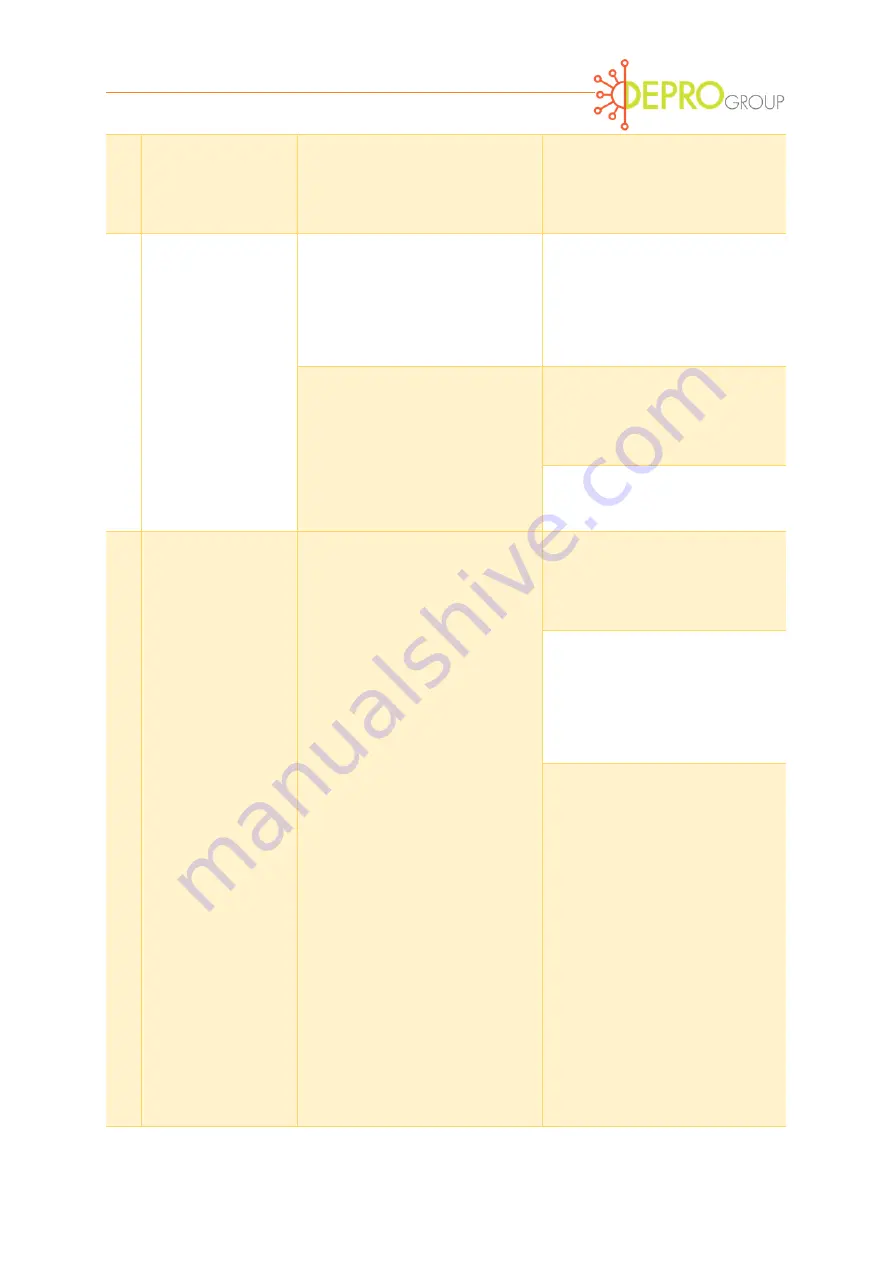
13 Chips
are
not
completely
removed.
Milling device stops when the
gun still in closed position
Ensure that the milling tool
does not stop until the welding
gun is opened.
14 In the middle of
the electrode weld
face, a small burr
forms.
The effect is usually due to
system inserts and smaller
burrs in milling inserts with Y-
blade and insert.
Please refer to 9
Imprecise retraction of the
welding gun.
Reduce milling time (milling in
2 short intervals) and increase
cutting speed.
Check
programming
and
correct if necessary.
15 With
flat
electrodes
ISO
Form A or C, the
effective surface is
not milled cleanly.
During welding, the active
surface
has
funnel-shaped
deformation. It has built up a
strong diffusion layer.
Therefore, gradually increase
the milling time and the closing
pressure.
Check whether the required
welding spot diameter can be
achieved
with
a
smaller
effective surface diameter.
Check whether the desired
welding result can also be
achieved with a slight radius
instead of a flat effective area
(40 mm). Note: With plan-
milled
electrodes,
crater
formation or retarding of the
active-surface center is faster.
Furthermore, these electrodes
are less tolerant when tilting
the welding gun.