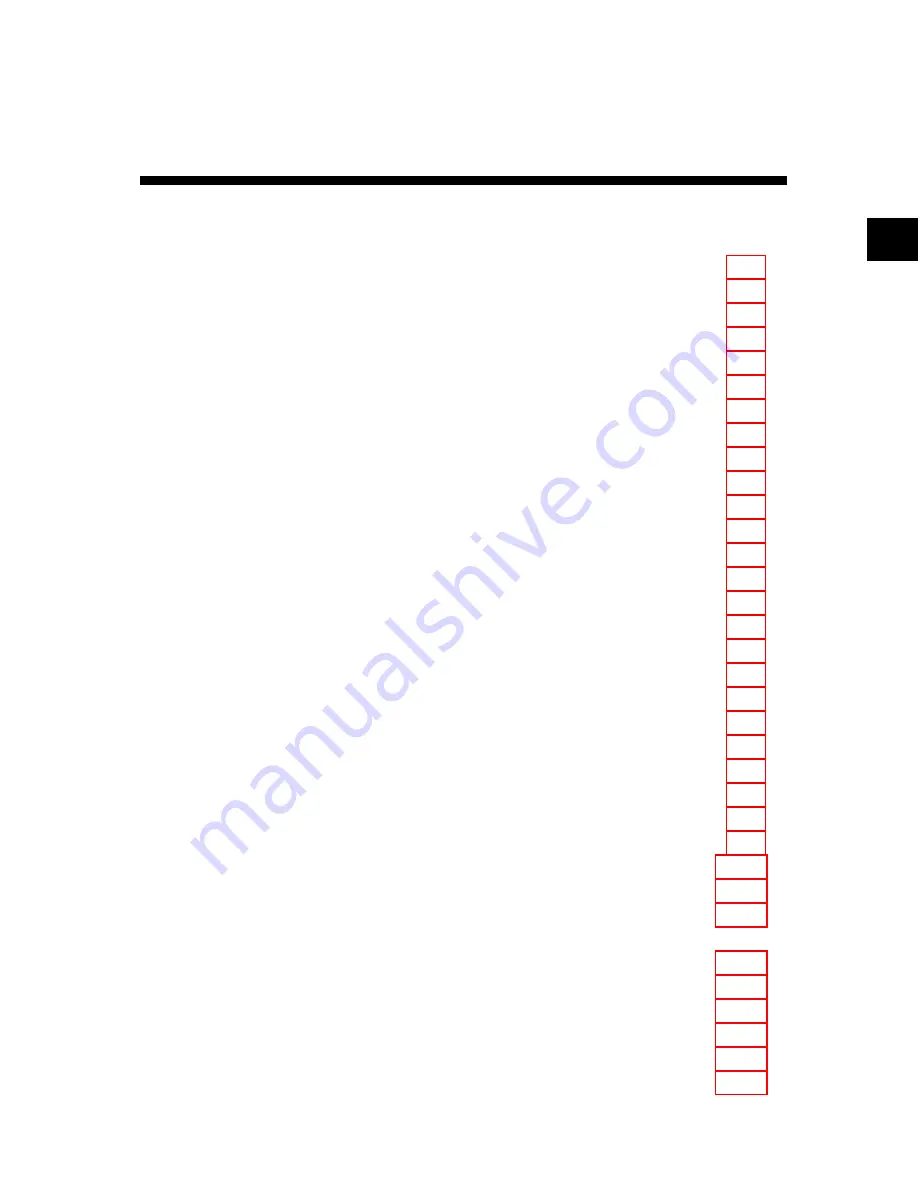
FEATURES AND GENERAL SPECIFICATIONS
1
CONTENTS
FEATURES ................................................................................
GENERAL SPECIFICATIONS ...................................................
1.2.1 Printing Specifications ..................................................
1.2.2 Character Specifications ...............................................
1.2.3 Paper Specifications .....................................................
1.2.4 Paper Roll Supply Device .............................................
1.2.5 Journal Paper Take-up Mechanism ..............................
1.2.6 Electrical Specifications ...............................................
1.2.7 Ribbon Cassette ............................................................
1.2.8 Dimensions, Weight, Finish ..........................................
1.2.9 Environmental Specifications.......................................
1.2.10 Reliability ........................................................................
1.2.11 Certifications ..................................................................
HARDWARE CONFIGURATION ...............................................
1.3.1 Main Unit Configuration ................................................
1.3.2 Main Unit Specifications ...............................................
Paper feed motor ...........................................................
Carriage motor ...............................................................
Print head unit (print solenoids) ...................................
Paper roll near-end sensor ...........................................
Cut sheet sensor (TOF/BOF sensor) ............................
Cover-open sensor ........................................................
Home position sensor ...................................................
Carriage motor out-of-phase state sensor ..................
1.3.3 Connectors .....................................................................
1.3.4 Interface .......................................................................... 1-11
1.3.5 Switches and Buttons ................................................... 1-13
CONFIDENTIAL
Summary of Contents for U375 - TM B/W Dot-matrix Printer
Page 2: ...Technical manual TM U375 U375P English 4005791 Copied Date 199 Copied by ...
Page 54: ...2 23 Figure 2 44 Host Interface Circuit and Custor Display Interface Circuit CONFIDENTIAL ...
Page 58: ...2 27 Figure 2 49 Carriage Motor Drive Signal Timing Chart CONFIDENTIAL ...
Page 149: ...6 2 Circuit 1 CONFIDENTIAL ...
Page 150: ...6 3 Circuit 2 CONFIDENTIAL ...
Page 151: ...6 4 Circuit 3 CONFIDENTIAL ...
Page 152: ...6 5 Circuit 4 CONFIDENTIAL ...
Page 153: ...6 6 Circuit 5 CONFIDENTIAL ...
Page 154: ...6 7 Circuit 6 CONFIDENTIAL ...
Page 156: ...6 9 CONFIDENTIAL ...
Page 157: ...6 10 CONFIDENTIAL ...
Page 158: ...6 11 CONFIDENTIAL ...
Page 159: ...6 12 CONFIDENTIAL ...
Page 168: ...7 9 Table 7 5 TM U375P Gate Array Pin Assignment continued CONFIDENTIAL ...
Page 174: ...CONFIDENTIAL ...
Page 175: ...CONFIDENTIAL ...
Page 176: ...7 17 CONFIDENTIAL ...
Page 177: ...7 18 CONFIDENTIAL ...
Page 178: ...7 19 CONFIDENTIAL ...
Page 179: ...7 20 CONFIDENTIAL ...