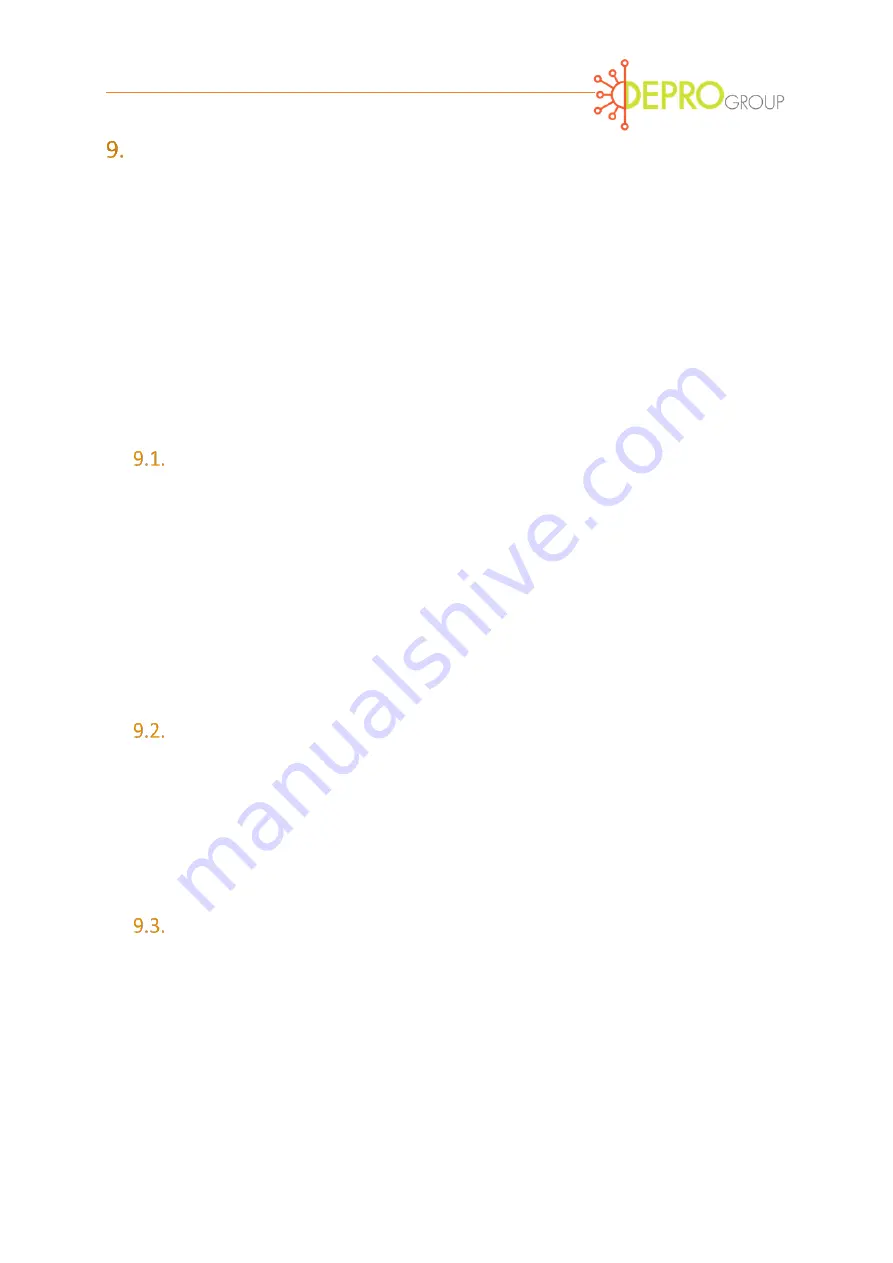
Maintenance:
Compliance the maintenance cycles is essential for the safe operation of the electrode
cutter / milling tool. Material residues in the tool as well as chip removal limit the process
reliability. Regular maintenance, including cleaning of the equipment at the critical points
prevents issues with the welding process.
Some devices wear and contaminate faster than others due to the welding application. The
following information is a guideline only. Responsible maintenance staff is required to check
problem areas more frequently, if necessary.
Inspection of magazine cartridges (2-3 days):
In general, the welding electrodes are changed once at the end of the shift or at the beginning
of the next shift. It is recommended that the system be programmed so that after the last
welding cycle electrodes are milled before being replaced. The maintenance staff can review
the milling performance after the electrode exchange to determine whether the blade of the
milling tool requires replacement.
Inspection of changing canisters (monthly):
It is recommended that every 2-4 weeks the collection canisters have be emptied on the
suction units or more frequently depending on electrode usage and debris collection. The
containers collect both caps and milling debris and are emptied by toggling the spring loaded
pins.
Care of the milling tools:
The functionality of the electrode milling tool and thus also the process reliability of the entire
spot welding system is ensured if:
The degree of contamination in the milling tool which will jeopardize its functionality.
Defective chip removal (blow-off), too long a milling cycle or excessive guns closing