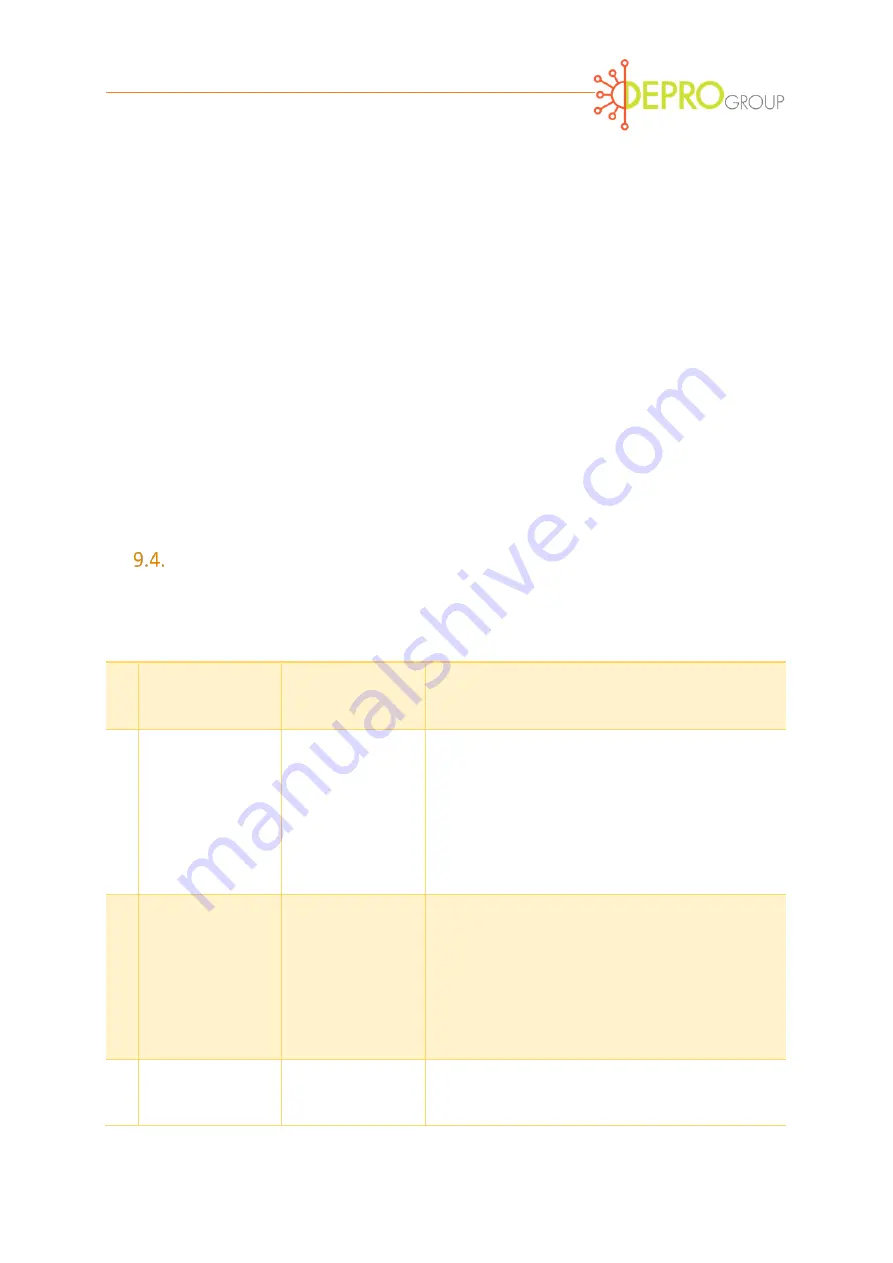
pressure during milling are to be eliminated to reduce failure. In difficult conditions
with adhesive related materials cleaning frequency may need to increase.
The cutting edges of the tool are intact. Dull or damaged cutting edges lead to
unfavorable milling results. Likewise, heavily worn running surfaces or copper deposits
in the holder can lead to errors. In case of doubt it is always advisable to replace the
part.
Re-sharpening of the blades is not recommended, especially if the cutting plate has
flakes, cracks or breaks.
The cutting properties of the tool change with each re-sharpening. The cutting ability
of the tool is determined by the clearance angle of the cutting edge and the protrusion
on the running surface in the holder.
When re-sharpening, coatings may be compromised, reducing life cycle.
Overview of maintenance intervals:
Table 5
Interval
Module/part
Measure
1
100
or
shift
change
Electrodes
Visual inspection of the milling result. If the
caps are not milled correctly, replace the tool
2
3,000 – 5,000
milling cycles or
monthly
Reservoirs Tool
Milling unit with
chip disposal
Visual inspection of the milling tool. If the caps
are not milled properly, replace the tool Empty
the collection container Cleaning the milling
tool and the chip removal. Clean the bayonet
mount before inserting the tool
3
30,000
milling
cycles or semi-
annually
Tool Milling unit
with
chip
disposal
Cleaning and checking the milling tool. Replace
if required. When cutting tools usually enough.
The replacement of the cutting plate. Replace
and check the suction. Exchange cover if
required.
4
Annually
Electrode milling Check pneumatics for leaks Check clamping
elements for cracks. Check screw connections